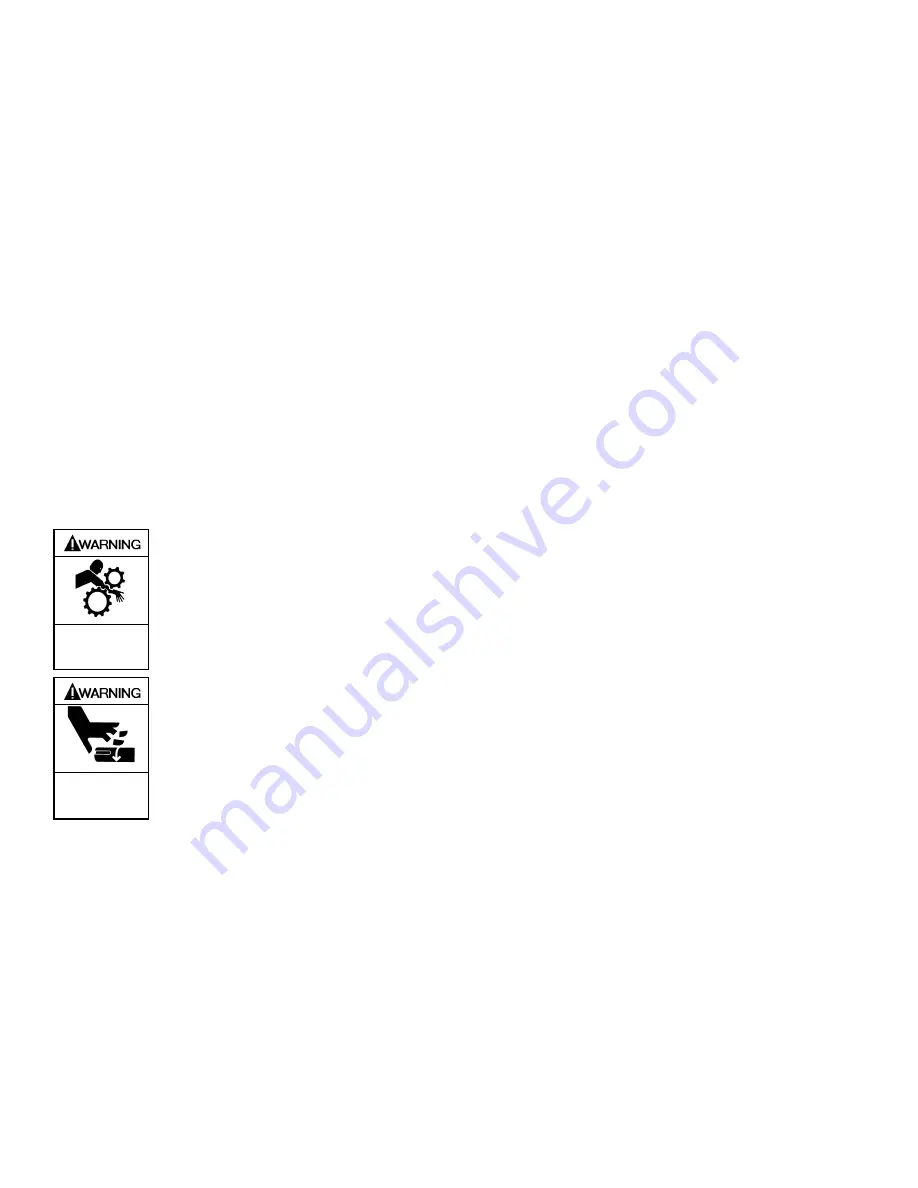
501-A00 Page 10/12
MAINTENANCE:
RELIEF VALVE ASSEMBLY
1. Insert the valve (9) into the relief valve bore of the casing
with the small end inward.
2. Install relief valve disc (9A) into relief valve.
3. Install the relief valve spring (8) in the valve bore.
4. Install new O-ring (4A) on spring guide (7).
5. Install spring guide (7) in valve bore of cylinder, aligning
spring (8) on spring guide during assembly.
6. Install new O-ring (10) in O-ring groove in relief valve cap
(4).
7. Apply a thin coat of grease on threads of relief valve cap
(4) and install in cylinder (12).
8. Screw the relief valve adjusting screw (2) with locknut (3)
into the valve cover (4) until it makes contact with the
spring guide (7).
9. After the relief valve has been adjusted, tighten the
Locknut (3)
NOTICE:
The relief valve setting MUST be tested and adjusted
more precisely before putting the pump into service.
Refer to "Relief Valve Setting and Adjustment"
10. Refer to “Pre-Start Up Check List” and “Start Up
Procedures” sections of this manual prior to restarting
pump operation.
Operation without guards in place can
cause serious personal injury, major
property damage, or death.
Do not operate
without guard
in place
Failure to adjust guards covering all
rotating part, allowing only a safe gap,
can cause personal injury or death
Do not operate
without guard
in place