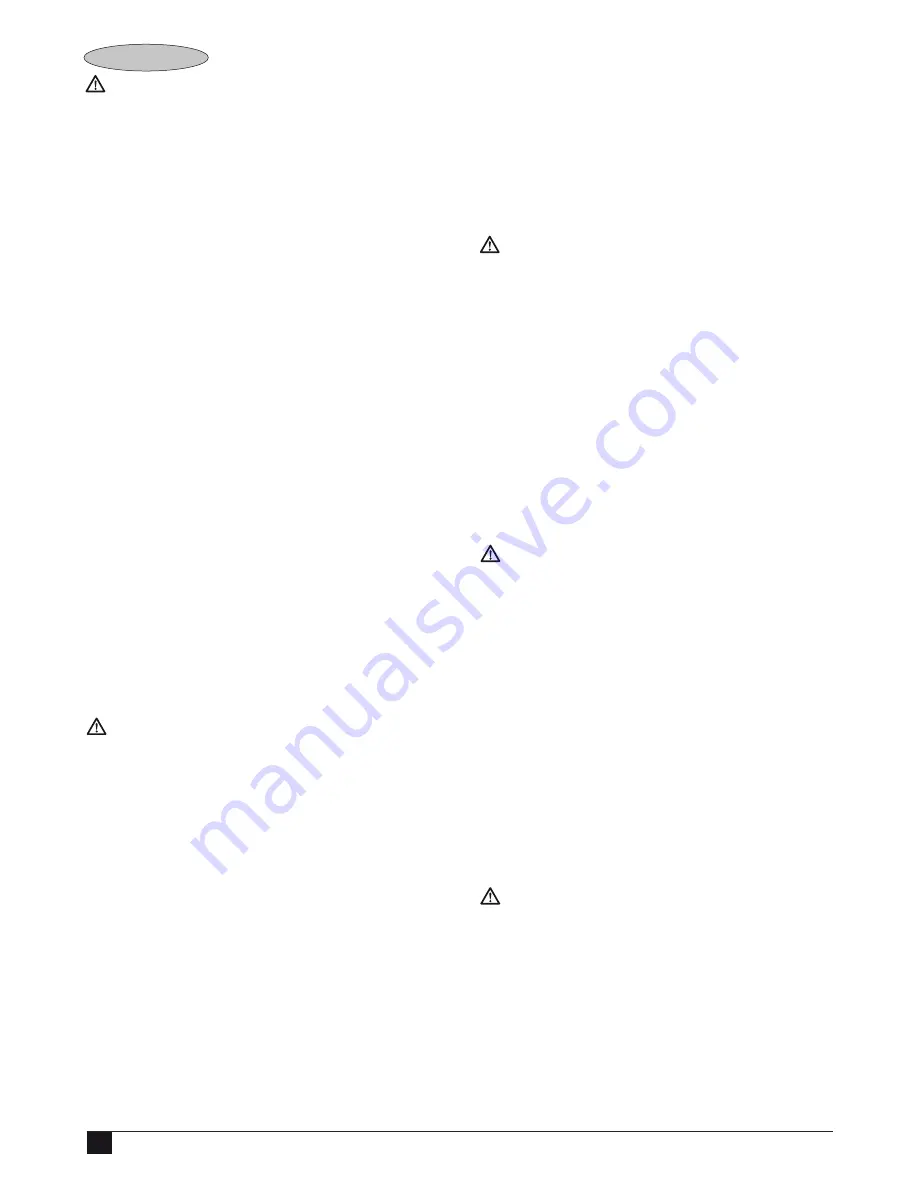
6
ENGLISH
making these cuts.
To Change Spacing between The Fence and Vise
Using the wrench provided, loosen and remove the two
fence bolts (P). Adjust the fence (E) to desired
locations.Insert both fence bolts in provided locations.
Securely tighten both fence bolts before use.
Removal and Installation of Wheels (fig. 7, 8)
CAUTION:
Turn off and unplug the tool before
making any adjustments or removing or installin
gattachments or accessories. Be sure the trigger
switch is in the OFF position.
Do not make any
adjustment while the wheel is in motion. Do not make
any adjustment while chop saw is plugged into power supply.
1. Push in spindle lock (L) and rotate wheel (J) by hand
until wheel lock lever engages slot in inside flange(R) to
lock wheel. Loosen the bolt (S) counterclockwise in the
center of the abrasive wheel with the 8mm hex wrench
(G). Bolt has right-hand thread.
2. Remove the bolt (S), washer (T), outside flange (U) and
old wheel (J).
3. Make sure flange surfaces are clean and flat. Install the
new abrasive wheel by reversing the above steps.
4. Do not overtighten bolt.
WARNING:
Check the work surface that the chop saw
rests on when replacing with a new abrasive wheel. Itis
possible that the wheel may contact ANY ITEMS OR
STRUCTURE THAT EXTENDS ABOVE work surface
(under the base) when the arm is fully lowered.
OPERATION TIPS FOR MORE ACCURATE CUTS
• Allow the wheel to do the cutting. Excessive force will
cause the wheel to glaze reducing cutting efficiency
and/or to deflect causing inaccurate cuts.
• Properly adjust fence angle.
• Make sure material is laying flat across base.
• Properly clamp material to avoid movement and
vibration.
MOTOR BRUSH INSPECTION AND REPLACEMENT
(FIG.9)
WARNING:Turn off and unplug the tool. Be sure
the trigger switch is in the OFF position.
Brushes should be regularly inspected for wear. To
inspect brushes, unscrew the two end cap screws (V)
and remove end cap (W). Remove brush cap (Y).
Brushes (X) should slide freely in brush box. If brushes
are worndown to .3" (8mm) as shown in Figure 9 they
should be replaced. To reinstall, push new brush back
into brushbox. If replacing existing brush, maintain
same orientation as when removed. Replace the brush
cap (do not overtighten). Replace end cap and two
screws. Tighten securely.
CAUTION:
When changing to a new wheel, readjust
depth stop to original position to prevent cutting
intosupporting surface.
Trigger Switch (fig. 1)
To start the tool, depress the trigger switch (N). To turn the
tool off, release the trigger switch. Keep hands and
material from wheel until it has coasted to a stop.To
prevent unauthorized use of tool, install a standard padlock
(not included) into the padlock hole (O) located inthe
trigger.
Material Clamping and Supporting
• Angles are best clamped and cut with both legs resting
against base.
• A spacer block slightly narrower than the work piece
can be used to increase wheel utilization (Fig. 2).
• Long work pieces must be supported by a block so it
will be level with top of base (Fig. 3). The cut off end
should be free to fall downward to avoid wheel
binding.
Vise Operation (fig. 4)
The vise (F) has a quick-travel feature. To release the vise
when it is clamped tightly, turn the crank (H) counter-
clockwise one or two times to remove clamping pressure.
Lift vise lever (I) up. Pull crank assembly out as far
asdesired. Vise may be pushed forward into work without
cranking. Lower vise lever (I) then tighten vise (F) onwork
by using crank (H).
Fence Operation (fig. 5, 6)
CAUTION:
Turn off and unplug the tool before
making any adjustments or removing or
installing attachments or accessories. Be sure
the trigger switch is in the OFF position.
The fence
(E) can be adjusted two ways: to change desired
cutting angle and to change spacing between the
fence and vise.
To Change the Desired Cutting Angle
Use the wrench provided to loosen (do not remove) the two
fence bolts (P). Align the desired angle indicator line with
theslot line (A) in the base (D). Securely tighten both fence
bolts before use. For more accurate square cuts,
disconnect the power supply, loosen the two fence bolts,
push arm down until wheel extends into base. Place a
square against thewheel and adjust fence against the
square. Securely tighten both fence bolts before use. When
making a miter cut, thevise (F) may not clamp securely,
depending on the thickness of the workpiece and the miter
angle. Other aids (such as spring, bar or C-clamps) will be
necessary to secure the work piece to the fence when
Summary of Contents for BDEL701
Page 1: ...www blackanddecker com English 3 BDEL701 ...
Page 8: ......