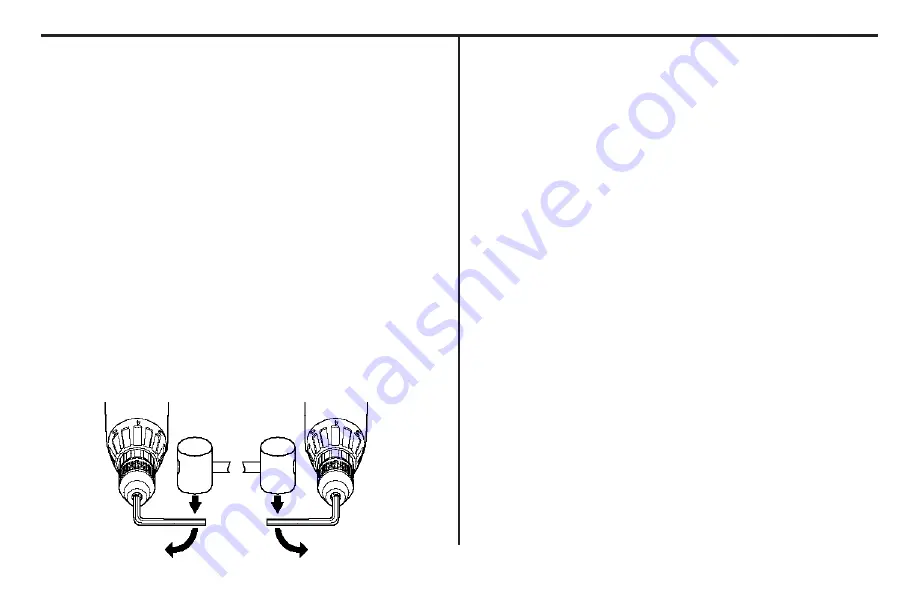
F
Fiig
gu
urre
e 8
8
F
Fiig
gu
urre
e 9
9
10
Chuck Removal
A
Allw
wa
ay
ys
s w
we
ea
arr e
ey
ye
e p
prro
otte
ec
cttiio
on
n..
Lock off the tool and turn the adjustment collar to the “drill” position and low
speed gear shifter to position 1. Tighten the chuck around the shorter end of
a hex key (not supplied) of 1/4” or greater size. Using a wooden mallet or
similar object, strike the longer end in the clockwise direction, as shown in
Figure 8. This will loosen the screw inside the chuck.
Open chuck jaws fully, insert screwdriver (or Torx tool if required) into front
of chuck between jaws to engage screw head. Remove screw by turning
clockwise (left-hand-thread). Place hex key in chuck and tighten, as shown
in Figure 9. Using a wooden mallet or similar object, strike key sharply in the
counter clockwise direction. This will loosen the chuck so that it can be
unscrewed by hand.
Chuck Installation
Lock off the tool. Screw the chuck on by hand as far as it will go. Tighten the
chuck around the shorter end of a 1/4” or larger hex key (not supplied) strike
the longer end in the clockwise direction with a wooden mallet, as shown in
Figure 8. Insert and tighten the screw by turning in a counter clockwise
direction.
Operation as a Drill
Turn the collar to the drill bit symbol. Install and tighten the desired drill bit
in the chuck. Select the desired speed/torque range using the dual range
gear shifter to match the speed and torque to the planned operation.
Follow these instructions for best results when drilling.
Drilling
1.
Use sharp drill bits only. For WOOD, use twist drill bits, spade bits,
power auger bits, or hole saws. For METAL, use high speed steel twist
drill bits or hole saws. For MASONRY, such as brick, cement, cinder
block, etc., use carbide-tipped bits.
2.
Be sure the material to be drilled is anchored or clamped firmly. If
drilling thin material, use a “back-up” block to prevent damage to the
material.
3.
Always apply pressure in a straight line with the bit. Use enough
pressure to keep the drill bit biting, but do not push hard enough to
stall the motor or deflect the bit.
4.
Hold tool firmly to control the twisting action of the drill.
5.
IIF
F D
DR
RIIL
LL
L S
ST
TA
AL
LL
LS
S
, it is usually because it is being overloaded.
R
RE
EL
LE
EA
AS
SE
E T
TR
RIIG
GG
GE
ER
R IIM
MM
ME
ED
DIIA
AT
TE
EL
LY
Y
, remove drill bit from work, and
determine cause of stalling.
D
DO
O N
NO
OT
T C
CL
LIIC
CK
K T
TR
RIIG
GG
GE
ER
R O
OF
FF
F A
AN
ND
D O
ON
N IIN
N
A
AN
N A
AT
TT
TE
EM
MP
PT
T T
TO
O S
ST
TA
AR
RT
T A
A S
ST
TA
AL
LL
LE
ED
D D
DR
RIIL
LL
L –
– T
TH
HIIS
S C
CA
AN
N D
DA
AM
MA
AG
GE
E T
TH
HE
E
D
DR
RIIL
LL
L..
6.
To minimize stalling on breaking through the material, reduce pressure
on drill and ease the bit through the last fractional part of the hole.
7.
Keep the motor running when pulling the bit back out of a drilled hole.
This will help prevent jamming.
8.
With variable speed drills there is no need to center punch the point to
be drilled. Use a slow speed to start the hole and accelerate by
squeezing the trigger harder when the hole is deep enough to drill
without the bit skipping out. Operate at full on after starting the bit.