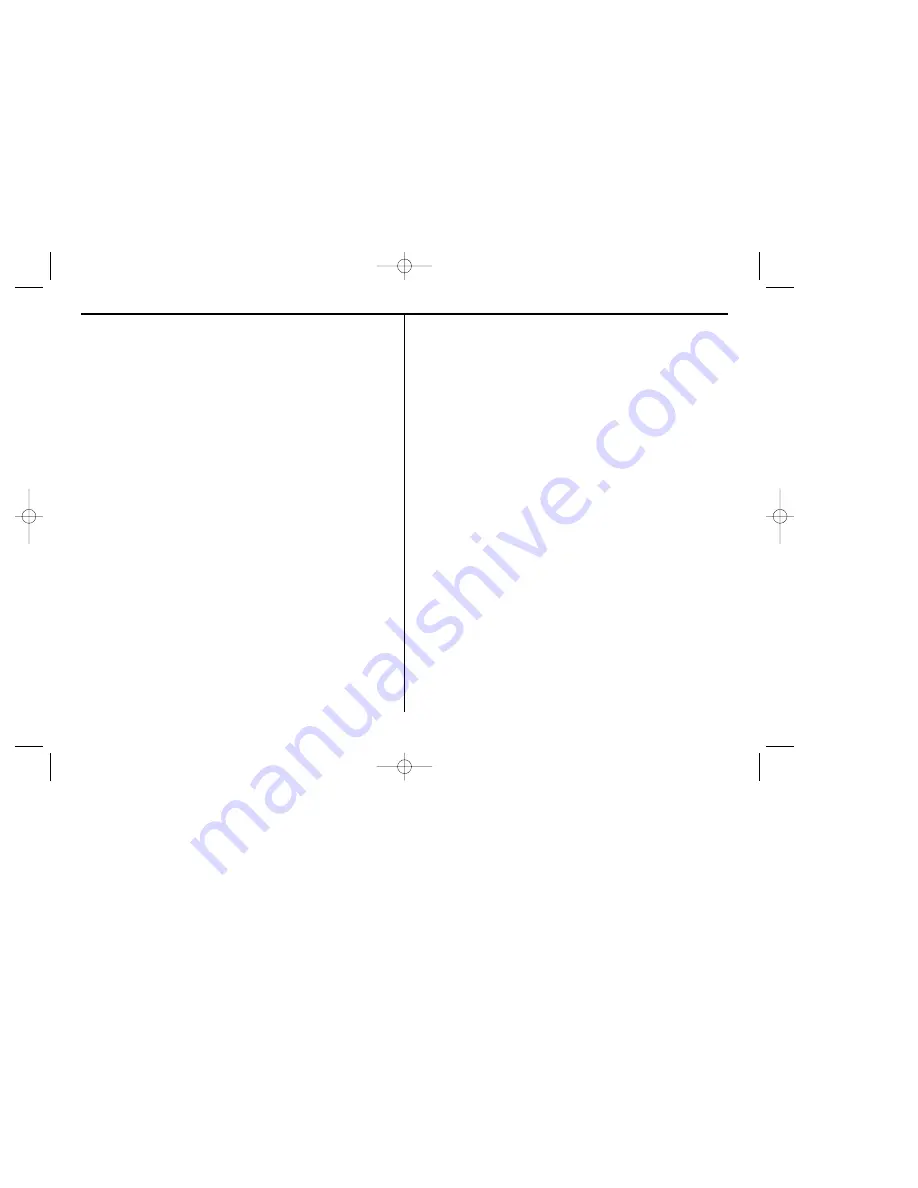
6
Lubrication
All ball bearings and needle roller bearings are factory lubricated for the life of
the bearings. Needle roller bearings receive additional lubrication from the
grease in the gear case. Gearing and gear case should be relubricated every 6
months or when gear case is removed for servicing as follows: (more often if
the tool is used constantly on production jobs.)
1. Remove 3 gear case screws from front and disassemble gear case.
2. Clean out old grease and thoroughly clean all parts.
3. Relubricate gear box and gearing with the quantity of B&D heavy duty
grease as called for on parts bulletin.
4. Reassemble.
Clutches should be lubricated at same time the gearing is lubricated
as follows:
1. Remove clutch housing by unscrewing (left hand thread).
2. On drywall, depth sensitive units slip clutch assembly from clutch housing.
3. Lightly brush or coat areas marked A, B, with B&D clutch grease (69251).
Coat clutch face inside nose of gear case (Figure 9).
4. On positive and versa clutch units, the clutch assembly will not slip out of
clutch housing. It is necessary only to coat the clutch faces on these units.
5. Reassemble clutch housing.
IMPORTANT!
To assure product safety and reliability, particularly for double insulated tools,
repairs, maintenance and adjustment (excluding maintenance described in this
manual) should be performed by B&D service centers or authorized service
centers, using identical B&D replacement parts.
Accessories
Recommended accessories for use with your tool are available at extra cost
from your distributor or local service center. A complete listing of service cen-
ters is included with your tool.
CAUTION: The use of any non-recommended accessory may be hazardous.
If you need any assistance in locating any accessory call 1-800-9-BD TOOL:
(1-800-923-8665) or contact Black & Decker (U.S.) Inc., Consumer Services
Department, 626 Hanover Pike, P.O. Box 618, Hampstead, MD 21074.
154567/2037-220 5/17/02 1:34 PM Page 6