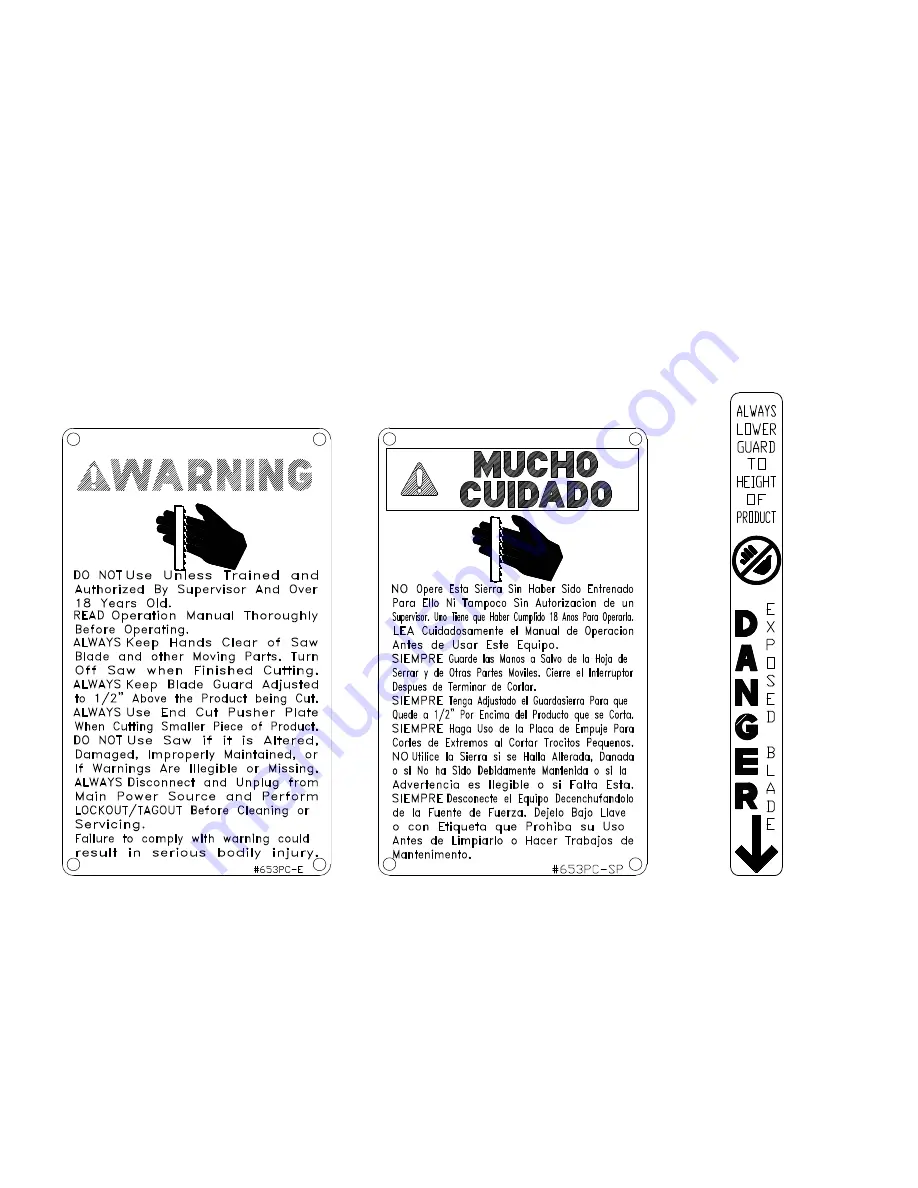
WARNING LABELS
FOR BIRO POWER SAWS
SEE PAGE 34 AND 35 FOR LOCATIONS ON MACHINE
Item No. 653PC-E
Item No. 653PC-SP
5
12. Make sure saw guide bar with saw guard is in its lowest position. Close head and base doors.
13. Push start button and check for proper phasing of motor. Blade should be traveling down through the guide.
14. Watch for proper tracking of blade. Back of blade should be centered in hole in saw guide (Part No. S119A)
in stationary bar. Push stop button to stop machine.
15. Check placement of all warning labels, wall chart and Manual. Machine is ready for trained operators to
process product.
16. Contact your local Distributor or BIRO directly if you have any questions or problems with the installation
or operation of this machine.
Item No.
708
Summary of Contents for 3334SS-4003FH-TL
Page 2: ......
Page 12: ...9 OPERATOR S NOTES ...
Page 24: ...21 COMMON TRUE LEFT PARTS ...
Page 25: ...22 COMMON TRUE LEFT PARTS ...
Page 32: ...29 ...
Page 33: ...30 ...