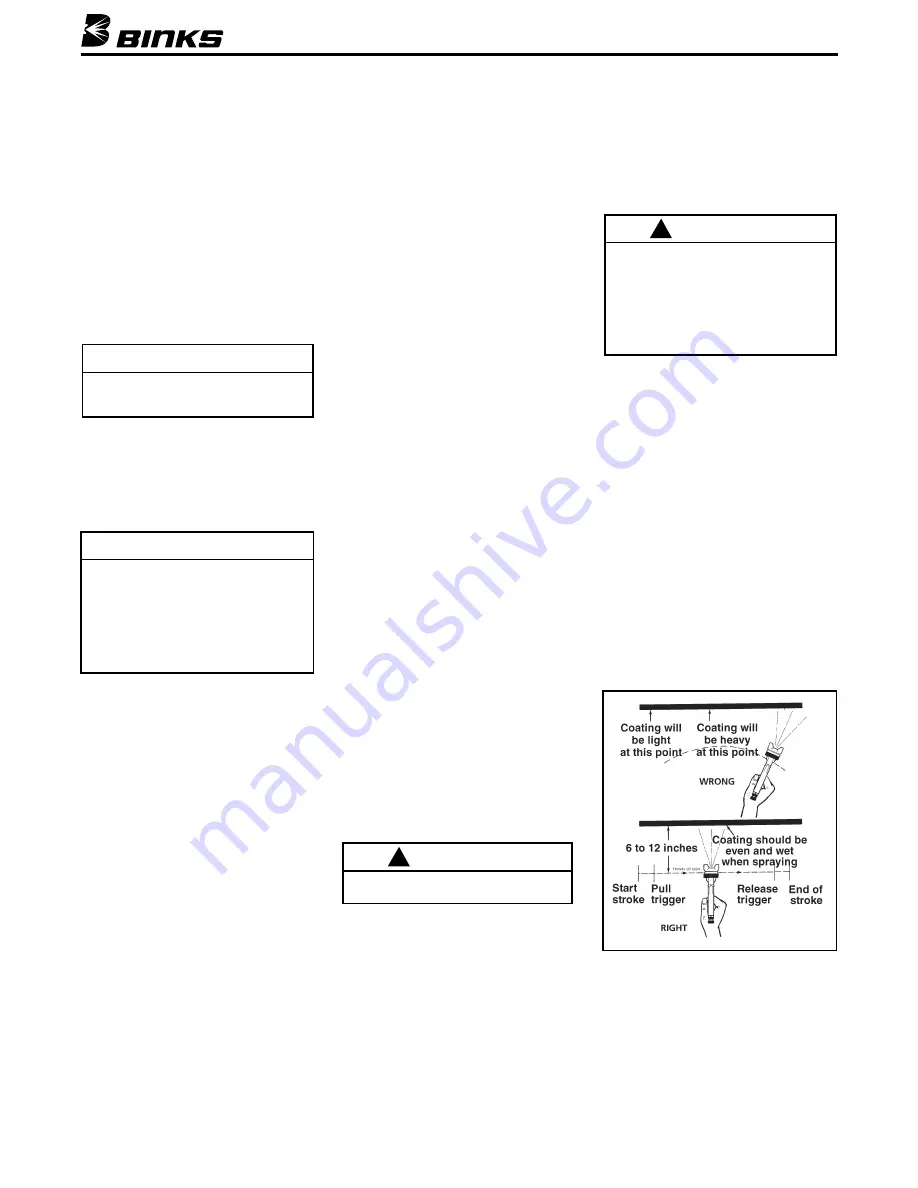
SPRAY TECHNIQUE
The first requirement for a good resultant
finish is the proper handling of the gun.
The gun should be held perpendicular
to the surface being covered and moved
parallel with it. The stroke should be
started before the trigger is pulled and the
trigger should be released before the
stroke is ended. This gives accurate
control of the gun and fluid.
The distance between gun and surface
should be 6 to 12 inches depending on
fluid and atomizing pressure. The fluid
deposited should always be even and wet.
Lap each stroke over the preceding stroke
to obtain a uniform finish.
GENERAL SPRAY INSTRUCTIONS
To reduce overspray and obtain maximum
efficiency, always spray with the lowest
possible fluid/air pressure that produces
an acceptable spray pattern.
For best results, use 3 to 6 psi fluid pres-
sure. Higher than 6 psi fluid pressure may
be required for heavy-bodied materials.
Low fluid pressures will produce a nar-
rower than normal spray pattern.
Generally use 30-35 psi air at gun inlet
(see page 6). Unusually heavy, difficult to
atomize fluids may require up to 50 psi
air at gun inlet.
CONTROLLING THE FAN SPRAY
The fan spray is controlled by means of
the side port control assembly (7).
Turning this control clockwise until it is
closed will give a round spray; turning it
counterclockwise will widen the spray
into a fan shape. The fan spray can be
turned anywhere through 360 ° by posi-
tioning the air nozzle (2) relative to the
gun. To accomplish this, loosen retaining
ring (1), position nozzle (2), then tighten
retaining ring (1).
CONTROLLING THE FLUID FLOW
When used with a pressure assisted cup,
an increase in air pressure will increase
the rate of flow. When fed from a pres-
sure supply, an increase in the fluid pres-
sure will increase the rate of flow. Correct
fluid nozzle size should be selected for
correct fluid flow rate. The fluid control
knob (19) may be used to restrict the (3)
fluid nozzle opening and reduce the fluid
flow as necessary.
AIR NOZZLE, FLUID NOZZLE,
NEEDLE ASSEMBLY
1. All nozzles and needles are precision
made. They should be handled with
care.
2. Except as described in “ADJUSTING
THE NEEDLE ASSEMBLY”, do not
make any alterations in the gun. To do
so could cause finishing difficulties.
3. To clean nozzles, soak them in solvent
to dissolve any dried material, then
blow them clean with air.
4. Do not probe any of the holes in the
nozzles with metal instruments. If
probing is necessary, use only a tool
that is softer than brass.
ADJUSTING THE NEEDLE
ASSEMBLY (16)
1. Remove the fluid control knob (19)
and the blue spring (14).
2. Pull the needle assembly out approxi-
matley 1-1/4 inches.
3. Loosen the needle cap (18).
4. Screw the needle assembly locknut
(17) out for more trigger movement,
in for less trigger movement.
5. Adjust the needle assembly so that
when the trigger (23) moves, the spin-
dle assembly (13) moves 1/16 to 3/32
of an inch before the needle assembly
moves.
6. Tighten the needle cap.
TROUBLESHOOTING
Faulty Spray
A faulty spray pattern is often caused by
improper cleaning resulting in dried mate-
rials around the fluid nozzle tip or in the
air nozzle. Soak these parts in thinners to
soften the dried material and remove with
a brush or cloth.
Intermittent Spray
If the spray flutters, it is caused by one
of the following faults:
1. Insufficient fluids available. Check
supply and replenish if necessary.
2. Pressure vent tube from gun body
to pressure assist cup is loose or
leaking.
3. Check valve in pressure assist cup
is stuck or blocked.
4. Pressure assist cup cover not suffi-
ciently tight or cover gasket defective.
5. Insufficient fluid pressure from stan-
dard pressure pots.
7
OPERATING THE MACH 1SL
HVLP SPRAY GUN
CAUTION
NEVER USE METAL INSTRUMENTS TO
CLEAN THE AIR OR FLUID NOZZLES. THESE
PARTS ARE CAREFULLY MACHINED AND
ANY DAMAGE TO THEM WILL CAUSE
FAULTY SPRAY. If either the air nozzle (2)
or fluid nozzle (3) are damaged, these
parts must be replaced before perfect
spray can be obtained.
!
NOTE
To reduce overspray and obtain maximum
efficiency always spray with the lowest
possible atomizing air pressure.
NOTE
Excessive atomizing air pressures can
increase overspray, reduce transfer
efficiency, and with some materials,
result in poor finish quality from dry
spray. Atomizing air pressures should
not exceed 10 psi. See table on page 6,
diagram on page 2 and regulatory note
on page 8.
CAUTION
Overtightening may damage the threads
and make future adjustments difficult.
!