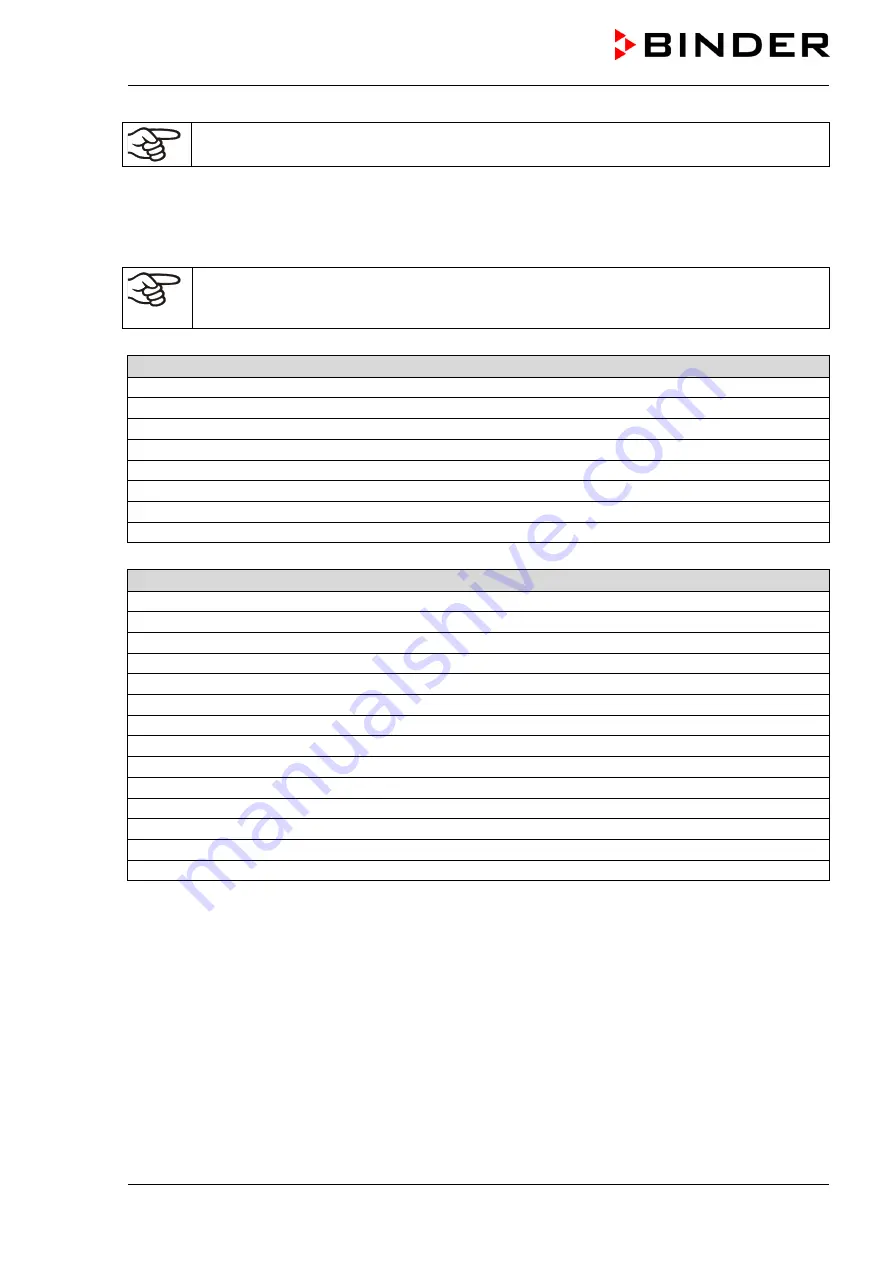
MK (E2.1) 10/2014
page 64/73
If the cabinet is fully loaded, the specified heating up and cooling down times may vary accord-
ing to the load.
18.5 Equipment and options MK 53
To operate the alternating climate chamber MK, use only original BINDER accessories or ac-
cessories / components from third-party suppliers authorized by BINDER. The user is respon-
sible for any risk arising from using unauthorized accessories.
Regular equipment
Microprocessor display program controller
Communication interface RS 422
Fan speed controller
Programmable bedew protection of charging material
Door with window and interior lighting
Access ports with silicone plug, 80 mm on top
1 rack, stainless steel
Temperature safety device class 2 acc. to DIN 12880:2007
Options / accessories
Additional rack, stainless steel
Perforated rack ,stainless steel
Securing elements for additional fastening of racks (4 pieces)
Keyboard locking
Lockable door
Access ports 80 mm right or left with silicone plug
Over-/under temperature safety device class 2
Analogue output 4-20 mA for temperature with 6 pole DIN socket, DIN plug included
Additional measuring channel for digital object temperature display with flexible Pt100 temperature sensor
BINDER Data Logger kit for temperature TH 220
Calibration of temperature including certificate
Spatial temperature measurement including certificate
Spatial temperature measurement acc. to DIN 12880 including certificate
Qualification folder