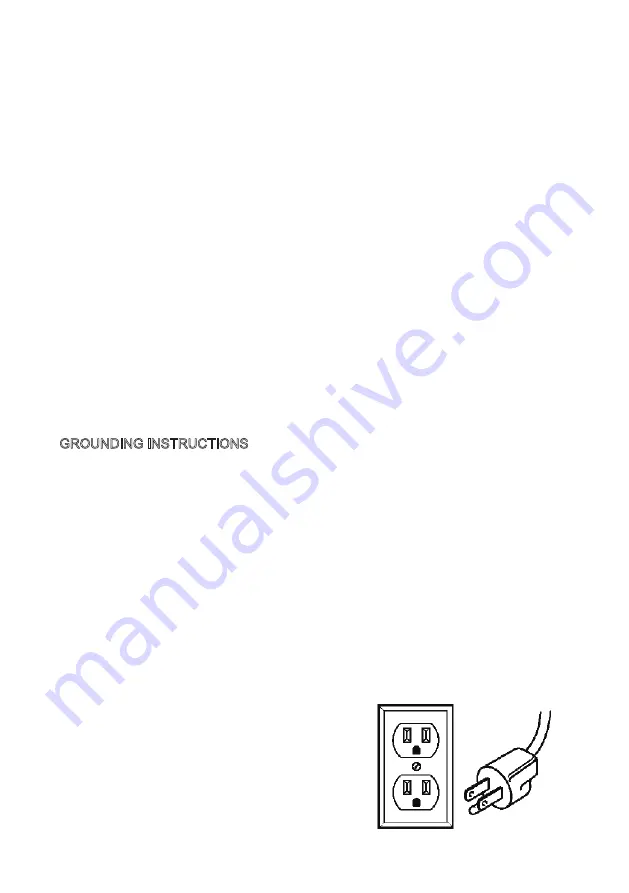
6
GROUNDING INSTRUCTIONS
IN THE EVENT OF A MALFUNCTION OR BREAKDOWN,
grounding provides the path of
least resistance for an electric current and reduces the risk of electric shock. This tool
is equipped with an electric cord that has an equipment grounding conductor and a
grounding plug. The plug MUST be plugged into a matching outlet that is properly
installed and grounded in accordance with ALL local codes and ordinances.
DO NOT MODIFY THE PLUG PROVIDED. If it will not fit the outlet, have the proper outlet
installed by a licensed electrician.
IMPROPER CONNECTION of the equipment grounding conductor can result in electric
shock. The conductor with the green insulation (with or without yellow stripes) is the
equipment grounding conductor. If repair or replacement of the electric cord or plug is
necessary, DO NOT connect the equipment grounding conductor to a live terminal.
CHECK with a licensed electrician or service personnel if you do not completely under-
stand the grounding instructions or whether the tool is properly grounded.
USE ONLY THREE-WIRE EXTENSION CORDS that
have threepronged plugs and outlets that accept
the tool’s plug as shown in Fig. 1.Repairor replace
a damaged or worn cord immediately.
CAUTION: In all cases, make certain the outlet in
question is properlygrounded. If you are not sure,
have a licensed electrician check the outlet.
17.Keep the distance between the wheel and tool rest at most a 1/8-inch (3.2 mm) space.
Adjust the work rest accordingly as the wheel grinds down to a smaller diameter with
use over time.
18.Guard against electrical shock by preventing body contact with grounded surfaces.
For example: pipes, radiators,ranges, refrigerator enclosure, etc.
19.Never reach to pick up a workpiece, a piece of scrap, or anything else that is in or near
the grinding path of the wheel.
20.Avoid awkward operations and hand positions where a sudden slip could cause your
hand to move into the wheel. Always make sure you have good balance.
21.Do not turn the switch on and off rapidly. This could cause the wheel to loosen and
create a hazard. Should this ever occur, stand clear and allow the wheel to come to
a complete stop. Disconnect your grinder from the power supply and retighten the wheel
nut securely.
22.Frequently clean grinding dust from beneath the grinder.
23.If any part of this grinder is missing, broken, bent, or damaged in any way, or if any
electrical component fails to perform properly, shut off the power switch, remove the
machine plug from the power source and have the damaged, missing, or failed parts
replaced before operation.
Electrical information