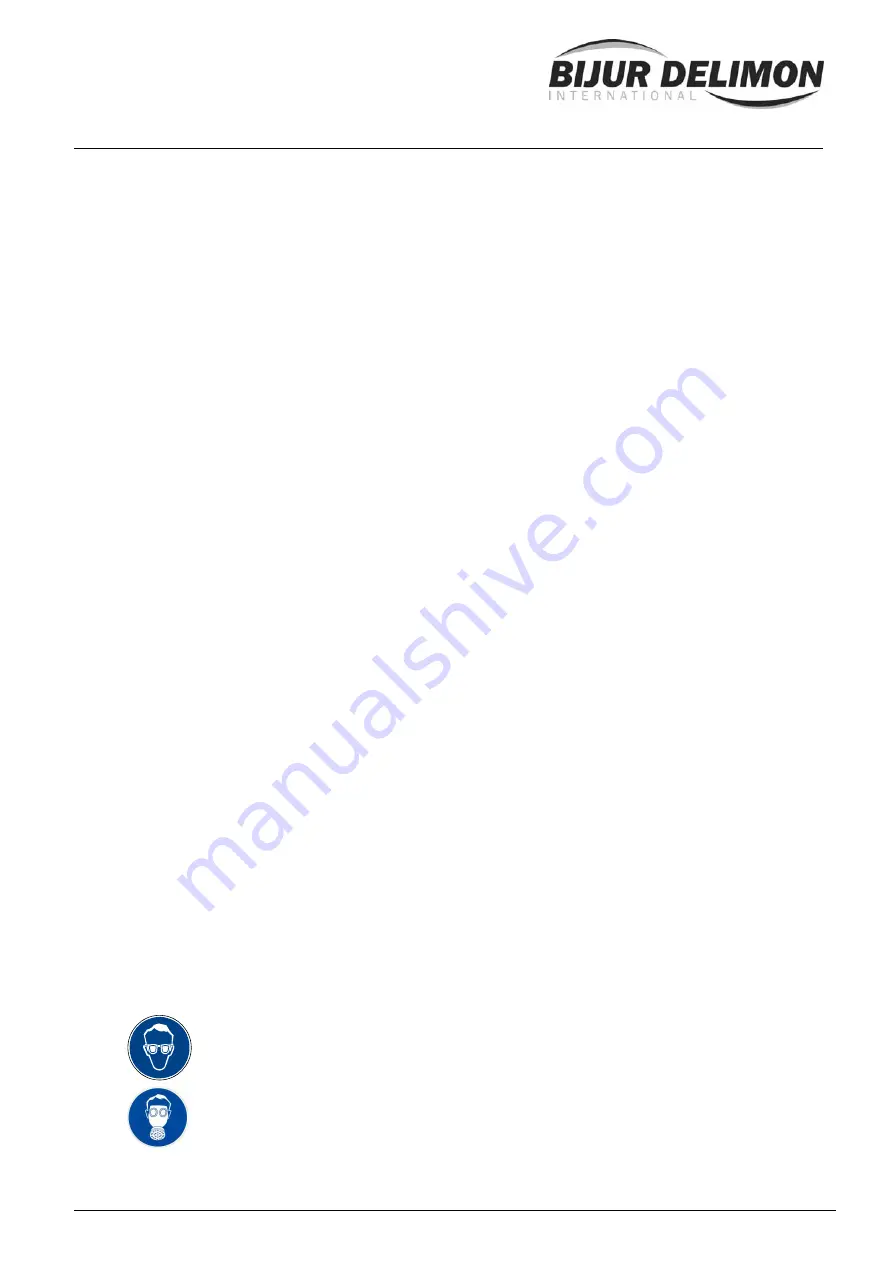
Page 3 of 11
BA_2005_1_GB_BFE
2. Safety
(continuation)
2.2
Personnel qualification and training
Personnel performing work required to install, operate, maintain or inspect this equipment must be
adequately trained and qualified. In this regard, determination of competency, understanding and
supervision levels required for individual assignment is left to the purchaser of the equipment. However,
should assistance with on-site training be desired, please contact your local DELIMON office for
assistance.
2.3
Dangers in case of nonobservance of the safety instructions
Failure to properly follow all safety instructions may result in hazard to personnel, the environment or to
machinery and equipment. Failure to follow these instructions may also additionally void warranties and
nullify claims for damages. Examples of such instances follow:
•
Failure of machinery or operating systems to function properly
•
Failure to observe proper methods of maintenance and repair
•
Unnecessary creation of hazards to personnel by means of electrical shock, mechanical injury or
exposure to potentially hazardous chemicals
•
Unnecessary creation of environmental hazards through chemical leaks
2.4 Safety
conscious
working
All Safety Instructions resulting from National, Local or User mandated regulations, as well as those
contained within this instruction, must be observed at all times.
2.5
Safety instructions for the user/operator
•
Users should always take care that only authorized and skilled personnel are allowed to perform
installation, maintenance and inspection work.
•
Installation, maintenance and inspection of lubrication systems should only be performed while
machinery and equipment being serviced is in “Shut-Down Mode”.
•
Protective covers and guards, provided to ensure that contact with moving parts is eliminated during
machine operation, (e.g. couplings, pulleys, gears, etc.), must be replaced following maintenance
and repair.
•
Use “Common Sense”! When hot or cold machine parts can lead to potential dangers, those parts
must be handled in such manner so as to avoid human touch; i.e. shielding is required.
•
Leaks from shaft seals, reservoirs, piping or fittings should be repaired so as to not cause potentially
hazardous materials from escaping to the work area. In instances where such leaks have occurred,
all local and National rules and regulations for their recovery and disposition must be followed.
•
All potential hazards resulting from exposure to electrical sources must be eliminated. Please refer to
VDE and local power company rules and regulations for guidance.
•
Before restarting system and equipment, refer to instruction in Section 7; Start-Up Procedure.
2.6
Safety instructions for maintenance, inspection and installation work
Before installing or servicing lubrication equipment and machinery, management should insure that only
persons who are fully trained, skilled and authorized to perform such work are assigned to such tasks.
Major installation or modification work should only be performed during shut-downs. It is also imperative
that shut-down procedures recommended by equipment manufacturers be followed. Pumps, lubricators
and distribution systems which deliver potentially hazardous materials to the environment must be
thoroughly cleaned. All safety devices and protective equipment, disabled or removed during cleaning,
must be immediately reinstalled and reactivated prior to machine use.
Safety Sign, per DIN 4844, Use Safety Glasses or Goggles.
Advice: Whenever working with compressed air, wear safety glasses
Safety Sign, per DIN 4844, Use Breathing Mask.
Advice: Observe EC-Safety Data Sheet for materials of consumption
and additives used and use personal protective equipment.