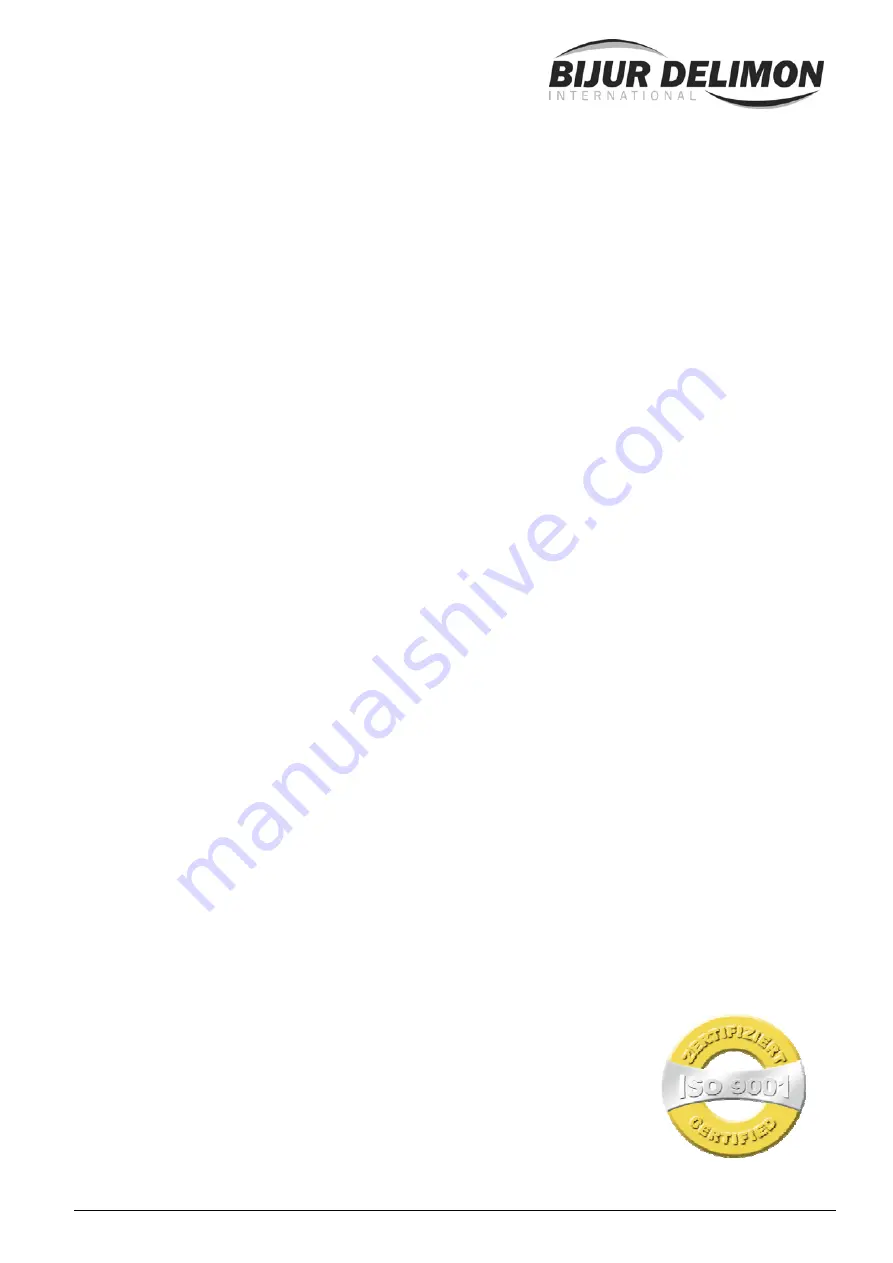
Page 1 of 11
BA_2005_1_GB_BFE
Operating
instructions
Pump BF-E
INDEX
Page
1. General ................................................................................. 2
2. Safety ............................................................................ 2 – 4
A. Pump type ............................................................................. 4
B. Number of outlets ................................................................ 4
C. Revision ................................................................................ 5
D. Kinds of drive ....................................................................... 5
E. Position of drive .................................................................. 5
F. Reservoir / drum capacity ................................................... 5
G. Accessories ......................................................................... 5
3. Design .................................................................................... 6
4. Principle of operation .......................................................... 7
5. Specifications .............................................................. 7 – 8
6. Start-up ......................................................................... 8 – 10
7. Maintenance ....................................................................... 10
8. Plates .................................................................................. 11