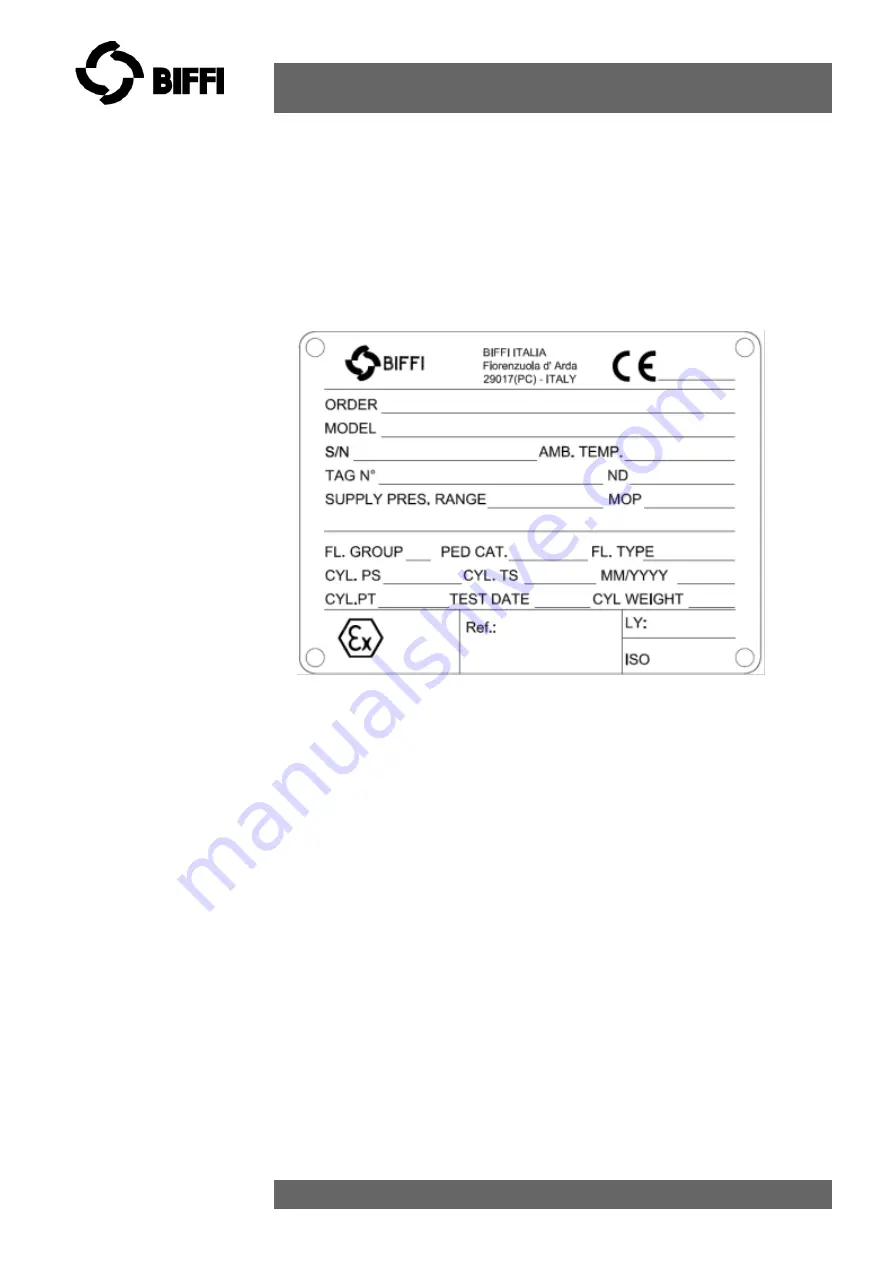
HLA
– Double acting- hydraulic linear actuator
Use and maintenance manual
© Copyright by BIFFI Italia. All right reserved.
Pag. 5
Contents may change without notice
1.2
IDENTIFICATION PLATE
It is forbidden to modify the information and the marks without
previous written authorization by BIFFI Italia S.r.l.
The plate fastened on the actuator contains the following information
(Figure1).
Figure 1
– Data plate
1.3
INTRODUCING THE ACTUATOR
HLA double acting hydraulic linear actuators, are suitable for the
operation of linear valves ( wedge gate valves, through conduit gate
valves) for ON-OFF and modulating heavy-duty service.
The actuator is made up of an hydraulic cylinder and a mounting
pedestal complete with a joint for the coupling to the valve stem of
actuator output stem. The valve is actuated in opening and in closing
position by the actuator hydraulic cylinder that is pressurized in one
or in the other direction.
The linear stroke of the valve is adjustable by means of the external
mechanical stop for upward position and by the adjustment of the
coupling of valve stem to actuator joint for the downward position.
The actuator pedestal has a flange with threaded holes to fix the
actuator to the valve.