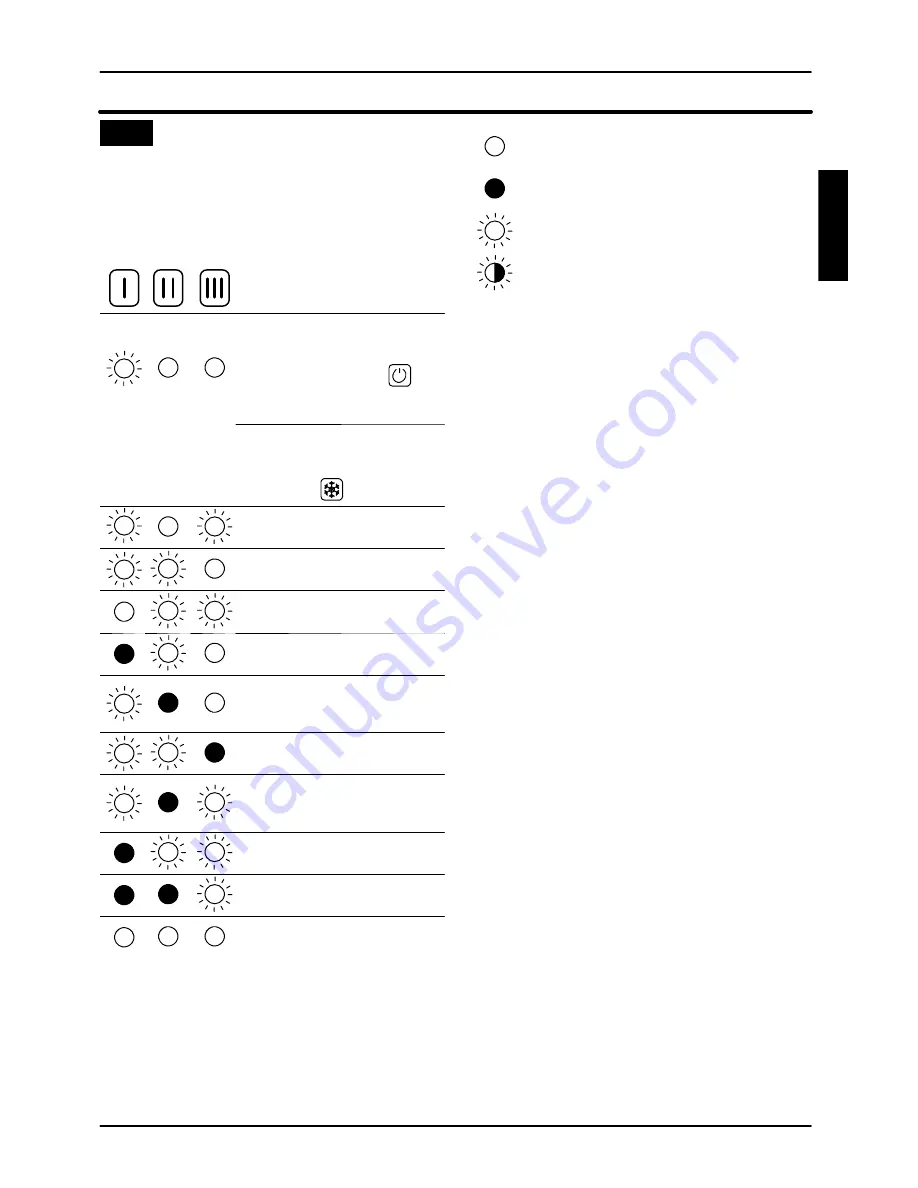
Appliance description
3
1.5
Operation lights
Three lights (9 in Fig. 1.3) give detailed indication
regarding the operation of the boiler.
The following table gives the relationship between
each of the possible light combinations and their
meaning.
A short pulse every 4
seconds:
stand---by condition
Function selector in
position.
Anti---freeze system active
1 second pulse every 2
seconds: normally
operating boiler. Function
selector in
position
C.h. operation
Frost protect operation
Faulty c.h. temperature
probe NTC
Faulty flue temperature
probe NTC
Faulty primary circuit
(no water or absence of
flow)
Faulty air pressure switch
Lack of burner ignition (no
ignition signal from the full
seqence ignition device)
Safety thermostat lock out
Flue temperature probe
NTC lock out
Lack of power supply or
fauly electr. control p.c.b.
Lamp OFF
Lamp ON
Flashing lamp, alone or simultaneously
with an other lamp.
Flashing lamp, alternate with another
lamp.
USE