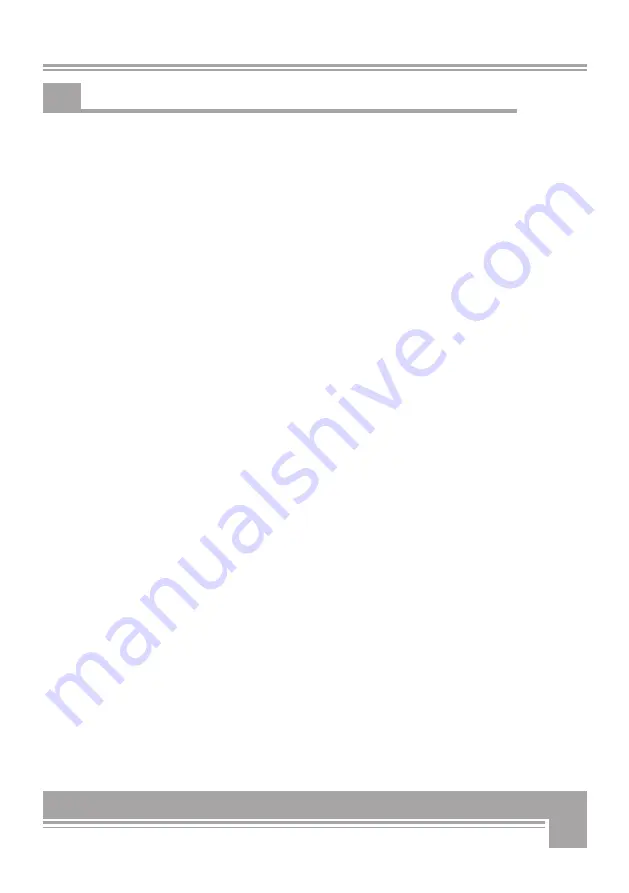
21
When the winch is fully obsolete and cannot be of any longer use, it
should be duly dismounted ahead of discarding. Certain components
need deactivation and dismantling in order to assure that no further
use is made by other parties and that no worn out parts are recycled
for other applications.
During dismantle be alert for possible recyclable materials and com-
ponents that belong to differentiated waste collection procedures ap-
plicable in your country.
The manufacturer is not liable and undertakes no responsibility for
personal injuries or damages that may result from the recycling of
worn outmachine parts and eventual re-use in other applications diffe-
rent than originally stated in this manual.
Dismantling procedure:
Take good note please: each and every dismantling task must be per-
formed by authorized service centres or trained skilled staff only!
● Pull the machine down into single components
● Lock and clamp all moving machine parts
● Deliver each single component only to authorized waste manage
ment facilities
● Drain oil and fuel out of respective tanks and lines before disposal
of the machine
● Remove rubber and plastic parts from the machine that must be se-
parately disposed of.
Deactivated, clamped moving/driving parts and components are of no
further risk and danger.
Electric components must be separately disposed to avoid substantial
environmental threat. In the event of fire on the electric deployment
system of the machine, use of an explosion-proof extinguish system is
required (for example powder fire extinguishers).
7. DISPOSING OF AN OBSOLETE WINCH
Summary of Contents for FSW 5.5 H Evolution
Page 27: ...27 14 FSW 5 5 H EXPLODED VIEW...