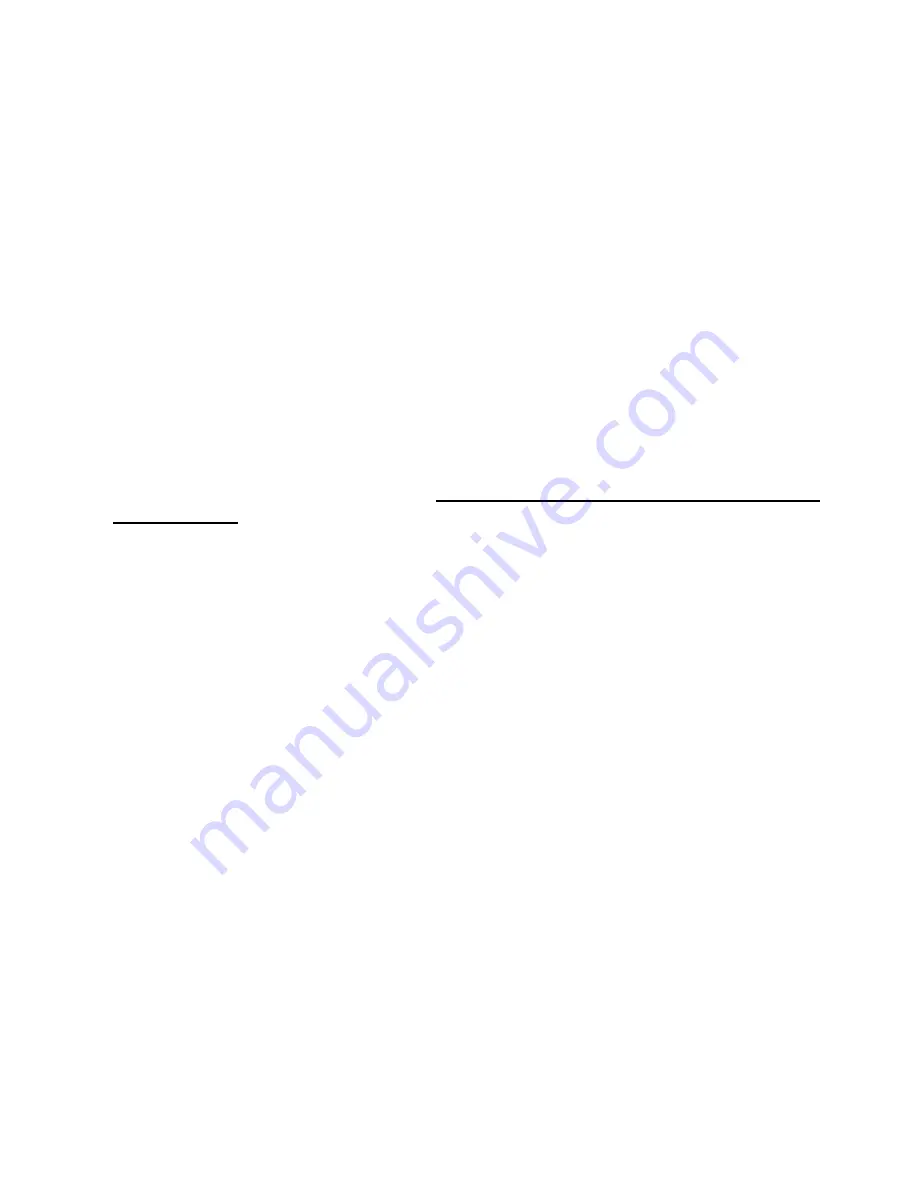
9
Heater Position Instructions
Important: Precautions and Instructions
General Instructions (Read All)
1.
The "Positioning Beam" (red dot) is an aid for proper placement of the heat sensor. The heat
Sensor reads an area of 0.8 to 1.2" diameter depending on the heater's distance from the
surface. The sensor takes an average temperature reading of the area and displays it on the
temperature controller. Note: the red dot is not at the exact center of the sensing area. As
you face the control panel the dot is
3/4"
to the left of the heat sensor.
2.
Make sure the heat sensing area is reading a painted surface. If the sensing area is positioned
incorrectly and is partially reading tape, masking, trim, plastic, rubber, a window, or a wheel
well, It will measure an average temperature much higher or lower than the actual temperature
of the painted surface. Thus, the heater will possibly overheat the area and scorch the paint, or
not heat the part enough and the paint will not be cured.
3.
The heater head distance from the product is important. If the heater head is too far away, the
product will not reach cure temperature and will run indefinitely trying to get to temperature. If the
heater head is to close "striping" may occur. The recommended distance of the heater face to the
product is 8 -12". The heater should be as parallel as possible to the product surface, which helps
maintain uniform heating over the heated area.
4.
Before heating a repair, determine if there are any types of reinforcements or extra thicknesses of
metal in the area to be cured. These areas will heat at different rates and not achieve the same
temperature as the single thickness metals without reinforcements. Aim the heat sensor on, or
near, the multiple thickness or reinforced areas so they will be fully cured.
5.
Once the cycle has started, do not move the unit. This will cause the temperature sensor to "see" a
different area, which may be cooler. If the temperature drops 18°F
,
it will reset the timer and run
another complete cycle. To help the unit's stability, be sure to lock the casters on the base of the
arm after positioning the heater to lock it in place.
6.
Check the control panel 3 to 5 minutes into the cycle. See if the temperature has risen to set point
and if the timer has started. If it hasn't, determine the problem and correct it. If there is a problem
with the position or setup of the arm where it cannot achieve the set point temperature, the timer
will not turn on. The heater will run at full intensity indefinitely.
7.
To achieve a full cure on a repair area, including overspray, the "effective cure area" of the heater
must be considered. The "effective cure area" of the rectangular shaped heater heads is an oval
shape that is just slightly smaller than the heater head. A general rule for the "effective cure area"
dimensions are 1" in from the sides and end covers of the heater head, which creates the outer
boundaries of the oval. When main and auxiliary heater heads are used together, add the two areas
together.
Heat Masking
1.
Any heat sensitive materials or surfaces (including plastic, rubber, trim, pin stripes, decals, light lenses,
Summary of Contents for AutoCure 5000
Page 1: ...January 2016 AutoCure 5000 Portable Repair Arm Assembly and Operating Manual AC5 2116 380...
Page 18: ...18 THIS PAGE INTENTIONALLY LEFT BLANK...
Page 19: ...19 Mechanical Drawings and Parts Lists Pyrometer...
Page 20: ...20 CAUTION...
Page 22: ...22...
Page 24: ...24...
Page 26: ...26 Heater Head Assembly ACH5 2116...
Page 40: ...40 SECTION J J SCALE 1 8 K DETAIL K SCALE 1 4 88 53 89 64 63 83 86 16 17...