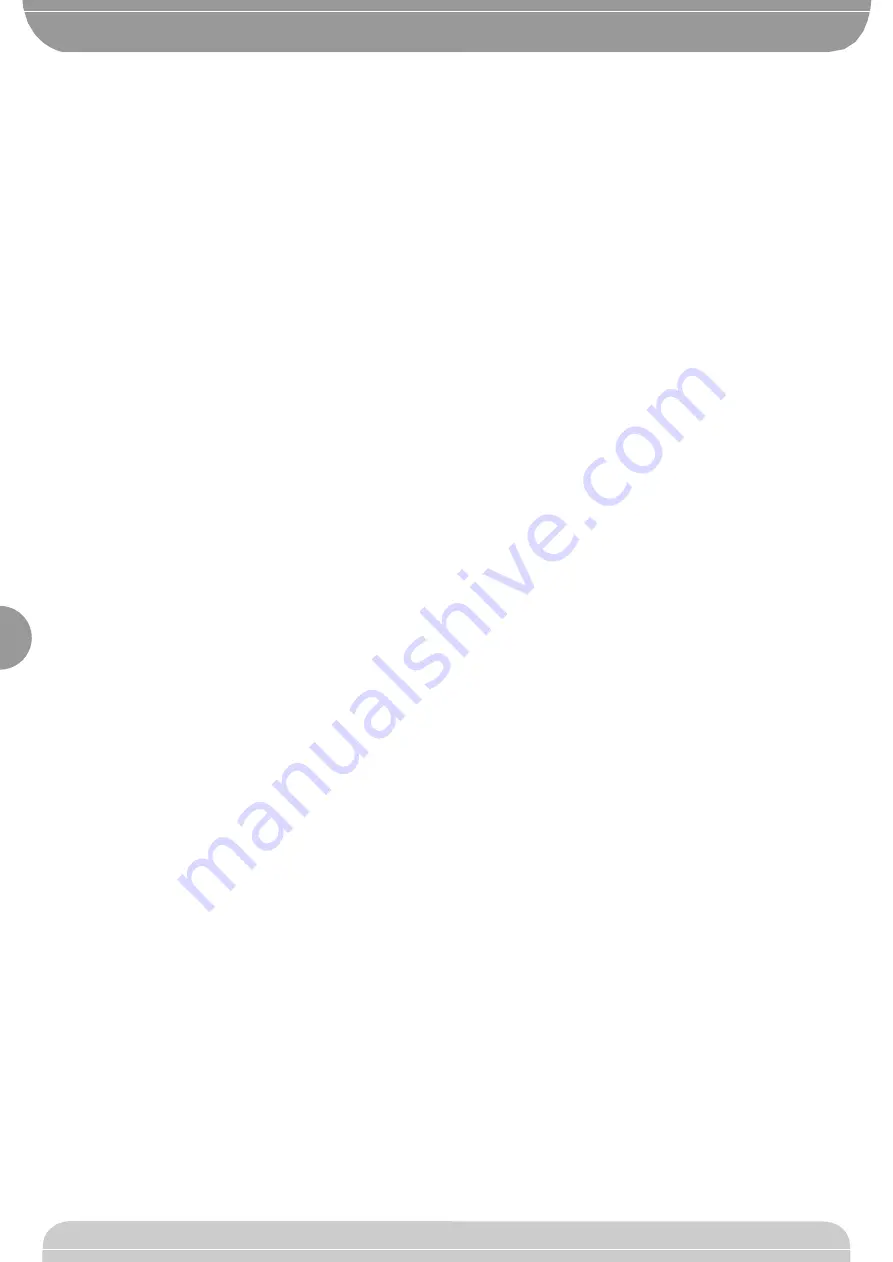
320
FR95
FR95
AUTOMATION FOR INDUSTRIAL SECTIONAL DOORS
AUTOMATION FOR INDUSTRIAL SECTIONAL DOORS
D811170_03
We declare that this product is in conformity with the following European
Directives:
89/336/EEC (amended by RL 91/263/CEE, 92/31/CEE and
93/68/EEC),73/23/CEE (amended by RL 93/68/CEE).
1) GENERAL OUTLINE
This controller has been designed to motorize residential and industrial sec-
tional doors.
The compactness and versatility of the installation allow the motor drive to be
fitted in a variety of ways.
The controller is available in the following versions:
FR95-C
Version with possibility of manual chain-opening and
closing.
FR95-CM
Version with possibility of manual chain-opening and
closing and release mechanism for maintenance (the
release mechanism disengages the drive from the
cable winder shaft of the door).
FR95-SB
Version with quick release for fast manual opening and
closing. The door should be perfectly balanced.
Safety microswitches protect each manual manoeuvre command.
The motor is supplied with an electro-mechanical brake to make the gear-
motor irreversible.
2) TECHNICAL SPECIFICATIONS
VOLTAGE
Single-phase 230V ±5% 50Hz
Three-phase 400V ±5% 50Hz
ABSORPTION
Single-phase 1.7 A
Three-phase 0.8 A
POWER
Single-phase 0.25 Kw (Hp = 0.33)
Three-phase 0.33 Kw (Hp = 0.45)
MOTOR
1400 RPM (revs./min)
CAPACITOR
12.5 µF+16 µF (starting)
BRAKE
Mechanical
INSULATION CLASS
F
THERMAL PROTECTION
130°C self-resetting
REDUCTION GEAR
OIL AGIP ALER 68
REDUCTION GEAR RATIO
1/43
OUTPUT REVS.
33 RPM
THROUGH-SHAFT
1” (Ø. 25.4 mm)
SPEED
8m/min with Z=18 1/2” x 5/16” (fig.4)
MAX DOOR WEIGHT
Single-phase 350 daN (Kg)=25 m
2
Three-phase 700 daN (Kg)= 40 m
2
TORQUE PROVIDED
Single-phase 5 daN (Kgm)
Three-phase 6 daN (Kgm)
IMPACT REACTION
Stop and reverse (with pressure
sensitive edge)
DRIVE
Link chain or direct drive
LIMITING DEVICES
Built-in limit switches
CONTROL UNIT
Mizar (single-phase)
Sirio TN1 (single-three-phase)
MANUAL MANOEUVRE
With chain for FR-C/CM
Rapid for FR95-SB (FR95-CM)
NUMBER OF MANOEUVRES
100 Manoeuvres/24h
WORKING TEMPERATURE
-15 + 60° C
PROTECTION
IP 55
CONTROLLER WEIGHT
9 Kg
DIMENSIONS
See fig. 1
3) INSTALLATION OF AUTOMATION
Preliminary checks
Check the balancing of the door.
Check that the door slides along the whole of its stroke.
Check the safety devices (parachute-type, cables etc.).
If a new door is not being installed, check whether the door and its compo-
nents are worn.
Repair or replace any worn or damaged parts.
Automation reliability and safety are directly influenced by the condition of the
sectional door’s structure.
4) CONTROLLER INSTALLATION
WARNING:
Before fastening the controller, check whether the protection
wedge “P” (fig. 10) is present in the adjustment limit switch unit. The protec-
tion wedge prevents damage to the limit switch unit when manual opening
checks are made before adjusting the limiting microswitches.
The controller can be installed on both the right or left of the sectional door.
Direct drive
The cable winder shaft of the sectional door (Ø = 1” Ø 25.4 mm) should have
a key way and can be inserted directly into the through shaft of the controller.
The controller is directly fastened to the cable winder shaft support (fig. 2) or
to the wall using special brackets. Some manufacturers of sectional doors
supply joints with shaft for these types of motor drives.
This type of installation is suitable for sectional doors with cable winders,
which have a diameter not exceeding 80 mm in order to comply with the max-
imum speed of movement required by current standards (e.g.: in Italy the
maximum speed for UNI8612 standards is 8m/min).
Drive with reduction ratio.
The cable winder shaft is driven by a chain drive which may have reduc-
tion gears.
The gearmotor is fastened to the wall by means of the bracket provided
(fig. 3).
The drive dimensions should be in accordance with the diameter of the cable
winder for lifting the sectional door.
The vertical movement speed must correspond to the speed required by cur-
rent standards (e.g.: in Italy the maximum speed for UNI8612 standards is
8m/min).
E.g.: If the sectional door is fitted with a 140mm diameter cable winder, to
obtain an upstroke speed of approx. 8m/min, a crown wheel must be fitted
which has a pitch diameter
Øp= 140mm corresponding to a 36-tooth crown wheel for a 1/2" x 5/16" link
chain.
For this type of installation, a shaft with an 18-tooth pinion for a simple 1/2"
x 5/16" chain (fig. 4) can be supplied as an accessory.
The chain tension is adjusted by moving the motor along the grooves in the
anchoring bracket (fig. 5).
CAUTION:
The chain drive should be protected in compliance with current
standards.
5) ELECTRICAL INSTALLATION SET-UP
Arrange the raceways for the connections as shown in fig. 6. Keep the power
supply connections separate from the limit switches connections.
Fit an omnipolar circuit breaker, with a contact opening of at least 3 mm,
which has protection against overloading and can be used to disconnect the
automation from the mains.
The Sirio-FR and Mizar-FR control panels are equipped with lockable cut-out
switches and fuses (fig. 7). A radio control single-twin channel receiver can be
inserted on the control boards.
Connection without the control unit can only be carried out in the single-
phase version and for “hold-to-run” control. Only use buttons with at least
10A-250V capacity (fig. 8).
6) CONNECTION TO TERMINAL BOARD
Fig. 8 shows the connection of the single-phase and three-phase gearmotor
to the terminal board.
For the electrical connection to the control unit, reference should be made to
the manual of the control unit.
7) LIMIT SWITCH ADJUSTMENT
(fig. 9)
The limit switch unit is situated on the head of the drive and is the system of
adjustment. To gain access to the adjustment unit, dismantle the pinion-type
quick release system, if any, and the box which covers the unit.
The microswitches are activated by two toothed cams which are locked in
position by a holding spring.
When the door is closed, the “door closed” adjustment cam should activate
the closing limit switch.
When the door is open, the “opening” adjustment cam should activate the
opening limit switch.
Fig. 9 shows the position of the closing and opening limit switches in relation
to the type of installation carried out.
If the adjustment cams are rotated towards each other, the stroke is
increased. If the adjustment cams are rotated away from each other, the
stroke is decreased.
The limit switch unit is equipped with a protection wedge “P” (fig.10) to pre-
vent damage to the limit switches during manual installation manoeuvres.
8) LIMIT SWITCH CAM ADJUSTMENT
WARNING:
For safety reasons, microswitch adjustment must be carried out
with the power supply off.
The adjustment unit is fitted with four microswitches: 2 act as limiting devices
and 2 act as safety overstroke devices.
The overstroke microswitches, if intercepted by the cams, bring the system