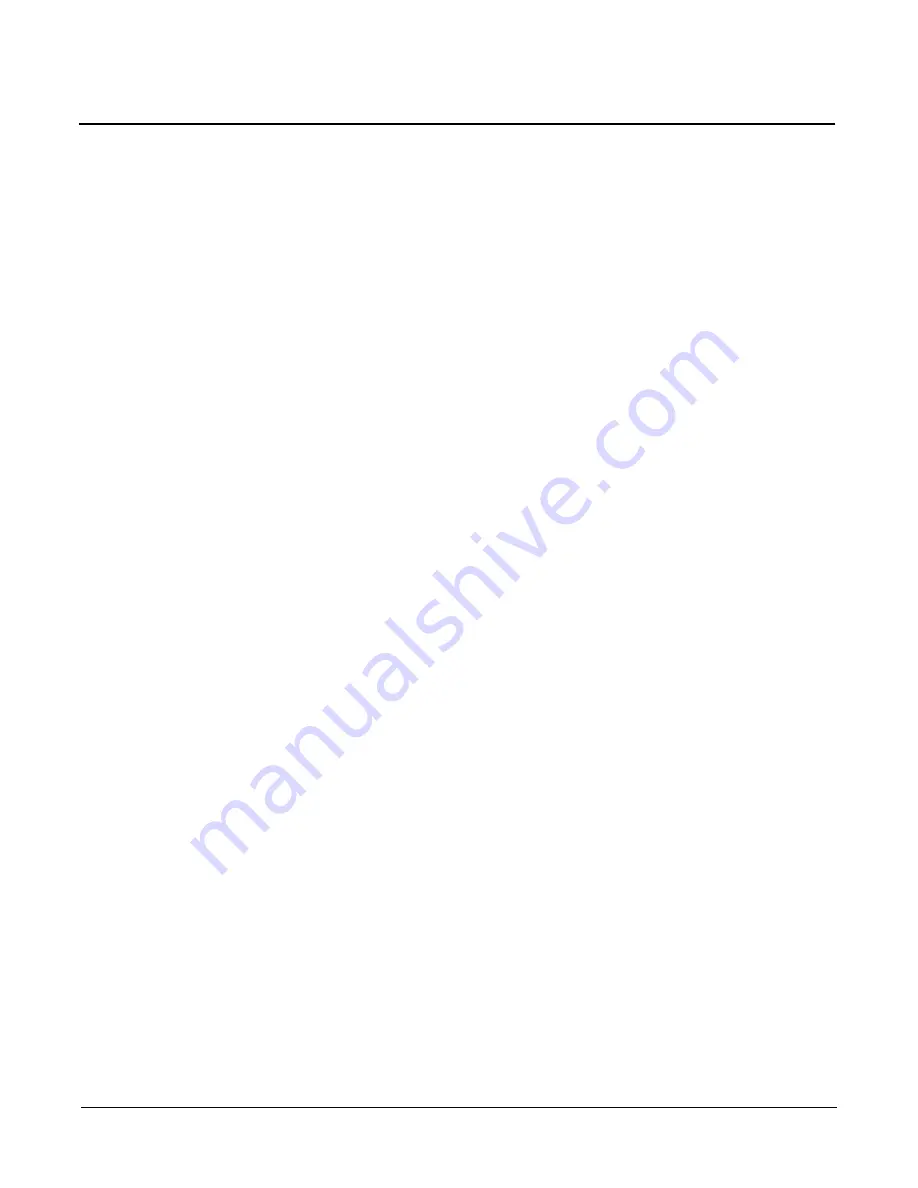
TorqPlus EM-Series Actuator
Installation and Operating Instructions
4
Remove power and rotate the proper cam to the position which toggles the limit switch.
Tighten the set screw on the cam.
Operate the actuator to verify proper cam setting.
Once adjustments are satisfactory, replace cover per section 9.0.
11.0
Troubleshooting
The following instructions are offered as a guide to the most common difficulties encountered during installa-
tion and startup.
The actuator is receiving power but the motor does not respond.
Verify the line voltage into the actuator via the field connections and insure that it matches the rating on the
nameplate of the actuator.
Check internal actuator wiring against the wiring diagram supplied with the actuator.
Check the limit switch cams to insure that they are properly set and depressing the appropriate limit
switches.
On 800 series only, verify the torque switches are not tripped.
Perform a visual inspection to verify no shipping or handling damage has occurred.
Verify no corrosion has contaminated any of the electrical or mechanical devices on the actuator.
Problem: Actuator is receiving power but does not operate. Motor hums and is warm to the touch.
Verify the line voltage into the actuator via the field connections and insure that it matches the rating on the
nameplate of the actuator.
Check torque requirement of driven device to insure that it is less than that shown on the actuator’s name-
plate.
Note: In some cases, we have noted that the actual torque needed to operate an end device has
been over two times that published by the manufacturer. It may be necessary to perform an actual torque
test during worst case conditions.
Verify coupler/bracket is properly installed and is not causing any binding.
Verify both the CCW and CW field connections are not receiving power at the same time.
Verify the limit cams are set properly and not allowing the actuator to travel outside its quadrant or against
stops.
Verify, if installed, that the electronic brake is operating properly and is not locking up the motor rotor.
Verify no corrosion has contaminated any of the electrical or mechanical devices on the actuator. Any sign
of corrosion potentially reduces the capability of the actuator.
Problem: Actuator runs erratically/sporadically.
Check ambient temperature. Standard actuators have a maximum ambient operating temperature rating
of 140 °F. Any temperatures above this rating may cause the actuator to fail.
Verify that the published duty cycle has not been exceeded.
Verify that the actuator is not wired in parallel to other actuators. All actuators must have their own isolated
control switch.
Inspect the manual override and disengagement mechanism.
Gear train may be damaged due to overtorque.
Verify proper signals are being supplied to the actuator.
Note: All AC voltage Bettis TorqPlus EM series actuators are standard with built in thermal overload motor
protectors. Should any of the above cause the protector to open, it will automatically reset when the motor
temperature is lowered to a safe level. Please consult the Bettis authorized Valve Automation Center or Bettis
Electric Division, Mansfield, Ohio.
12.0 Spare Parts and Product Information
Each Bettis TorqPlus actuator is manufactured complete with a nameplate containing important and detailed
information. This information will be needed anytime parts or additional data is requested. Please keep a file
on with all nameplate information for reference when calling the factory.