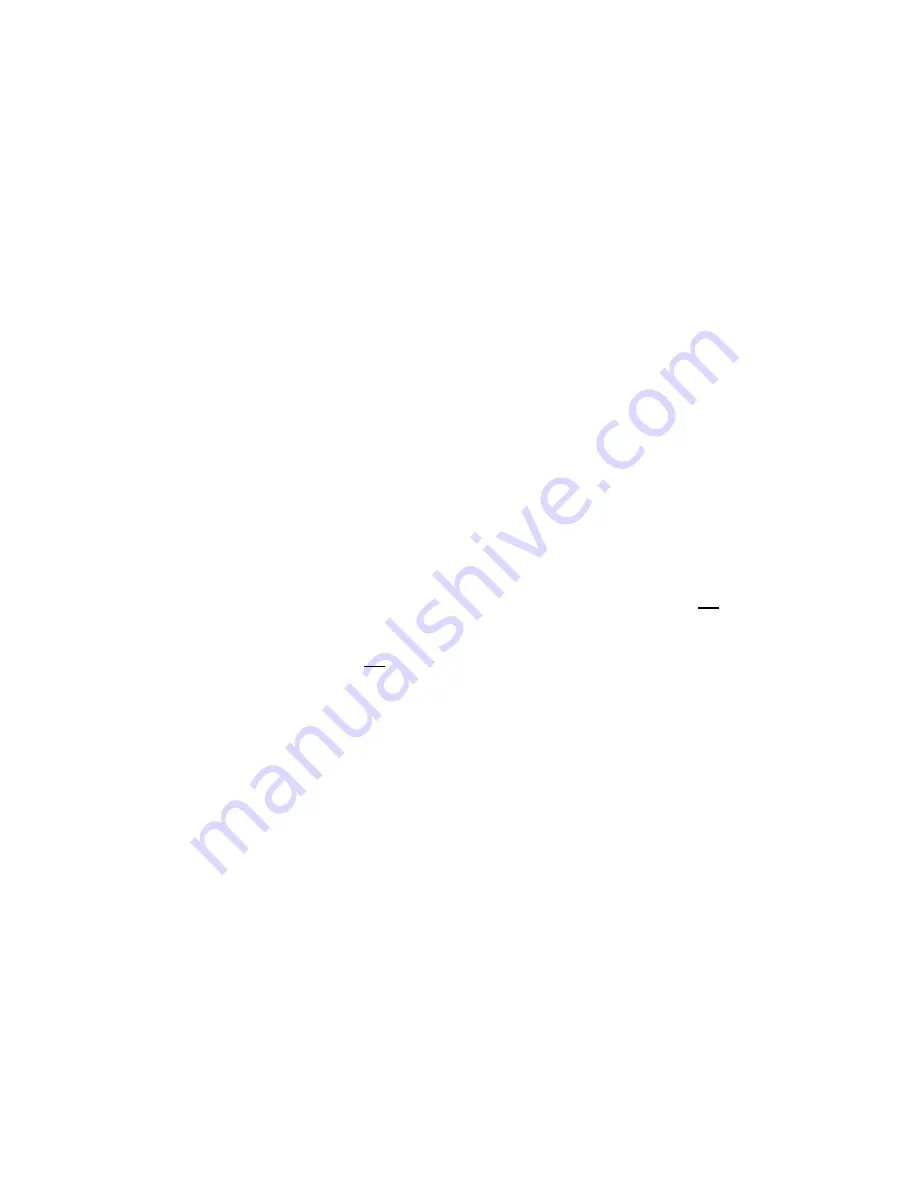
14
General Machine Cleaning
The feed wheel pushes tape through the machine. Obstructions such as dirt or dried adhesive can divert
the tape and cause it to jam. Periodical cleaning of the tape path will mitigate tape jams.
Procedure
1. Remove the upper tape plate that sets on the tape next to the feed wheel. Pull tape off from the
lower tape plate if it hasn’t already been removed. Clean any dirt and adhesive from the upper
and lower tape plates.
2. Lift the heater up and clean the bottom of it. Under the heater is a lower plate that the tape rides
over. The lower plate and heater plate are separated by a small gap that helps the tape to move
under the heater and onto the brushes with minimal obstruction. Pull down on the front of the
lower plate to separate it from the heater plate. Clean between the plates the snap the lower plate
back onto the heater plate. Be careful not to bend the lower plate. A bent plate can be a cause of
tape jams.
LUBRICATION – Not Needed!
1.
All vital moving parts of this machine have oil retaining porous bushings and should not require
additional oil for the average life of the machine.
2.
FEED WHEEL SHAFT
-
Do not oil this shaft. Oil can creep in through the bearings and effect
internal parts.