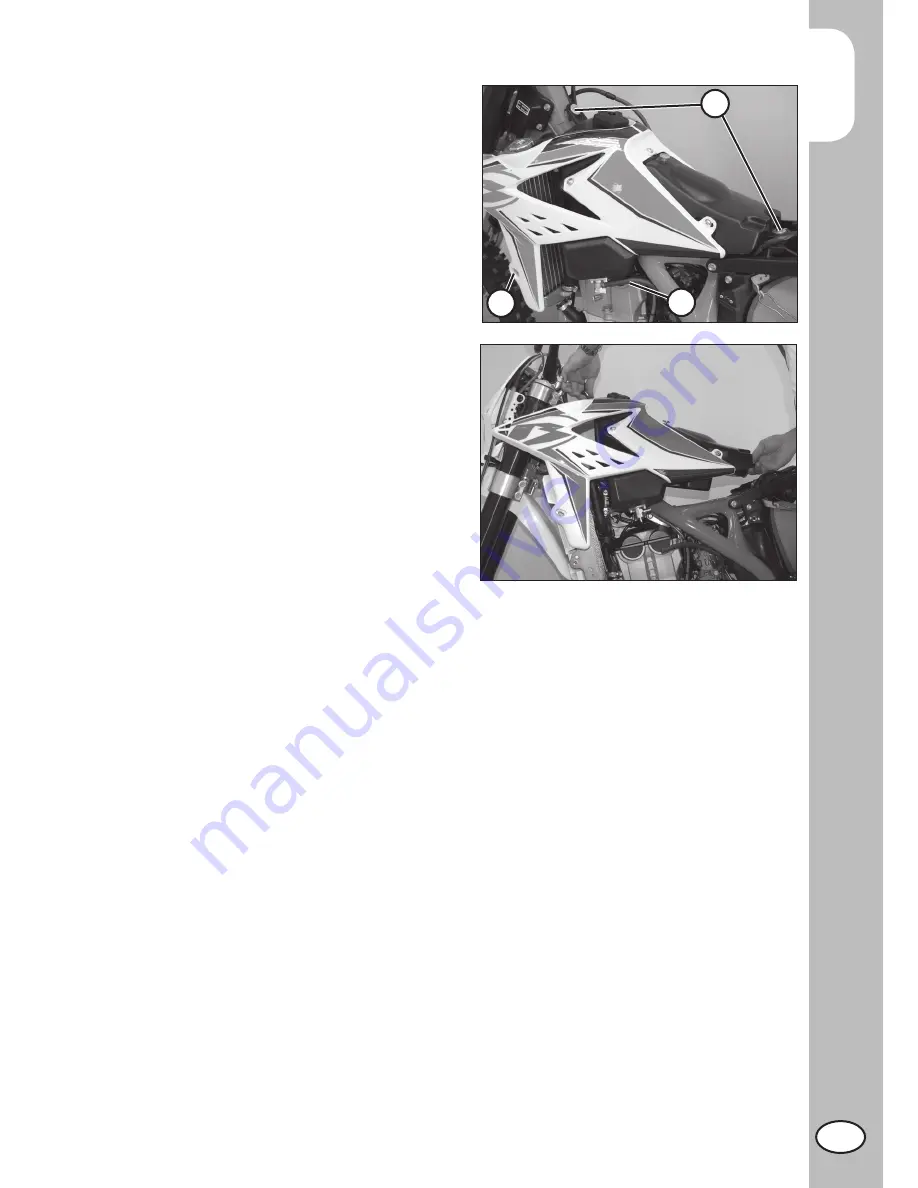
3
CHECKS AND MAINTENANCE
49
GB
B
C
A
SPARK PLUG
To accede to spark plug, is necessary to
take off saddle and the fuel tank.
To remove the fuel tank proceed as follows.
Unscrew the two screws
A
, unscrew the
screw
B
(both side). Close the fuel tap (OFF
position) and disconnect the pipe fuel
C
from the fuel tap.
Lift the fuel tank.
Keeping the spark plug in good condi-
tion makes for reduced consumption and
optimum engine performance.
It is advisable to remove the spark plug
when the engine is hot (and naturally off)
because the carbon formation and the
colour of the insulator provide important
information on carburetion, lubrication,
and the general condition of the engine.
Note
Black spark plug = mixture is rich
Light brown spark plug = mixture is correct
White spark plug = mixture is lean
This operation must be performed with the
utmost care to avoid severe hand burns.
Always wear protective gloves.
To carry out the check, simply remove the
current cap and then unscrew the spark
plug using the spanner provided.
Carefully clean the electrodes using a
wire brush. Blow the spark plug with com-
pressed air to prevent any residues from
getting into the engine.
Summary of Contents for RR 350
Page 34: ...34 GB ...