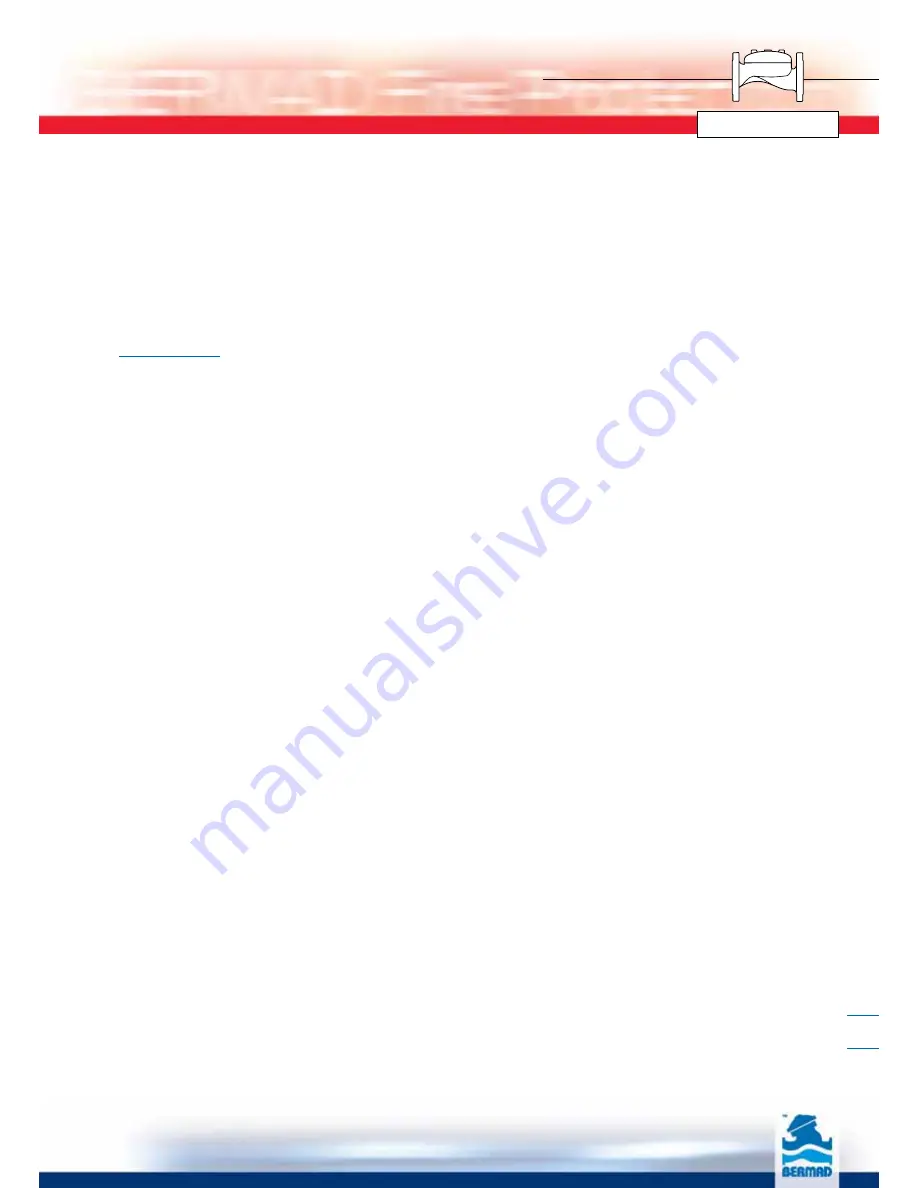
BERMAD
Fire Protection
400 Series
FP 400E Installation, Operation
&
Maintanence
Placing in Service/Resetting
The deluge valve and the control trim shall be Place in
Service with accordance to the most recent IOM
procedures for the specific model.
After all relevant instructions are performed, slowly open
the supply-isolating valve and check that no water flows
into the system.
The system is now operational and in stand-by mode.
Maintenance
Bermad Deluge Valves require no lubrication, no packing
tightening, and require minimum maintenance.
Removing the System from Service
Warning: When taking a deluge system out of service,
a fire patrol should be established in the system area.
If automatic fire alarm signaling equipment is utilized,
the proper authority should be notified that the system
is being removed from service. The insuring body and
owner’s representative should also be notified when the
system is being taken out of service.
WARNING:
Do not turn off the water supply to make repairs without
placing a roving fire patrol in the area covered by the
system. The patrol should continue until the system is
back in service.
Prior to turning off any valves or water supply, notify local
site fire officials.
Removal Instructions
1. Shut off the main supply-isolating valve.
2. Close the priming line valve to the deluge valve
control chamber.
3. Open all drain valves.
4. Release the water pressure from the control chamber
of the deluge valve by pulling the manual emergency
release.
5. Place “Fire Protection System Out of Service” signs in
the area protected by the system.
Inspection and Testing
1. Warning: Do not turn the water supply off to make
repairs without placing a roving fire patrol in the area
covered by the system. The patrol should continue
until the system is back in service.
2. Prior to turning off any valves or activating any
alarms, notify local security guards and the central
alarm station, if used, to avoid signaling a false alarm.
3. The deluge valve and the control trim shall be
maintained with accordance to the most recent IOM
procedures for the specific model. A periodic test
schedule should be established also with accordance
to the site conditions and owner regulations.
4. Take all additional measures as required by NFPA-25
“standard for the inspection, testing, and
maintenance of water-based fire protection systems”.
5. The system should be checked weekly for “Normal
Conditions”.
6. Clean the priming strainer prior to any resetting of the
deluge valve.
7. The deluge valve must be activated at full flow at
least annually. Take all necessary precautions to drain
water and prevent damage in the area protected by
the system.
8. After about five years of operation, replacement of the
diaphragm assembly is recommended. Remove the
cover, clean the valve body from sediments, clean the
control tubing entry holes, and install a new
diaphragm assembly in place.
Spare Parts
1. The Diaphragm Assembly is the only spare part
needed for the main deluge valve, see attached
“Valve Disassembly and Parts Breakdown Illustration”.
2. It is not recommended to store spare rubber parts for
long periods (rubber in improper storage conditions
can harden and crack).
3. Contact your Bermad representative and order new
rubber parts when required.
7