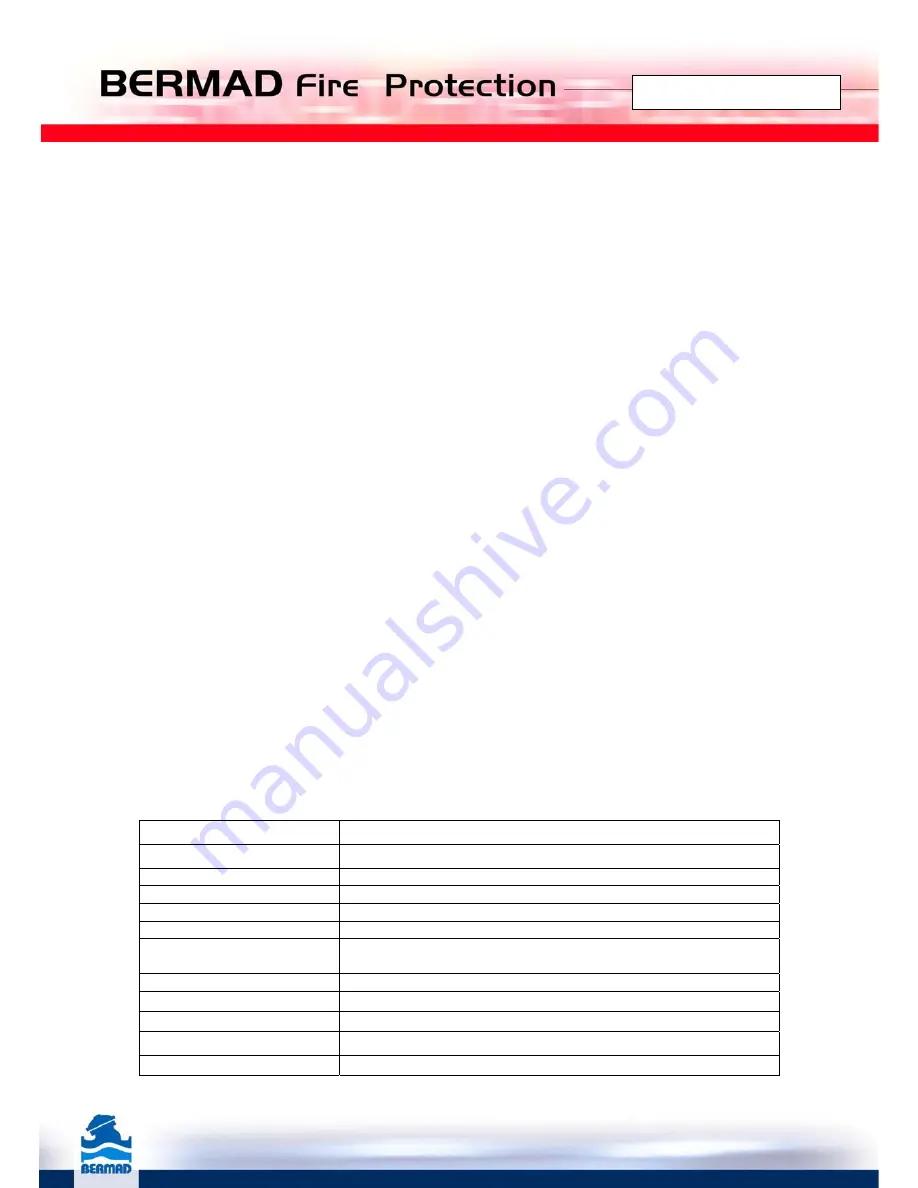
27
400E-Y Deluge Valve
4.
Placing in Service/Resetting
The deluge valve and the control trim shall be placed in Service in accordance to the instructions below. After all
relevant instructions are performed, slowly open the supply-isolating valve and check that no water flows into the
system.
4.1
Electrical Detection System:
A. Place the detector circuit in service.
B. Reset the Solenoid Valve by resetting the releasing control panel.
C. Test supervisory circuits in releasing control panel.
4.2
Hydraulically Control / Wet Pilot Systems:
A. Open the pressure supply isolating valve, allowing release system pressure to build up, check the entire
system for leaks.
B. Check the entire Wet Pilot line/Fusible Plugs for leaks, replace any fused temperature-release plugs.
NOTE:
Any automatic air or nitrogen pressure supply must feed the system through an orifice restriction. If a low
air pressure switch is utilized, test it by dropping the release line pressure, restore pressure after the test.
4.3
Pneumatic System Pressure Requirements:
C. Supply of day air or nitrogen is required to maintain a pneumatic pressure between 2.4-2.6 bar (35-38 psi).
D. The Pneumatic system shall use a clean, dependable and continuous compressed-air source using an
independent air compressor or an AMD (Air Maintenance Device) supplied by a dry nitrogen-gas or external
high air pressure source.
NOTE
: Any event of an air supply failure, slow leakage of air from the pneumatic system, will result in activation
of the Pneumatic Pilot Valve, causing the Deluge Valve to Open.
E. The Low-Pressure Alarm Switch is recommended and shall be set to operate at 2.2 bar (32 psi) with
decreasing air pressure. If necessary, adjustments can be made by following the manufacturer’s instructions.
F. Operate pneumatic pressure supply system, allowing release system pressure to build up to the above range
of 20 to 30, check the entire system for leaks.
G. Check the entire Fusible Plugs/Dry Pilot line for leaks, replace any fused temperature-release plugs.
NOTE:
Any automatic air or nitrogen pressure supply must feed the system through an orifice restriction. If a low
air pressure switch is utilized, test it by dropping the release line pressure, restore pressure after the test.
4.4
Placing In Service
A. Close all emergency release valves.
B. Open the priming-line valve .Check that there is no water flow from the Solenoid Valve.
C. Push and hold the Manual Reset button, this allows upstream water pressure to fill the Deluge Valve’s
control chamber through the Control Trim.
D. When the control chamber pressure gauge indicates full upstream pressure and is no longer rising, the
release system is reset.
E. Slowly Open the supply Isolating Valve and check that no water flows into the system.
F. Depress the Drip Check and drain any water from the system side of the Deluge Valve.
NOTE:
The system is now operational and in a standby mode, ensures that the following Set Conditions are met.
Table No. 3: Set Conditions (Normal Conditions)
Item Status
All Main Isolating Valves
OPEN
and sealed with tamperproof seals
All Manual Releases
CLOSE
position and sealed
Alarm Shut-Off Valve (11A)
OPEN
position
Priming Ball Valve (18B)
OPEN
Control-Chamber Gauge
OPEN
gauge valve, the gauge indicates pressure in control-chamber
Upstream Pressure Gauge
OPEN
gauge valve, the gauge indicates supply pressure to deluge
valve
Drip-Check Device (19B)
VENTED
: Push the knob to confirm that there is no leakage
Wet Pilot Line System
IN SERVICE
– no leaks in the system
Control Panel & Detections
IN SERVICE
and in there stand-by position.
Pneumatic Release System
ON
, maintained to 2.4-2.6 bar (35-38 psi) and functioning properly
Releasing Devices
CLOSED
with no leaks