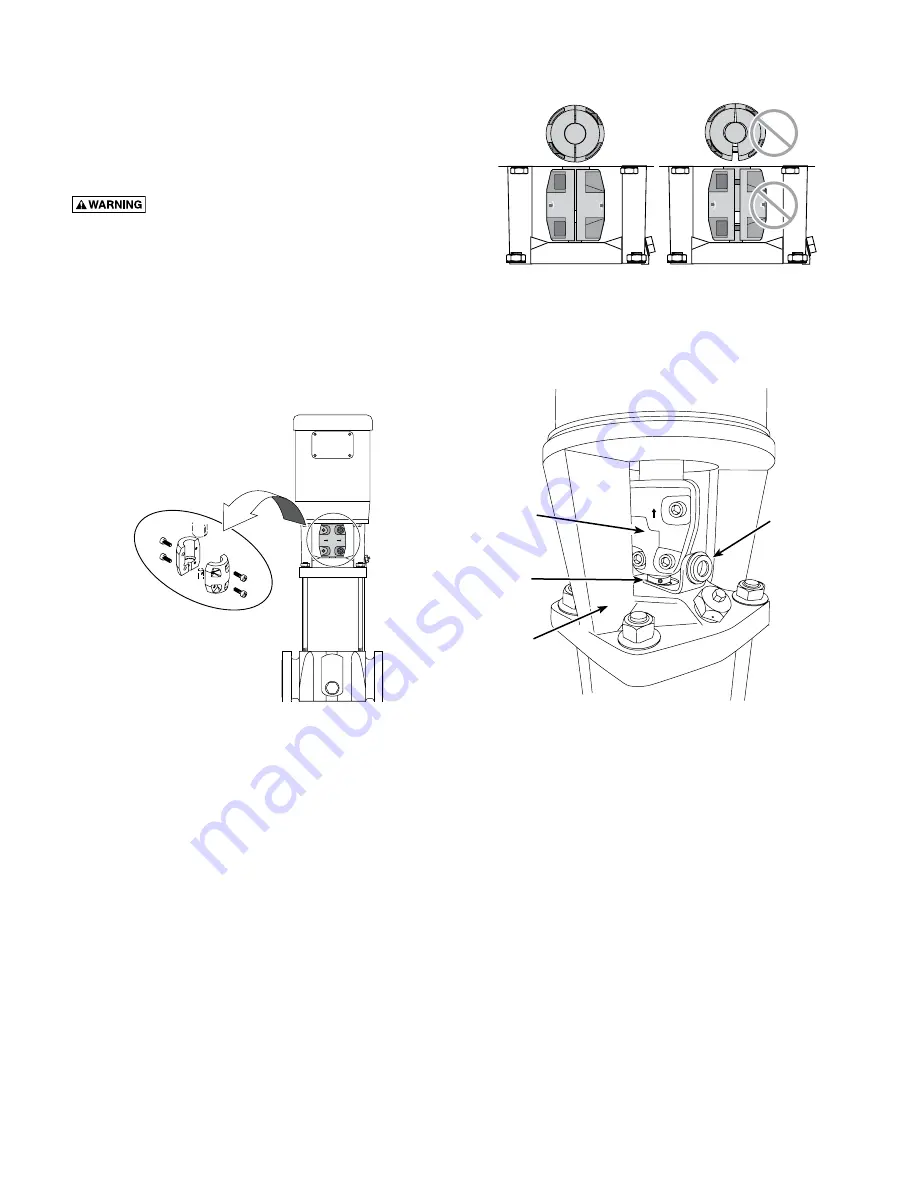
9
Maintenance
Motor Replacement
For Reference Numbers [shown as (3) or (5)], refer to the
Exploded View, Figure 14, for BVM2 and BVM4 Series
Models, Figure 16 for BVMI/X2 and BVMI/X4 Models,
Figure 15 for BVM8 and BVM16 Series Models, and
Figure 17 for BVMI/X8 and BVMI/X16 Series Models.
Risk of electric shock. Can shock, burn or
kill. Disconnect all power to the pump before servicing
or working on pump. Make sure that power is locked out
and that pump cannot be accidentally started.
1. Disconnect the power to the pump motor.
2. Close the nearest suction and discharge valves.
3. Remove the coupling guards (4) by prying them
loose with a screw driver.
4. Remove the socket head screws (3) and the coupling
halves (2) from the shaft (16A). For additional
reference, see Figure 10.
NOTICE: Socket head screws are metric. See
Table VIII for specific metric driver sizes.
5. Remove the shaft pin (5).
NOTICE: Pin has been discontinued and if present
does not need to be reinstalled.
6. Remove the capscrews (13), flatwashers (11), and
lockwashers (12) that hold the motor (1) and the
motor bracket (6) together.
7. Pull the old motor up and off of the motor bracket.
NOTICE: Note the location of the conduit box on
the motor.
8. Thoroughly clean the surfaces of the mounting
flanges on the new motor and the pump end.
9. Install the new motor on the pump with the conduit
box in the desired position.
10. Lubricate the capscrews (13) with oil.
11. Reinstall the lockwashers, flatwashers, and capscrews
that hold the motor and the motor bracket together,
then tighten evenly and diagonally. See Table VIII for
torque specifications.
12. Install the collar (13B) onto the shaft. With the collar
resting on the motor bracket, tighten the collar bolt.
13. Raise the height of the pump shaft by inserting the
stack height adjustment tool (see Figure 11B) below
the collar.
14. Reinstall the coupling halves (2) on the pump and
motor shaft.
15. Snug the socket head cap screws (3).
NOTICE: Torque settings are critical to prevent
coupling movement. Refer to Table VIII for torque
specifications.
16. Remove the stack height adjustment tool and secure
it to the top of a staybolt.
17. Rotate the shaft to make sure that there is no
interference. After assembly there should be a small
gap between the collar and the bracket. If rubbing is
noted, repeat steps 13, 14, and 15 to readjust pump
shaft height.
18. Reinstall the coupling guards by snapping them
into place.
NOTICE: The guards should be in place before the
unit is run.
19. Open the suction and discharge valves. Turn the
power back on.
Figure 11A - Make Sure that the Coupling Halves are
Evenly Tightened
Figure 10 - Remove the Socket Head Screws and the
Coupling Halves
Motor
Pump
Figure 11B - Using the stack height adjusting tool
Coupling
Collar
Stack Height
Adjustment Tool
Bracket