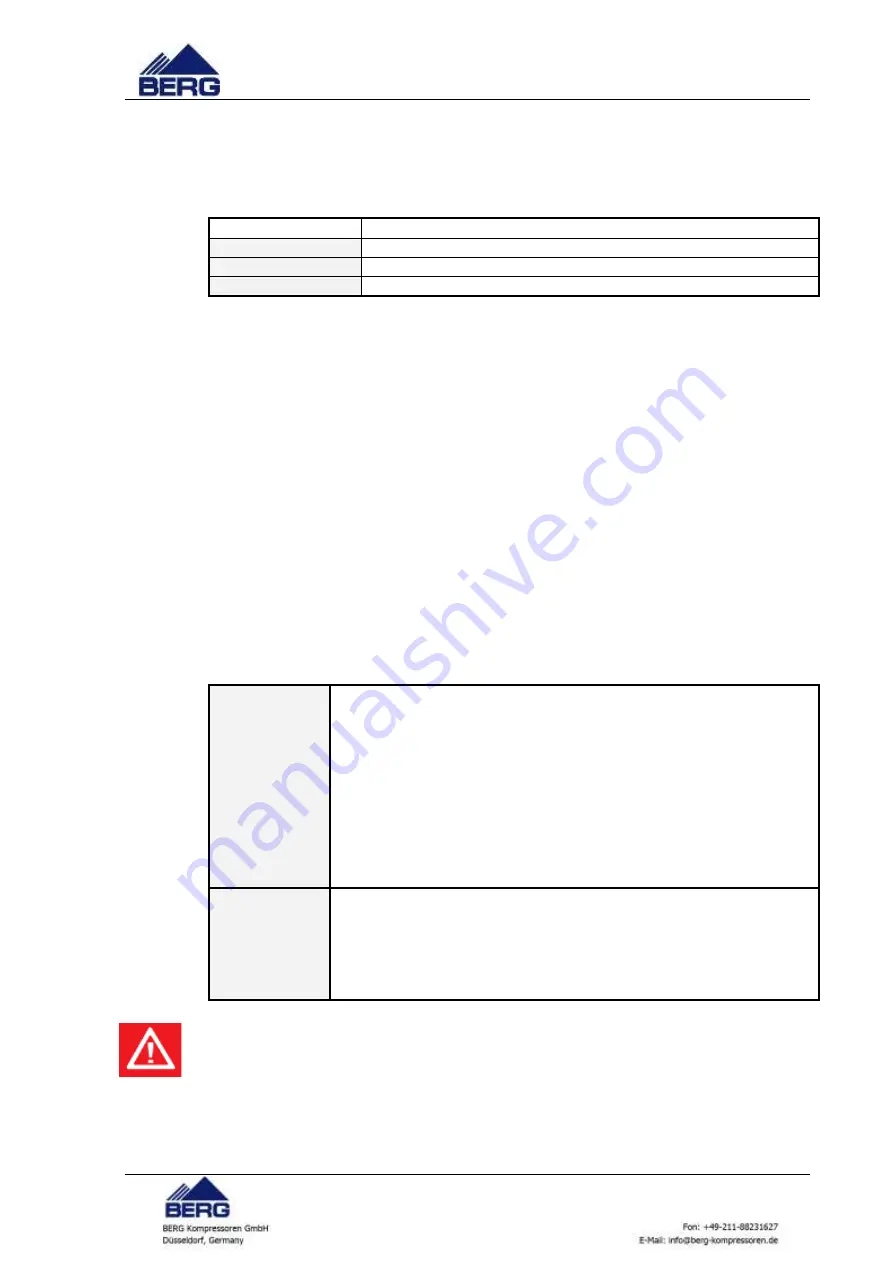
7.2. Maintenance and checks
7.2.1 Maintenance at the beginning of compressor use, after oil and drive belts (if present)
change
Maintenance interval Operation
after 2 work hours
-
check oil level in the receiver, top it up if necessary,
after 2 work days
-
check oil level in the receiver, top it up if necessary,
after 1 week of work
-
check oil level in the receiver, top it up if necessary,
7.2.2 Daily maintenance
-
visually inspect the state of pneumatic and oil conduit connections,
-
check the air overpressure gauge and temperature indicator for correct readings,
-
check the compressor performance for unusual symptoms, such as excessive noise
and vibration,
-
check oil level,
7.2.3 Periodic maintenance
Every 1000 work hours:
-
check the air filter for contamination and replace if necessary (in case of higher air dustiness,
more frequent cleaning and changing of the filter is recommended),
-
check the condition of the elastic coupling,
-
clean the air and oil cooler ribs if necessary.
7.2.4 Warranty and post-warranty checks
every 2000 work
hours
or after 1 year
-
change the filter mat at the cooling air inlet,
-
change the air filter cartridge,
-
check electric clamp terminals, fasten if necessary,
-
clean the air and oil cooler ribs,
-
test the non-return valve for proper functioning,
- check the condition of elastic coupling,
-
check the tubing for leaks, mend if any,
-
test the pressure switch for proper functioning,
-
check the oil temperature indicator,
-
check the condition of safety valve,
-
check the motor thermal protection setting.
every 8000 work
hours
or after 1 year
In addition to the activities required after 2000 work hours:
-
change the filter mat at the cooling air inlet,
-
change the air filter cartridge,
-
change oil filter,
-
change oil,
-
inspect the electric system and check it for proper functioning.
During the warranty period, the checks must be performed only by one of the servicing
companies listed in the Warranty Book