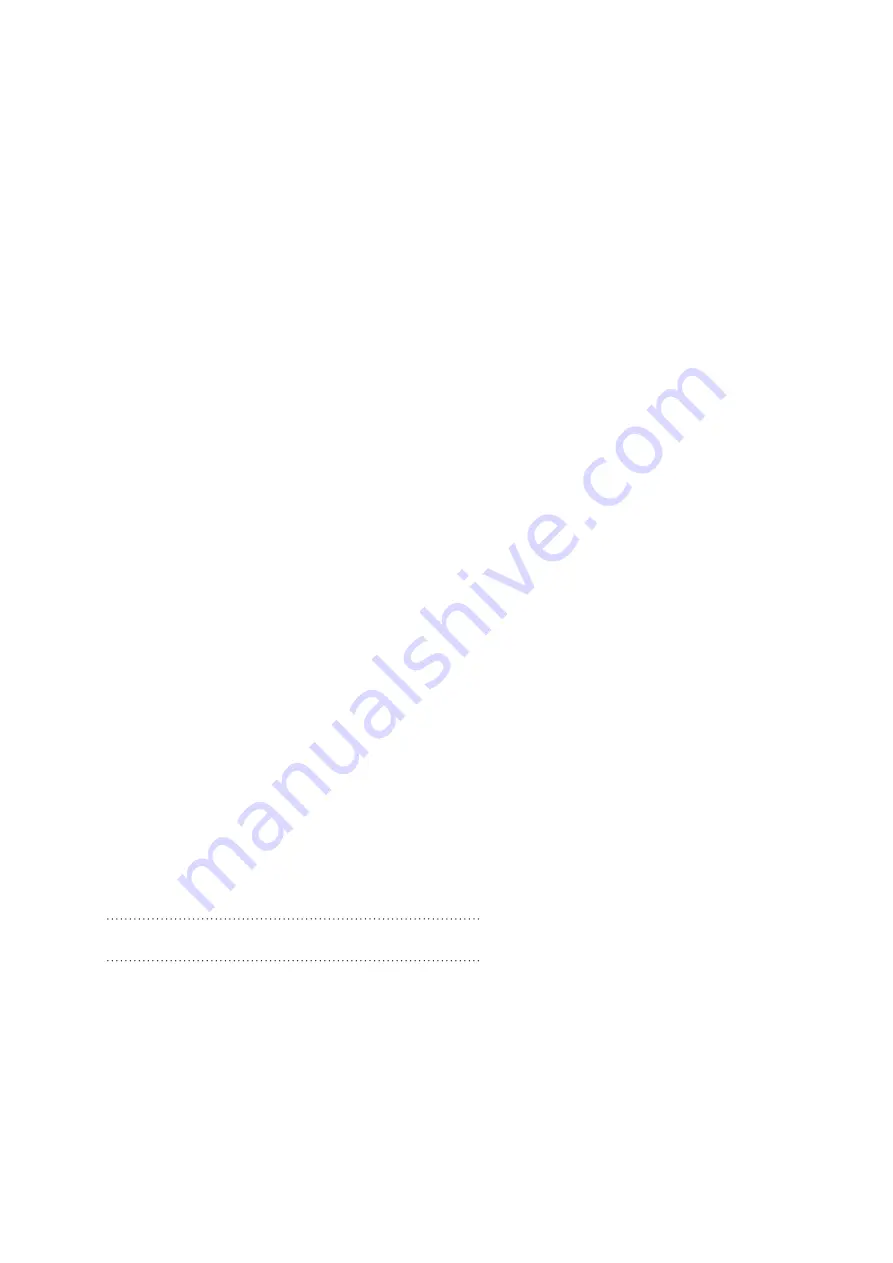
OIL BURNERS MAINTENANCE
INSTRUCTIONS
General information
Keep the boiler room clean. Ensure that the boiler
room has permanent fresh air intake. Switch off before
dismantling the oil burner.
At hinged mounting, make sure that an automatic safety
switch is fitted, so that the burner cannot start when
theswing door is open.
Don´t use the oil fired boiler to burn paper or
rubbish,unless the boiler is especially fitted with a hinged
door tomake this possible.
Don´t fill tank while burner is working.
Starting precautions
Make sure that the oil tank is not empty
Make sure that the valves on oil and water supply pipes
areopen.
Make sure that the boiler flue damper is open.
Make sure that the boiler thermostat is set at the correct
temperature.
Switch on the current. Most relay systems have a
delayed action so that the burner will not start for
perhaps 20 seconds.
With heavy oil the delay will be longer as the burner
will notstart until the oil in the preheater reaches the
requiredtemperature.
If the burner will not start
Press the reset button on the relay. Check that the
thermostats are correctly adjusted.
Don´t forget the room thermostat, check that any
fusesare intact and main switch is on.
If the burner starts but does not ignite
Make an attempt to start the burner.
Never make close repeated start attempts.
Don´t restart the burner until the boiler is free from oil
gases.
If the burner still does not ignite send for the service
engineer.
When switching off during summer
Always use the main switch to cut out the burner even
when adjusting the burner or cutting off the heating for
ashort time. For longer periods of shut down, close all
valves and the oil supply stop-cock.
Clean the filter and nozzle by washing in petrol or
paraffin.
Make sure the filter medium is not damaged or defective.
Protect electrical gear from damp.
Warning
Never stand too near or put your face to the inspection
or fire door, when the burner is about to start.
Never use a naked flame to ignite oil if the electrical
ignition fails.
Always wait for about 10 minutes for the unburnt gases
to disperse before restarting the oil burner if it has failed
to ignite previously.
Installed by:
Tel:
170 025 01 2012-04-16
Summary of Contents for STERLING 40 ST108PL
Page 2: ......
Page 16: ......
Page 18: ......
Page 19: ......
Page 20: ...Enertech AB P O Box 309 SE 341 26 Ljungby www bentone se www bentone com ...