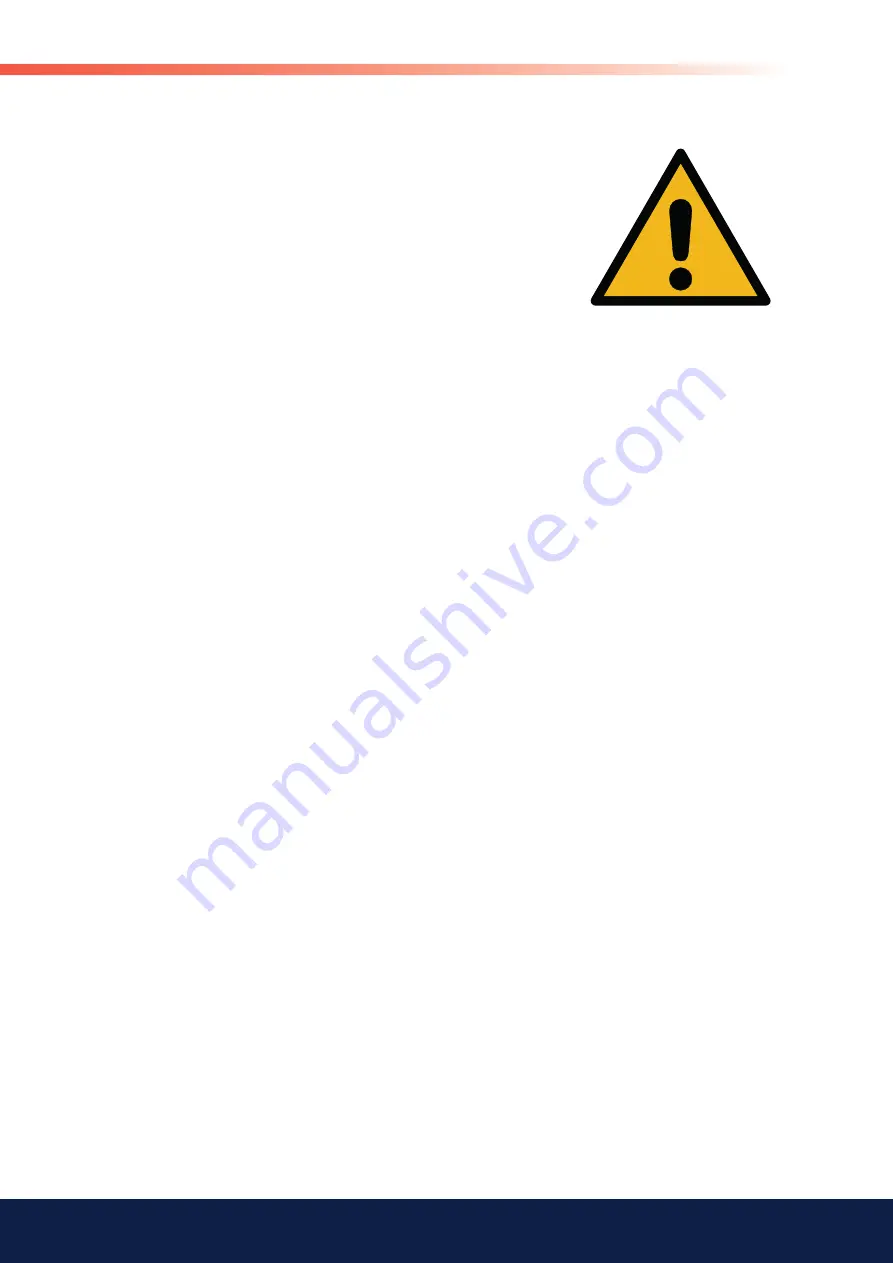
5
• Prior to commissioning, the following points should be checked:
-
all fi tting and installation work has been completed and approved.
-
the electrical installation has been carried out properly, the correct
fuses added to circuits and measures to safeguard enclosures on
electrical devices and all wiring have been checked.
-
fl ue gas ducts and combustion air ducts are not blocked.
-
all actuators and control and safety devices are in working order and
set correctly.
Service
• Service should be performed after approx. 3,000 working hours, but
no less than once a year.
• Only authorised personnel should perform the service.
• Before obtaining access to terminals, all supply circuits must be
disconnected.
• Be careful: certain parts exposed after separation of the burner can be
hotter than 60 °C.
• Care should be taken by the installer to ensure that no electrical
cables or gas pipelines are crushed or damaged during installation or
servicing.
• Only spare parts recommended by Enertech should be used.
What to do if you smell gas
• Prevent open fl ames or sparking, e.g. do not turn lights on or off, do
not use any electrical appliances, do not use mobile phones. Open
windows and doors. Close the gas ball valve. Warn residents; do not
use doorbells. Vacate the building. Notify the company/installer or gas
supplier once the building has been vacated.
• Turn off the equipment and take the boiler out of operation. Open
windows and doors. Notify the company/installer.
• Check that the burner is approved for the intended grade of gas and
connection pressure.
• No safety systems on the burner may be disconnected.
• General advice on how to eliminate a fi re.
• One or more boilers for solid or liquid fuel whose total rated output
exceeds 60 kW should be installed in a separate boiler room. An
airlock should be the only way a separate boiler room is connected
to evacuation routes from residential buildings in activity class 3, and
offi ces in activity class 1 that do not constitute an integrated part
of an industrial activity or similar activity. Ensure that local rules and
regulations are observed.
• The term “separate boiler room” refers to boiler rooms which are
specially designed to provide protection against the starting and
spreading of fi re and the production and spreading of combustion gas.
Ensure that local rules and regulations are observed
.
• Separate boiler rooms and fuel stores immediately next to a separate
boiler room should be designed as individual fi re compartments.
Ensure that local rules and regulations are observed.
Summary of Contents for 354012011601
Page 9: ...9 2 1 Description BFG 1 7 8 10 11 12 13 14 15 16 22 1 2 3 4 5 6 24 23...
Page 12: ...12 7 8 10 9 1 2 3 5 6 12 4 3 1 Description STG 23 24 16...
Page 18: ...18 5 Electric Equipment LME 5 1 Wiring diagram Alt 1 Acc to DIN 4791 Alt 2 Alt 3 172 615 82 2...
Page 22: ......
Page 23: ......
Page 24: ...Enertech AB P O Box 309 SE 341 26 Ljungby www bentone com...