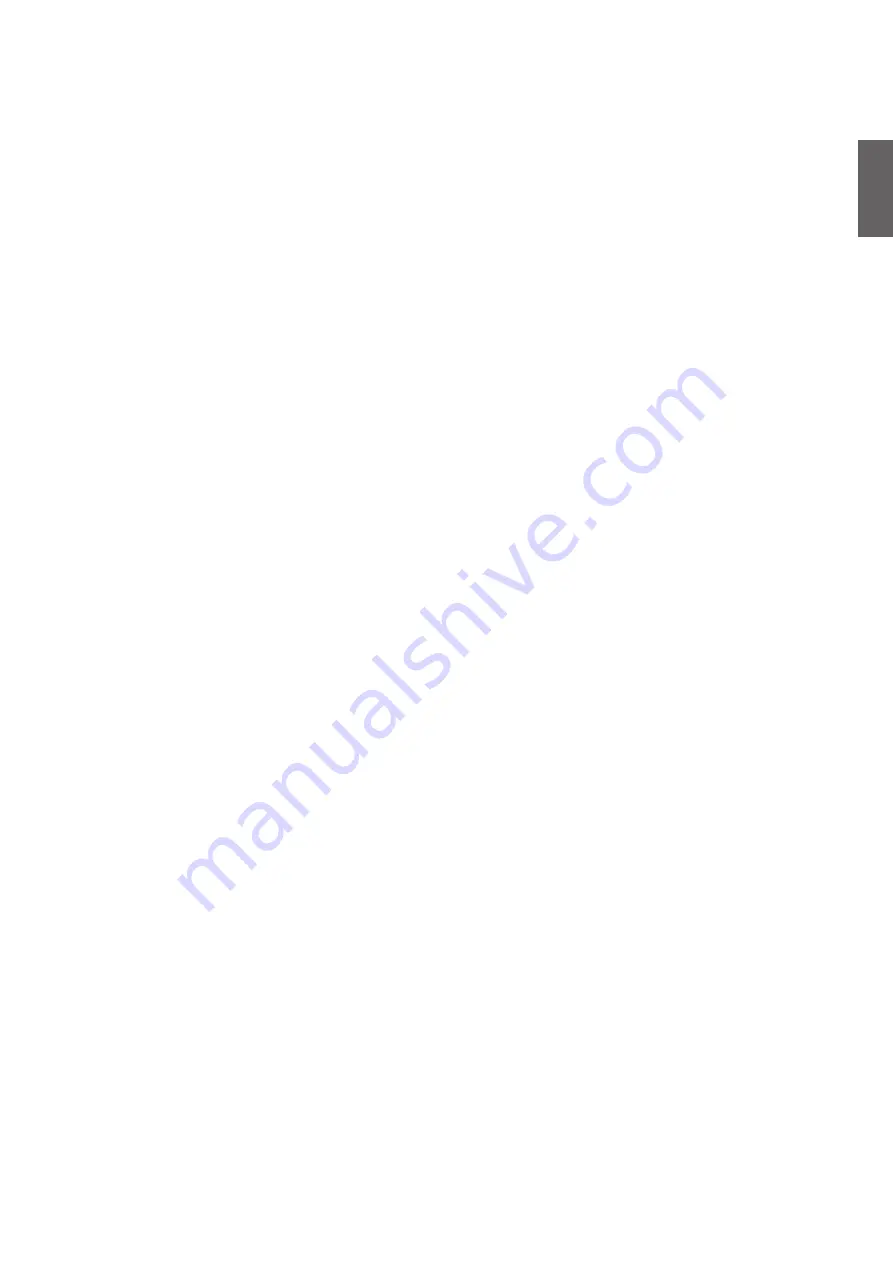
23
EN
4) INSTALLATION
4.1) FITTING OF THE RACK
4.1.1) RACK IN NYLON (FIG.8).
Position the rack at a height of 102 mm from the centre line of the fixing slot provided on the base on which the foundation plate will be fitted. At that
height, drill a hole on the gate and provide for a M6 threading.
Keep to the P tooth pitch, even from a section of rack and another. To this purpose, it could be useful to join another section of rack (Part. C)
Then fix the rack with V screws, taking care, once the actuator is installed, that 1-mm backlash is left between the rack and the tow wheel (seei Fig.7).
To this purpose, use the slots on the rack.
4.1.2) RACK IN FE 12X30MM (FIG.9).
Position the spacers D by welding them or fitting them with screws to the gate, at 135 mm height from the centre line of the fixing slot provided on the
base on which the foundation plate will be fitted. Fix the rack.
Keep to the P tooth pitch, for all sections of the rack. To this purpose, it could be useful to connect another section of rack (Part. C)
Then fix the rack with V screws, taking care, once the actuator is installed, that 1-mm backlash is left between the rack and the tow wheel (seei Fig.7).
To this purpose, use the slots on the rack.
4.2) POSITIONING OF THE FOUNDATION PLATE (FIG.5-6)
It is very important to keep to dimension X shown in Fig.2. This value depends on the type of rack used:
X = 11 mm for rack in nylon
X = 13 mm for rack in iron, 12x30mm
Preset a corrugated tube (Fig.2 -A) for the passage of power supply cables and connection wires for the accessories.
Check that, at the end of the fitting, the foundation plate is perfectly parallel with respect to the wing.
4.2.1) FITTING WITH SCREW ANCHORS ON CEMENT BASE (FIG. 3)
Through 4 “T” screw anchors in steel (not supplied), firmly anchor the foundation plate to ground by means of 4 bolts “B” (not supplied). Use the founda-
tion plate as drilling template.
Fix the geared motor to the plate by means of the 4 screws V (M10x70), with the relevant plain washers R and knurled washers, as indicated in the figure 6.
4.2.2) INSTALLATION WITH CEMENT (FIG. 4-5)
In this case, after providing for an adequate foundation hole, pour cement on the plate, taking care of the plate level. Check that the threaded inserts (I)
for the fitting screws are clean and cement free.
Wait for the hardening of the cement.
Fix the geared motor to the plate by means of the 4 screws V (M10x70), with the relevant plain washers R and knurled washers, as indicated in the figure 6.
4.2.3) HEIGHT ADJUSTMENT OF THE GEARED MOTOR
The height of the geared motor (10mm max) can be adjusted in height, with respect to the foundation base, by 4 dowels G.
In this case, BEFORE fitting the geared motor to the plate, apply the 4 adjustment dowels G, by inserting the 4 nuts D in the special housings located at
the bottom of the geared motor.
Then adjust the 4 dowels by lifting the geared motor at the desired height. Fix the motor by firmly tighten the 4 screws V4 (M10x70) and related flat wa-
shers R and knurled washers Z, as shown in the figure 6.
4.3) POSITIONING OF THE LIMIT SWITCH BRACKETS (FIG.10)
Manually open the gate and leave a clearance from 1 to 3cm according to the weight of the gate between the main door and the mechanical stopper
A. Fix the bracket to the limit switch S by using the grains G, so that the limit switch microswitch F is pressed. The same operation should be repeated
with gate in the closing phase.
N.B.: The limit switch bracket should be positioned so that the gate can be stopped without hitting the mechanical stopper.
5) MANUAL OPERATION (FIG. 13-14-15)
In the event of power failure or malfunction, to manually operate the gate proceed as follows:
- After inserting the customized key C, turn it anti-clockwise and pull the lever L (opened padlock)
- The geared motor is unlocked and the gate can be moved by hand.
- To return to the normal operating mode, close the lever L again and manually activate the gate until it is geared.
6) HOW TO POSITION THE LIMIT SWITCH BRACKETS
Open manually the gate and leave approximately of 1÷3cm, depending on gate weight, between gate and positive mechanical stop A; tighten the limit
stop flask S with the grains G to press the limit stop micro. Repeat the sequence with closing gate.
7) HOW TO INSTALL THE MAGNETS (BULL 624 TURBO.S OR ACCESSORY MLS) FIG.12
The magnets are housed in special supports (fig.12-”A”). These magnets are to be fitted to the limit switch brackets or the rack and cause the triggering
of sensors when they approach them.
7.1) FITTING ONTO THE LIMIT SWITCH BRACKETS
The bases are complete with hooking tongue allowing the fitting of the magnets to the limit switch bracket supplied with the operator, as shown in Fig.12-B.
This type of fitting allows to rapidly adjust the position of magnets. After calculating the correct distance, fix the support in the correct position by means
of a screw, so as to avert the moving of the bracket.
7.2) FITTING ONTO THE RACK
As an alternative, the supports can be fitted directly to the rack, by using the slots shown in Fig. 12-C. This fitting mode does not allow for subsequent
regulations. It is therefore advised to make some trials with temporarily fitted supports before carrying out the final fitting.
IMPORTANT:
The correct distance of the magnet with respect to the sensor depends on the installation characteristics. This space cannot be preset
and must be adjusted on a trial basis.
The distances regarding the triggering of the sensor (value X) with respect to distance K of 3 and 35 mm, which are shown in Fig. 12 are only indicative.
In any case, distance K must not exceed 35 mm as a higher distance will not allow the triggering of the magnetic sensor.