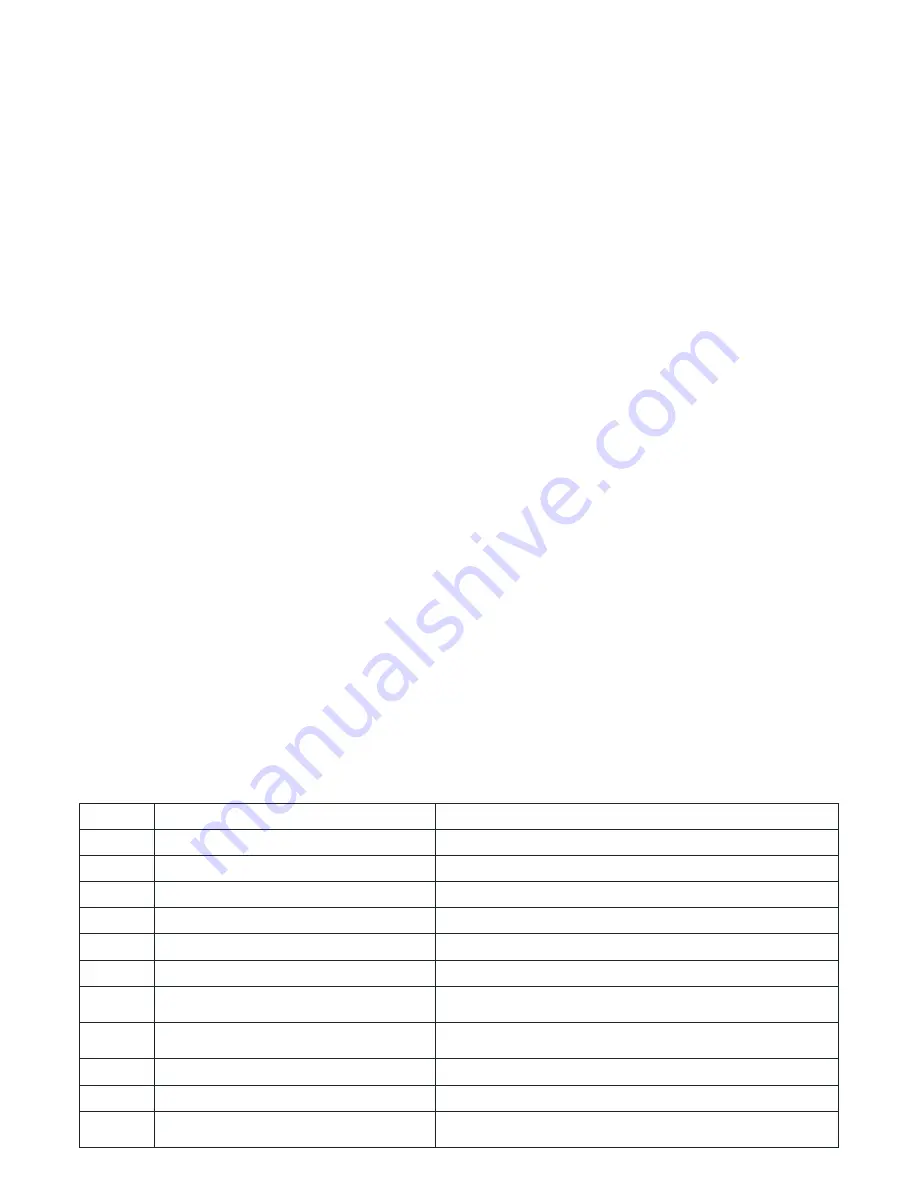
18
BRAKING
With the ENC=OFF logics, braking is given by the TSM1/TSM2 parameter value referred to the TM1/TM2 operating time. For example,
if the operation of motor 1 lasts 20 seconds and TM1=24s and TSM1=8 are preset, 4 s braking will result (20-(24-8).
With ENC=ON logics, braking is calculated as a percentage on the space covered during the complete operation.
FUSES
F1: F6.3A (230VAC) / F10A (115VAC) – Motor protection
F2: T315mA (230VAC) – T500mA (115VAC) – Protection for primary transformer
TRANSMITTER REMOTE LEARNING
If the transmitter code is already stored in the receiver, the remote radio learning can be carried out (without accessing the control
unit).
IMPORTANT: The procedure should be carried out with gate in the opening phase, during the TCA dwell time.
Proceed as follows:
1 Press the hidden key of the transmitter, the code of which has already been stored in memory.
2 Within 5 seconds, press the already memorised transmitter key corresponding to the channel to be matched to the new transmitter.
The flashing light switches on.
3 Within 10 seconds, press the hidden key of the new transmitter.
4 Within 5 seconds, press the key of the new transmitter to be matched to the channel selected at item 2. The flashing light switches
off.
5 The receiver stores the new transmitter code and exits from the programming mode immediately.
TYPES OF INSTALLATION
AUTOMATIC SYSTEM WITH ELECTROMECHANIC LIMIT SWITCHES AND CONNECTION TO ENCODER
In this operating mode, the NOT=ON logics and the ENC=ON logics must be preset.
Start a self-test operation, as indicated in the AUTO Menu.
At completion of the lelf-learning, the value of all torques and the TDMO/TDMC value are preset by the control unit.
If an obstacle is present, the Encoder acts as anti-crash sensor. Its sensitivity is adjusted by SEAV and SEAR parameters.
AUTOMATIC SYSTEM WITH ELECTROMECHANIC LIMIT SWITCHES AND WITHOUT ENCODER
In this operating mode, the NOT=ON logics and the ENC=OFF logics must be preset.
All parameters must be preset manually. In particular, values of TM1/TM2 must be some seconds higher than the actual operating
time.
AUTOMATIC SYSTEM WITH ELECTROMECHANIC LIMIT SWITCHES AND CONNECTION TO ENCODER
In this operating mode, the NOT=OFF logics and the ENC=ON logics must be preset.
Start a self-test operation, as indicated in the AUTO Menu.
At completion of the lelf-learning, the value of all torques and the TDMO/TDMC value are preset by the control unit.
In this case, the encoder not only acts as snit-crash sensor, but it also performs the stop function in the presence of limit switches.
AUTOMATIC SYSTEM WITH ELECTROMECHANIC LIMIT SWITCHES AND WITHOUT ENCODER
In this operating mode, the NOT=OFF logics and the ENC=OFF logics must be preset.
All parameters must be preset manually. In particular, values of TM1/TM2 must be some seconds higher than the actual operating
time.
ERROR MESAGES
Some messages that are displayed in the event of malfunctions are shown hereunder:
Enc1
Error, motor 1 encoder
Check the connection to motor 1 encoder
Enc2
Error, motor 2 encoder
Check the connection to motor 2 encoder
Amp1
Error, motor 1 obstacle
Check the presence of obstacles on the motor 1 leaf stroke
Amp2
Error, motor 2 obstacle
Check the presence of obstacles on the motor 2 leaf stroke
Err1
Error, check motor 1 circuit
Check connections to motor 1
Err2
Error, check motor 2 circuit
Check connections to motor 2
Err3
Error, check actiation relay
Ask for technical assistance
Err4
Error, check PHOTA photocell
Check connections, alignment of PHOT A photocell or obstacle
present.
Err5
Error, check PHOTC photocell
Check connections, alignment of PHOT C photocell or obstacle
present.
Err6
Error, activated sensitive edge (during self-set)
During self-setting, the safety edge was activated.
Err7
Error, activated stop (during self-test)
During self-setting, the STOP input was activated.
Err8
Error, activated input (during self-test)
During self-setting, a Start/Pedestrian/Open/Close input was acti-
vated.