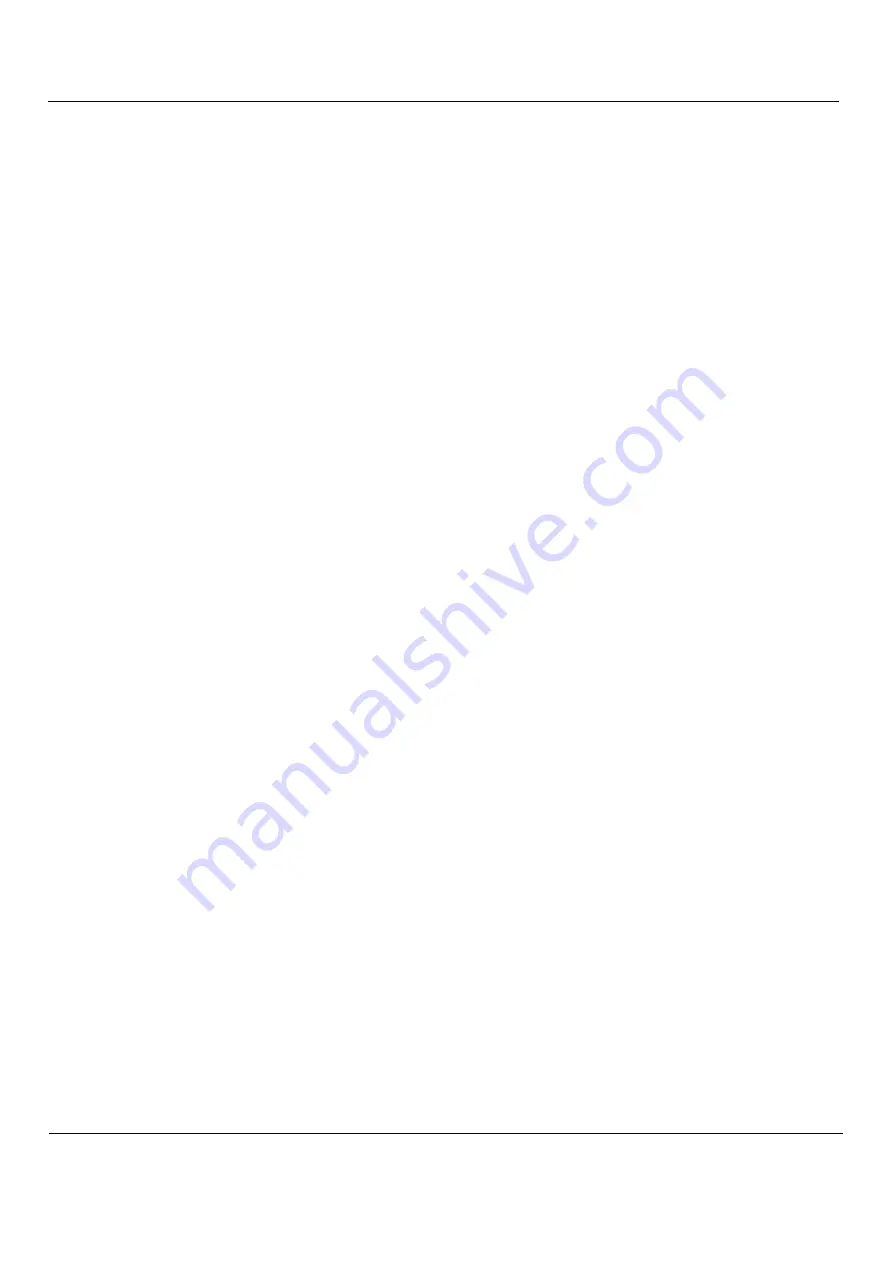
Benezan Electronics
Hard- and software development
Breakout Board Installation Guide
Nicolas Benezan, Stauffenbergstr. 26, 72108 Rottenburg
Phone: +49 (0) 7457/946365 0 benezan-electronics.de
Page
Netbob1 installation.docx22.09.2020
Functional description
In contrast to conventional breakout boards with LPT interface, which only pass on the signals from the PC and, if necessary,
adjust or amplify the signal levels, the Beamicon2 interface board has a powerful 32-bit processor, which can generate step and
direction signals in real time independently of the PC. The PC only sends coordinates at regular intervals via a network interface
(Ethernet IEEE802, 10MBit/s). All hardware-related operations run on the interface board, so that the PC is relieved of time-
critical tasks and is only needed for the user interface.
Much higher step rates are possible than with LPT port-based solutions, and the timing is more precise and reliable.
Compromises in the selection of the resolution in connection with the maximum possible speed are therefore no longer necessary.
Servo drives can also be operated with high resolution and speed. Step losses due to short "dropouts" of the PC (violations of real-
time conditions by competing processes) are excluded.
Even settings for pulse duration and distance, which are often difficult for the user to understand, can be completely omitted.
The breakout board always generates the step signals with a duty cycle of 50%. Changes of direction always occur in the middle
of the pauses between clock pulses. This ensures that always the maximum pulse duration matching the frequency is output.
Violations of the setup and hold time by simultaneous change of step and direction signal state are avoided.
PC / network connection
The data transfer from the PC software to the breakout board is done via an Ethernet network connection (IEEE802.3 10BASE-T).
The connection can be made with standard patch cables to the RJ45 socket ST1. Please note that the other four RJ45 sockets ST2
to ST5 (without LEDs) are not network connections but are intended for step/direction signals.
In contrast to similar products from competitors (e.g. Smoothstepper or Eding-CNC) no exclusive interface has to be reserved
on the PC, but the infrastructure of an existing network with switches can be used. There is also no need to change IP addresses or
otherwise interfere with the Windows Control Panel. The Beamicon2 software automatically detects the breakout board, even if it
is connected "somewhere" in the network. To ensure reliable operation, however, the following rules must be observed:
The breakout board must be connected either directly to the PC or to the first switch after the PC. A further switch may
only be added if only devices of the machine are connected to the second switch, e.g. within the control cabinet of the
machine. All devices not involved in machine control (Internet router, printer, NAS, etc.) must be connected to the first
switch or to additional switches behind the first.
The transmission speed between the PC and the first switch must be higher than the maximum data rate of any existing
Internet routers (DSL modem etc.). For home networks with few PCs 100MBit is recommended, for larger networks
Gigabit-Ethernet.
Since no TCP/IP is used but a separate protocol, this cannot be forwarded by routers, external firewalls, proxies, etc.
Therefore only so-called "unmanaged switches" may be used between the control PC and the CNC pod.
Switches must support Fast Forward and Store-and-Forward (virtually all modern switches meet this criterion)
Hubs are also allowed for test purposes (listening with diagnostic tools on taps), but are not recommended.
The data traffic of the machine controller must not be routed via slow (DSL modem) or unreliable (wireless) connections
(WLAN). All wireless interfaces are therefore intentionally hidden.
If the board is connected directly to the PC and the PC interface does not support automatic crossover, a crossover cable must
be used (usually marked with a red plug or "X"). The network interface is galvanically isolated from the PC. Power-over-Ethernet
(PoE) is not supported.
Power supply
The breakout board can be supplied with an operating voltage of 15 to 75V DC. In most cases the power supply unit can be used
for the motor voltage. Only if 24V is required for external consumers (inductive proximity switches, holding brake), an extra
power supply unit is necessary.
For fans, external sensors or additional circuits the board provides regulated 5V and 12V outputs (terminal X1). A 3-pole plug-
in socket is provided for standard PC fans with 12V (ST7). The outputs are short-circuit proof. However, since the same voltage
regulators are also used for the internal supply, malfunctions can occur in the event of a short circuit. In case of overload or
undervoltage at the 12V connection the E-Stop LED (red) lights up.
Power stage signals
The outputs of the step/direction signals are equipped with RJ45 sockets so that BEAST stepper motor power amplifiers and UHU
servo controllers can be connected with standard Ethernet patch cables. To avoid confusion with the network cables, it is
recommended to use different cable colours, e.g. grey for the network data lines, yellow for the step/direction signals.