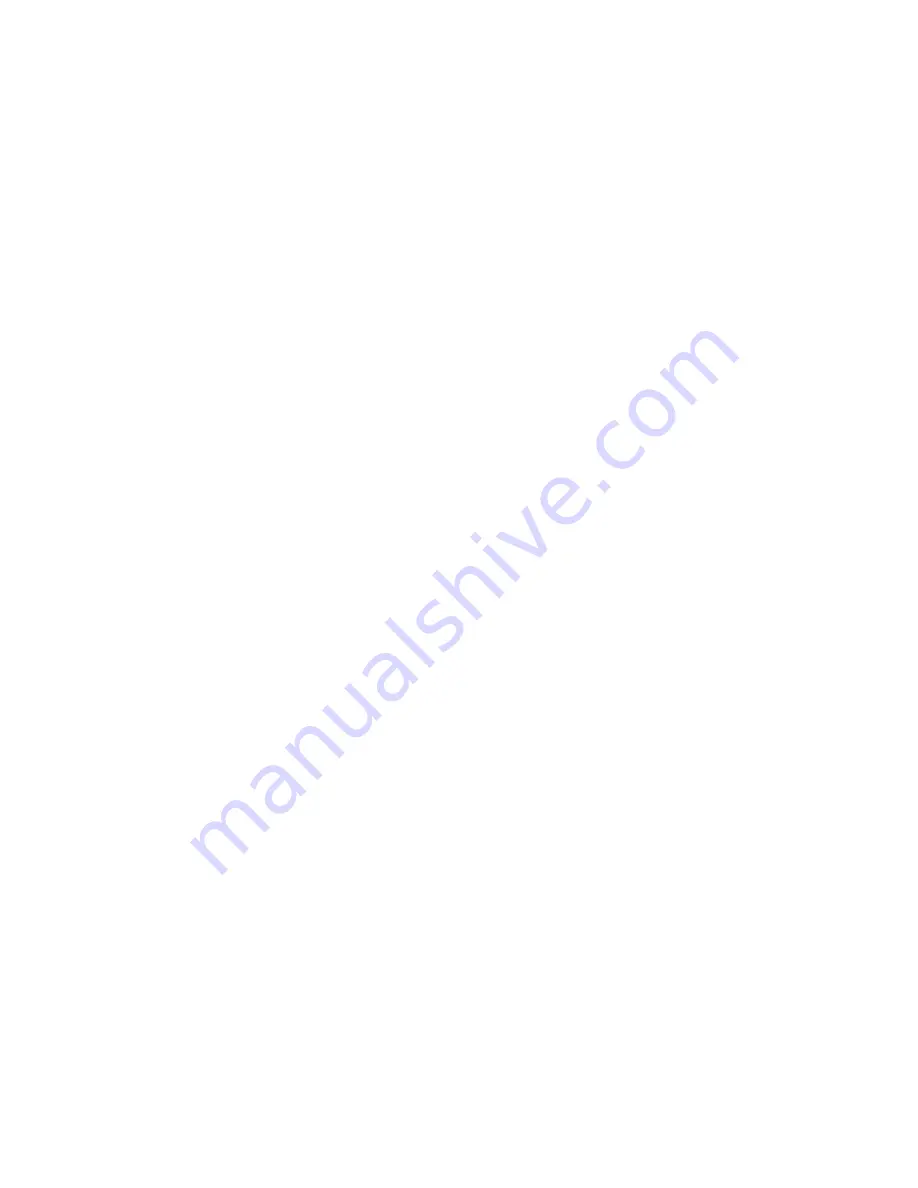
11
3. Remove as much road dirt and grease from the exterior
of the compressor as possible.
4. Remove the discharge and inlet fittings, if applicable,
and note their position on the compressor to aid in
reassembly.
Note: If a cylinder head maintenance kit is being
installed, stop here and proceed to PREPARATION FOR
DISASSEMBLY. If replacing the compressor continue.
5. Remove any supporting bracketing attached to the
compressor and note their positions on the compressor
to aid in reassembly.
6. Remove the front flange mounting bolts/nuts and
remove the compressor from the vehicle.
7. Inspect the drive gear and associated drive parts for
visible wear or damage. If the compressor drive gear
is worn or damaged, the drive gear must be removed
and replaced.
Refer the Engine Manufacturer's service
manual to address the associated engine drive parts.
8. If the compressor is being replaced, stop here and
proceed to “Installing the Compressor” at the end
of the assembly procedure. (Note: Replacement
compressors do not come with the drive gear pre-
assembled on the compressor. If the drive gear is in
good condition, the drive gear and attachment nut can
be removed from the old compressor and transferred
to the new compressor or a new drive gear must be
purchased through a Volvo
®
distributor and installed on
the compressor.
PREPARATION FOR DISASSEMBLY
Remove the balance of road dirt and grease from the
exterior of the compressor with a cleaning solvent. If a rear
end cover or end cover adapter is used on the compressor
being worked on, mark it in relation to the crankcase. It is
recommended, but not specifically necessary, to mark the
relationships of the cylinder head (13), cooling plate (15),
valve plate assembly (16), and crankcase (21).
A convenient method to indicate the above relationships
is to use a metal scribe to mark the parts with numbers or
lines. Do not use marking methods such as chalk that can
be wiped off or obliterated during rebuilding.
Prior to disassembly make certain that the appropriate kits
and/or replacement parts are available. Refer to Figure 10
during the entire disassembly and assembly procedure.
What follows is a description of a complete disassembly,
actual maintenance may only need to include portions of
these instructions.
DISCHARGE JUMPER ASSEMBLY & FITTINGS
Note: The discharge jumper (37) must be removed in order
to remove the inlet fitting (35) and to service the unloader
mechanism.
1. Loosen and remove the four discharge jumper washers
(39) and discharge jumper screws (38) that secure
the discharge jumper (37) to the cylinder head (13).
Remove the discharge jumper (37) and the two o-rings
(40). Loosen and remove the safety valve (12) from the
discharge jumper (37), if necessary.
2. The inlet fitting (35) and top coolant fitting (36) were
pre-installed on the compressor by Bendix to ensure
proper positioning when the coolant and air induction
lines are installed. Unless the inlet fitting (35) and top
coolant fitting (36) have been damaged they should
stay intact. If it is necessary to remove the fittings, first
loosen the jam nut of the inlet fitting (35) and remove it
from the cylinder head (13). Then, loosen and remove
the top coolant fitting (36) from the cylinder head (13).
CYLINDER HEAD ASSEMBLY
3. To restrain the spring force exerted by balance piston
spring (8) of the unloader assembly, hold the unloader
cover (4) in place while removing the two unloader
cover cap screws (2). Carefully release the hold on the
unloader cover until the spring force is relaxed, then
remove the unloader cover.
4. Remove the unloader cover gasket (5).
5. Remove the unloader balance piston (6), its spring
(8) and the unloader piston (10) along with its o-rings
(7, 9 & 11) from the cylinder head (13).
6. Remove the six head bolts (1) from the cylinder head
(13).
Note: The five head bolts located towards the perimeter
of the cylinder head retain the cylinder head directly
to the crankcase. The single head bolt in the center
of the cylinder head holds the cylinder head, cooling
plate and valve plate assembly together; independent
of the crankcase.
7. Gently tap the cylinder head, cooling plate (15) and
valve plate assembly (16) with a soft mallet to break
the gasket seal between the valve plate assembly and
the crankcase (21). Lift the cylinder head with cooling
plate and valve plate assembly off the crankcase.
8. Remove the metal inlet reed valve/gasket (17).
9. Gently tap the cylinder head, cooling plate and valve
plate assembly with a soft mallet to break the gasket
seals. Then separate the cylinder head from the cooling
plate (15) and valve plate assembly and remove the
two gaskets (14) between them.