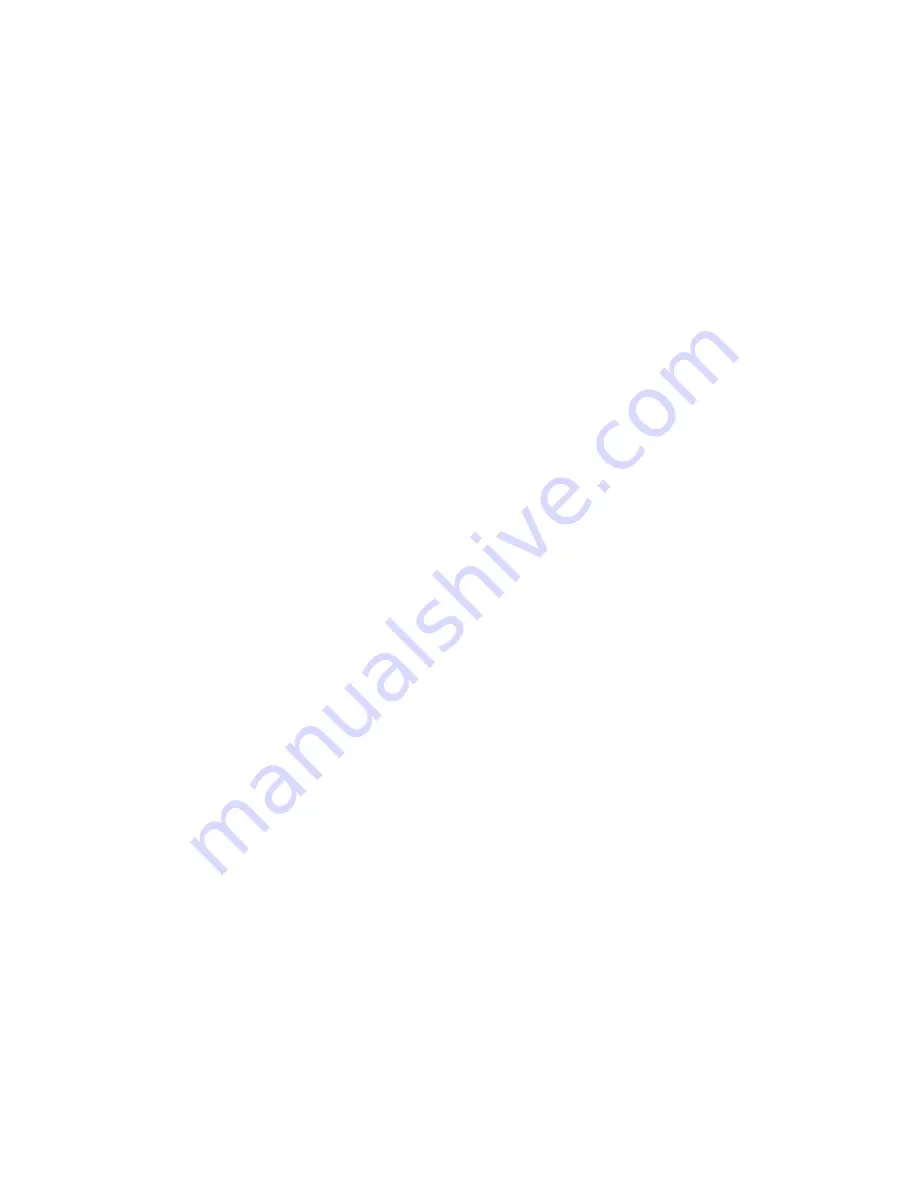
5
5. Remove piston (9) from the body (10) and retain for reuse.
6. Remove and discard o-ring (8) from piston (9).
7. Depress and hold the exhaust cover assembly (16) and
remove and discard retaining ring (17) from the valve
body (10).
8. Slowly release the holding force on the exhaust cover
assembly (16) to relax the spring.
9. Remove and discard the following parts:
a. Exhaust cover assembly (16)
b. O-rings (14 & 15)
c. Spring (13)
d. Inlet exhaust valve (11)
e. Retainer (12)
CLEANING AND INSPECTION
1. Wash all metal parts in mineral spirits and dry them
thoroughly.
(Note: When servicing the R-12DC
™
valve, all springs
and all rubber parts should be replaced.)
2. Inspect all metal parts for deterioration and wear, as
evidenced by scratches, scoring and corrosion.
3. Inspect the exhaust valve seat on the relay piston for
nicks and scratches which could cause excessive
leakage.
4. Inspect the inlet valve seat in the body for scratches
and nicks, which could cause excessive leakage.
5. Inspect the check valve seat in the R-12DC
™
valve cover
and make sure all internal air passages in this area are
open and clean and free of nicks and scratches.
6. Replace all parts not considered serviceable during these
inspections and all springs and rubber parts. Use only
genuine Bendix replacement parts, available from any
authorized Bendix parts outlet.
ASSEMBLY
Note: All torque specified in this manual are assembly torque
and can be expected to fall off slightly after assembly. Do
not re-torque after initial assembly torque fall. For assembly,
hand wrenches are recommended.
Prior to assembly, lubricate all o-rings, o-ring bores and any
sliding surface with a silicone lubricant equivalent to Dow
Corning #10.
Wash all remaining parts in mineral spirits and dry thoroughly.
Using the lubricant provided in this kit, lightly lubricate all
o-rings, o-ring grooves, body bores any sliding surfaces.
1. Install o-rings (14 & 15) in the exhaust cover assembly
(16).
2. Install o-ring (8) on piston (9).
3. Install sealing ring (7) on cover (1).
4. Install retainer (12) on inlet exhaust valve (11) and insert
both in the body (10).
5. Install spring (13) in the body (10).
6. Install exhaust cover assembly (16) in the body (10).
Depress and hold the exhaust cover assembly in the
body.
7. Install retaining ring (17) in the body (10). Make certain
the retaining ring is completely seated in the groove in
the body.
8. Install piston (9) in body (10).
9. Install o-ring (5) on double check cover (6), install spring
(2), guide (3) and double check diaphragm (4) in cover
(1). Install cover (1) and torque torx head screws to
80-100 in. lbs.
10. Referring to the marks made during disassembly, install
cover (1).
11. Install the mounting bracket (not shown) on the cover
(1).
12. Install the four cap screws in the cover (1) and torque to
80-100 inch pounds.
13. Test the valve as outlined in the Operational and Leakage
Test section before returning the valve to service.
INSTALLATION
1. Clean air lines.
2. Inspect all lines and/or hoses for damage and replace
as necessary.
3. Install valve and tighten mounting bolts.
4. Connect air lines to valve (plug any unused ports).
5. Test valve as outlined in Operational and Leakage Tests.
OPERATIONAL AND LEAKAGE TEST
1. Chock the wheels, fully charge air brake system and
adjust the brakes.
2. Make several brake applications and check for prompt
application and release at each wheel.
3. Check for inlet valve and o-ring leakage. Make this check
with the service brakes released. Coat the exhaust port
and the area around the retaining ring with a soap solution;
a 1” bubble in 3 seconds leakage is permitted.
4. Check for exhaust valve leakage. Make this check with
the service brakes fully applied. Coat the outside of
the valve where the cover joins the body to check for
seal ring leakage; no leakage is permitted.
If the valves do not function as described above, or if
leakage is excessive, it is recommended that the valves
be replaced with new or remanufactured units or repaired
with genuine Bendix parts, available at any authorized Bendix
parts outlet.
GENERAL SAFETY GUIDELINES