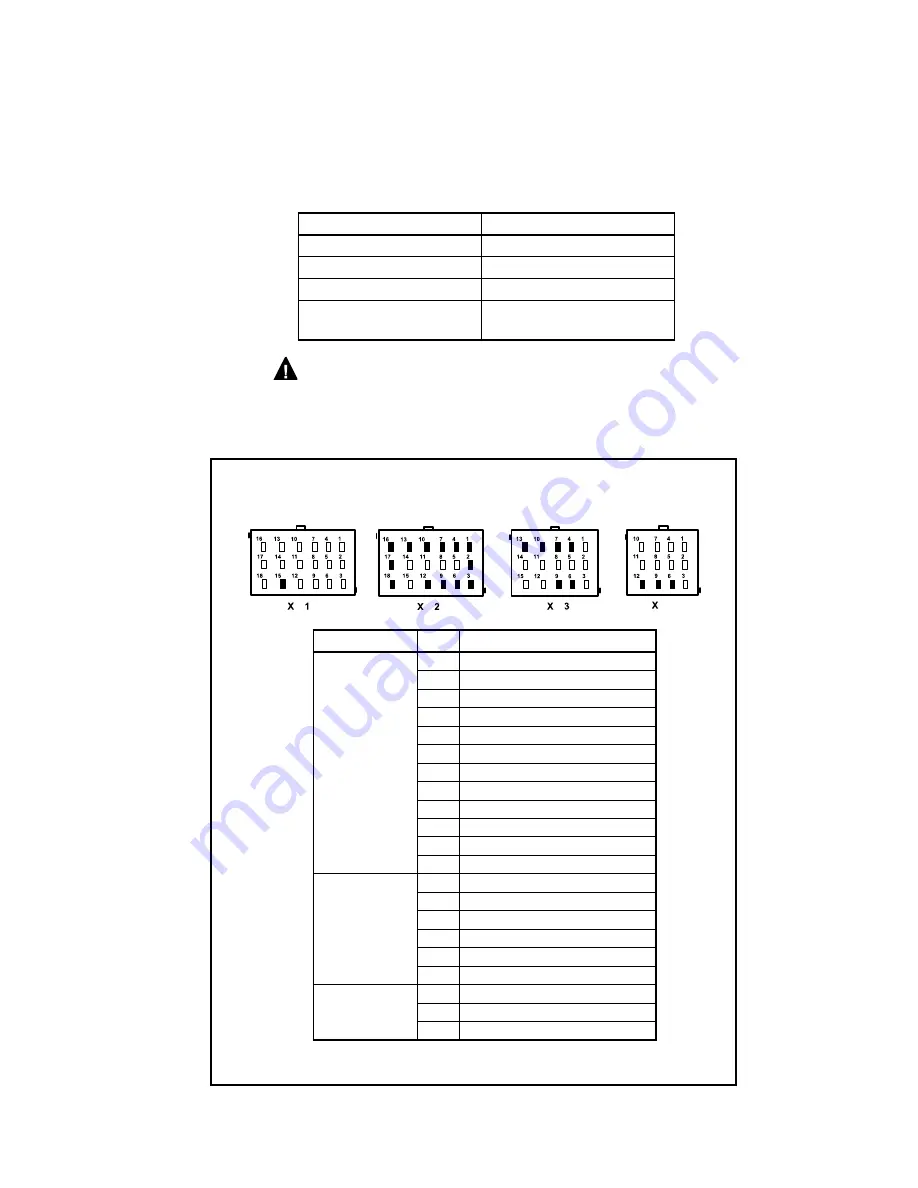
31
Pressure Modulator Valve Repair Tests:
1. Take all measurements at ECU harness connector pins in
order to check wire harness and PMV. Probe the connector
carefully so that the terminals are not damaged.
2. Pressure modulator resistance should read:
Location
Measurement
Release to Common
4.9 to 5.5 Ohms
Hold to Common
4.9 to 5.5 Ohms
Release to Hold
9.8 to 11.0 Ohms
Release, Hold, Common to
Voltage or Ground
Open Circuit (no continuity)
CAUTION
:
When troubleshooting modulator trouble
codes, check inactive trouble codes and event history for over-
voltage or excessive noise trouble codes. If one of these is
found, troubleshoot these trouble codes first before the PMV.
Cab-mount ECU: Looking into
wire harness connector
4
Connector
Pin PMV Location
X2
18 Way
1
Left Steer Axle Hold
2
Left Steer Axle Release
3
Left Steer Axle Common
4
Right Steer Axle Hold
6
Right Steer Axle Common
7
Right Steer Axle Release
9
Right Drive Axle Common
10 Right Drive Axle Hold
13 Right Drive Axle Release
12 Left Drive Axle Common
16 Left Drive Axle Hold
17 Left Drive Axle Release
X3
15 Way
(if ECU is
configured for
6 modulators)
4
Left Additional Axle Hold
6
Left Additional Axle Common
7
Left Additional Axle Release
9
Right Additional Axle Common
10 Right Additional Axle Hold
13 Right Additional Axle Release
X4
12 Way
6
Trailer PMV Hold
9
Trailer PMV Release
12 Trailer PMV Common