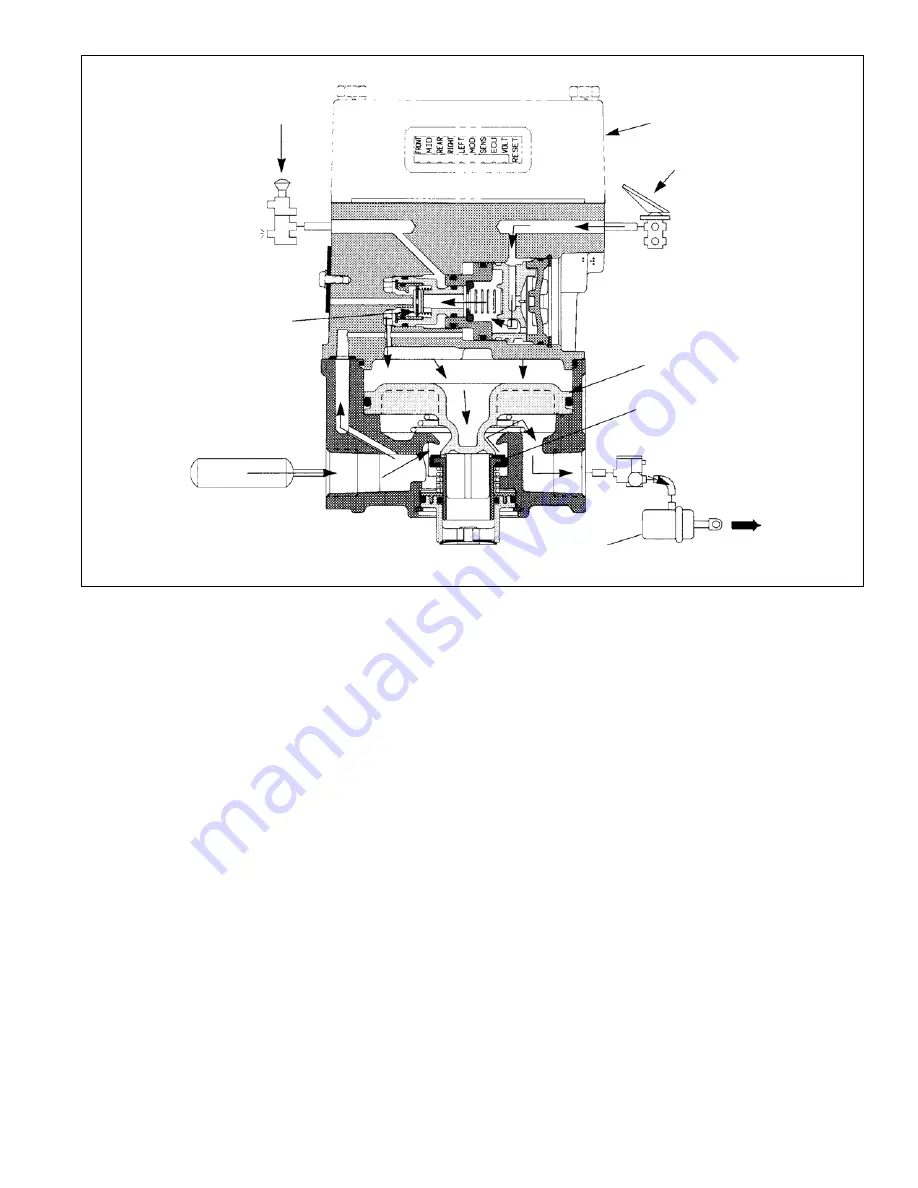
3
FIGURE 3 - TRACTOR SERVICE BRAKES APPLYING - TRACTOR TRAILER COMBINATION
SERVICE BRAKES APPLYING - TRACTOR/TRAILER
COMBINATION
Brake application air enters the AR-2
™
valve service port
and is conducted through the service piston then through
the center of both the blend back and proportioning pistons
to the inlet and exhaust valve. Flowing around the inlet valve,
application air moves through a passage in the cover to the
top of the service relay piston. In response to air pressure,
the relay piston moves into contact with the exhaust portion
of its inlet and exhaust valve. With the exhaust passage
sealed, continued movement of the piston unseats the inlet
portion of the inlet and exhaust valve, allowing supply air
from the reservoir to flow out the AR-2
™
valve delivery ports
to the brake chambers.
SERVICE BRAKES HOLDING - TRACTOR/TRAILER
COMBINATION
The air pressure being delivered to the brake chambers is
also present beneath the relay piston.
When the air pressure above and below relay piston is
equal, the piston moves slightly allowing the inlet valve to
return to its seat. The exhaust valve remains closed. With
both the inlet and exhaust valves closed, air pressure in the
brake chambers is held stable and neither increases nor
decreases.
SERVICE BRAKES RELEASING - TRACTOR/TRAILER
COMBINATION
When the brake application is released, air from above the
relay piston, flows back through the proportioning, blend
back and service pistons to the foot brake valve and is
exhausted. As air pressure is reduced above the relay
piston, pressure beneath it lifts the piston away from the
exhaust valve and opens the exhaust passage. Air from the
service brake chambers returns to the AR-2
™
valve and flows
out the open exhaust.
SERVICE APPLICATION - BOBTAIL TRACTOR
When the trailer supply valve (dash control with red octagonal
button) is activated to disconnect the trailer, air in the AR-2
™
valve control port and trailer supply line is exhausted to
atmosphere. During bobtail tractor operation, service
application air enters the AR-2
™
valve service port and as it
passes through the blend back piston air exerts a force on
the full effective diameter of the piston. The blend back piston
remains stationary at application pressures below
approximately 80 psi because of opposing reservoir air
acting on the large diameter. Application air flowing through
the blend back piston also exerts a force on the small
diameter of the proportioning piston while simultaneously
TRAILER
SUPPLY
VALVE
INLET-OPEN
EXHAUST-CLOSED
REAR AXLE
SERVICE
CHAMBER
RELAY PISTON
SERVICE
BRAKE
VALVE
ANTILOCK
CONTROLLER
INLET-OPEN
EXHAUST-CLOSED
M-21
™
MODULATOR