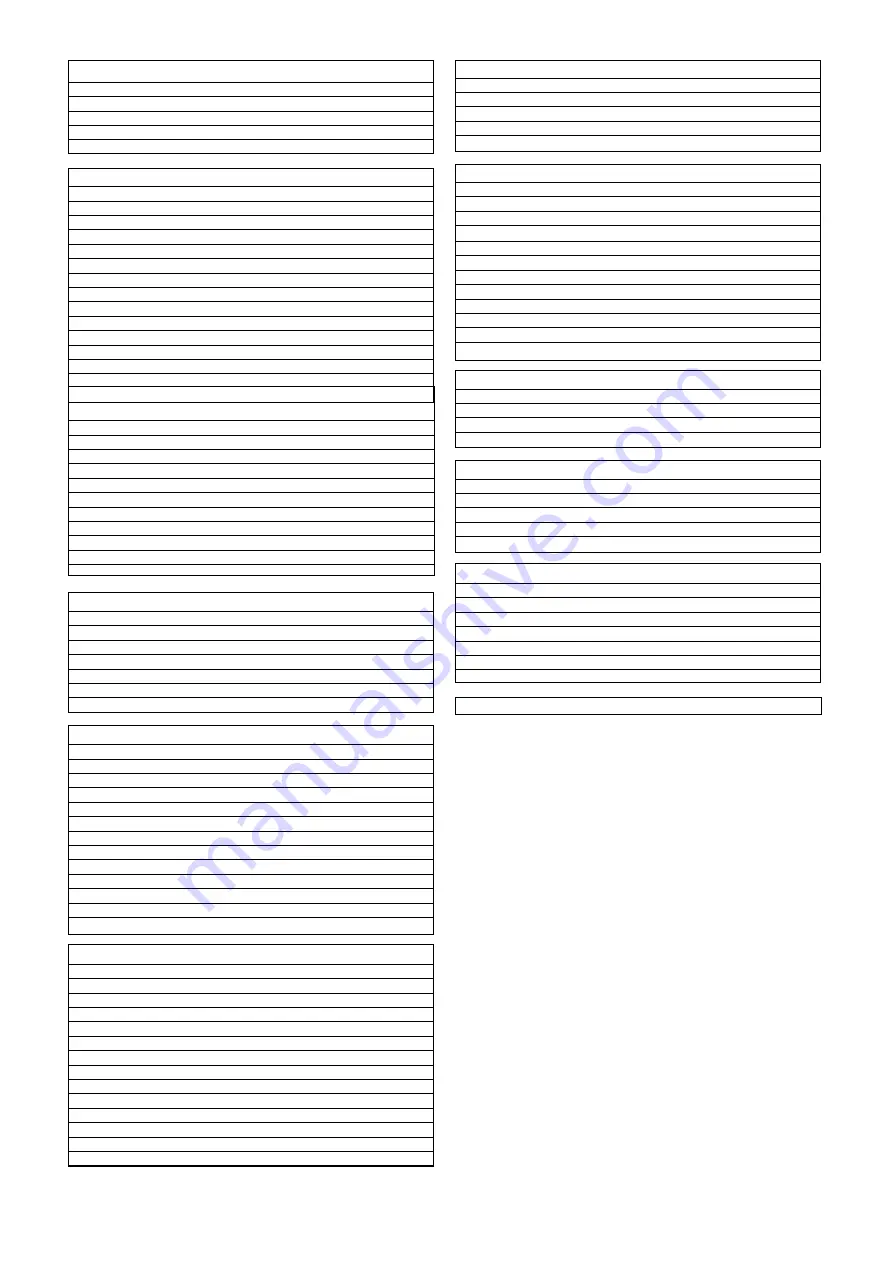
Contents
Design principles & operating sequence
Page
1.1
Principle components
3
1.2
Mode of operation (at rest)
3
1.3
Mode of operation (heating)
3
1.4
Mode of operation (Hot water)
3
1.5
Safety devices
3
Technical data
Page
2.1
Central heating
4
2.2
Domestic hot water
4
2.3
Gas pressures
4
2.4
Expansion vessel
4
2.5
Dimensions
4
2.6
Clearances
4
2.7
Connections
4
2.8
Electrical
4
2.9
Flue details (concentric)
4
2.9A Flue details (twin pipes)
4
2.9B Flue details (80/125)
4
2.10 Efficiency
4
2.11 Emissions
4
2.12 Pump duty
5
General requirements (UK)
Page
3.1
Related documents
6
3.2
Location of appliance
6
3.3
Gas supply
6
3.4
Flue system
6
3.5
Air supply
6
3.6
Water circulation
6
3.7
Electrical supply
7
3.8
Mounting on a combustible surface
7
3.9
Timber framed buildings
7
3.10 Inhibitors
7
3.11 Showers
7
Installation
Page
4.1
Delivery
8
4.2
Contents
8
4.3
Unpacking
8
4.4
Preparation for mounting the appliance
8
4.5
Fitting the flue
8
4.6
Connecting the gas & water
10
4.7
Electrical connections
11
Commissioning
Page
5.1
Gas supply installation
12
5.2
The heating system
12
5.3
Initial filling of the system
12
5.4
Initial flushing of the system
12
5.5
Pre-operation checks
12
5.6
Initial lighting
12
5.7
Checking gas pressure & combustion analysis
12
5.8
Final flushing of the heating system
13
5.9
Setting the boiler operating temperature
13
5.10 Setting the system design pressure
13
5.11 Regulating the central heating system
13
5.12 Final checks
13
5.13 Instructing the user
13
Servicing
Page
6.1
General
14
6.2
Routine annual servicing
14
6.3
Replacement of components
14
6.4
Component removal procedure
14
6.5
Pump assembly
14
6.6
Safety valve
15
6.7
Lower automatic air release valves
15
6.8
Water pressure switch
15
6.9
Primary thermistor
15
6.10 Return thermistor
15
6.11 Printed circuit board
15
6.12 Gas valve
15
6.13 Electrodes and condense sensor
16
6.14 Flue fan & mixer
16
6.15 Burner
16
6.16 Main heat exchanger
16
6.17 Automatic by-pass
17
6.18 Expansion vessel
17
6.19 Condense trap removal
17
6.20 Flue collector removal
17
Checks, adjustments and fault finding
Page
7.1
Checking appliance operation
19
7.2
Appliance modes of operation
19
7.3
Appliance fan speed
20
7.4
Checking the CO
2
& adjusting the valve
20
7.5
Combustion analysis test
21
7.6
Checking the expansion vessel
21
7.7
External faults
21
7.8
Electrical checks
21
7.9
Fault finding
22
7.10 Component values & characteristics
22
7.11 Boiler configuration
22
7.12 Final fault codes
22
Wiring diagrams
Page
8.1
External wiring
23
8.2
Typical control applications
23
8.3
Other devices
23
8.4
Twin-channel programmer
23
Exploded diagrams
Page
9.1
Table 1
25
9.2
Table 2
26
9.3
Table 3
27
9.4
Table 4
28
9.5
Table 5
29
L.P.G. instructions
Page
10.1 Related documents
30
10.2 Technical data
30
10.3 Converting the appliance gas type
30
10.4 Gas supply
30
10.5 Gas supply installation
30
10.6 Adjusting the gas valve
30
10.7 Appliance fan speed
31
Benchmark
32-33