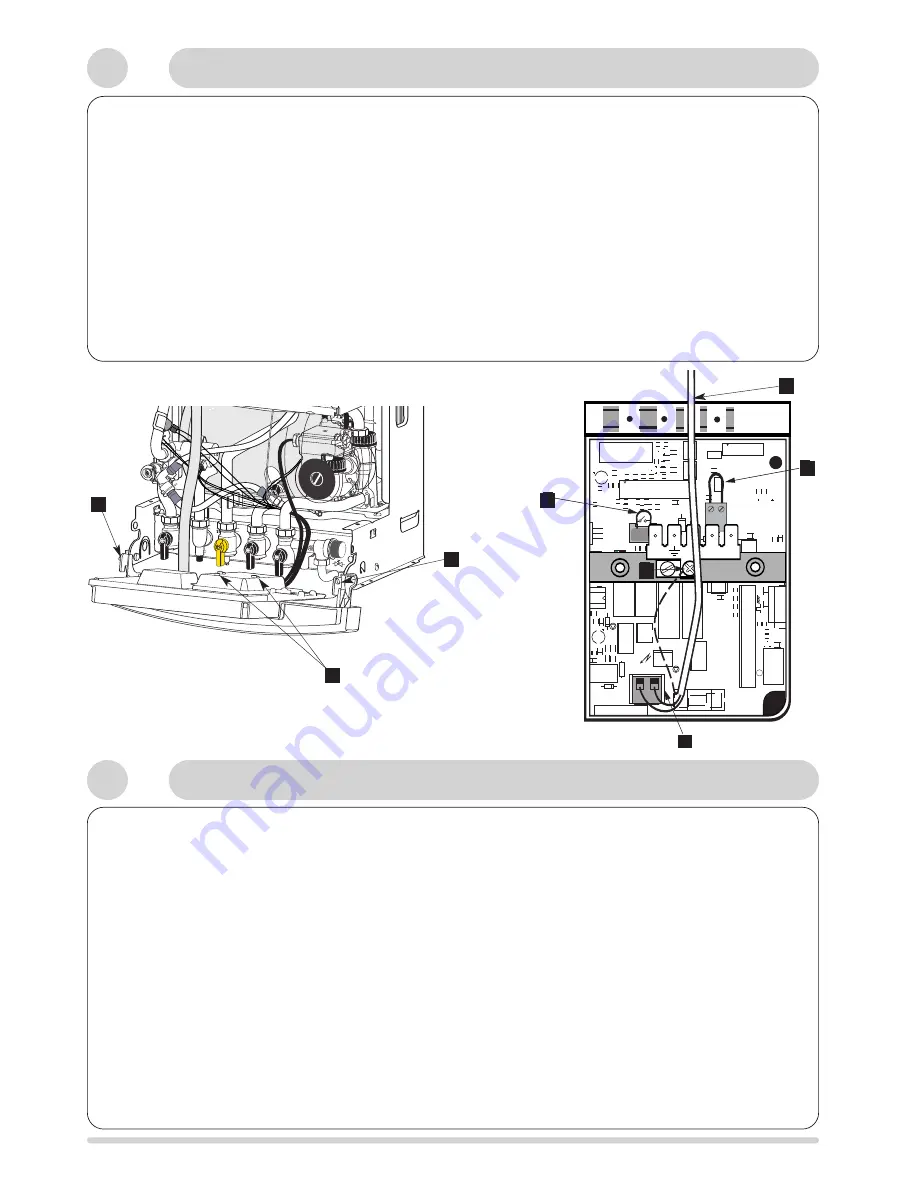
10
Making the Electrical Connections
Hinge down the electrical box to gain access to the electrical connections. Push in the tabs P (Fig. 13) on either side of the
boiler and pivot the box forward. Undo the two retaining screws V, remove the cover and remove the cable clamp C (Fig. 14).
Connect the live and neutral wires to the multipin plug leaving sufficient earth wire to connect to the earthing point T (Fig. 14).
Note: The connections should be made so that should the lead be pulled from its anchorage, the current carrying wires
become taut before the earth wire.
If using a room thermostat or other external control, they can be connected in place of the link S on the multipin plug (see Fig.
14).
Note: Use only controls designed for voltage free switching or a 24V supply. Do not connect to a 230V supply.
Connect the multipin plug into the socket on the printed circuit board. Secure the cable using the cable clamp and
replace the cover.
NB: The room thermostat options setting can be made before replacing the electrical box cover J1 (Fig.
14).
All necessary settings for room thermostat operations are described in Section 9 ADJUSTMENTS AND SETTINGS.
T
R
C
O
M
R
E
P
8
M
/A
VITESSE
1
1
1
1
1
1
BUS
1
CALYDRA
OFF ON
11
12
2
1.23
OFF ON
11
12
1
SW2
PROG
SW1
TA
1
T2A
1
MCD
1
230V
MOTEUR
RL6
R
13
3
C
28
T15
R
36
R
35
C
80
C79
T1
6
R
34
T12
T11
R107
R
33
R
13
0
R129
D43
U9
Z7A
R
13
2
R16
R15
R14
C84
C
83
R
6a
Z4A
C78
R
L1
3
C73
Z6
R7a
Z7
Z4
D46
T10
T9
RL8
R
L7
A
RL7
RL10
R
L2
A
R
L2
RL9
R
11
9
R
11
8
R113
R
9
R
8
R7
R
6
R
31
R
32
R
29
R27
R
25
R24
R23
R19
R
18
R
17
R
14
0
R137
TH
4
R13
R12
R1
1
R
11
5
C82
C
81
T14
T13
R136
TH3
U
11
R64
R10
R63
R59
R
12
8
R112
J9
J6
J7
J4
J3
J2
J1
F1
D
5
D31
D
30
D
32
D42
D41
D40
D35
D
36
A
D36
D
17
D16
D
15
D14
J1
1
C34
J5
C
52
C51
C75
C74
C
31
C
38
C27
C26
C25
C1
J12
U
12
+5
V
J
T
S
J 1
Fig. 14
6
J
T
C
S
7
Pre-commissioning
Ensure that the system has been adequately flushed.
Purge gas supply of air and test for soundness.
Carry out final electrical tests to ensure the correct polarity and
earthing continuity.
DHW
Open the main cold feed valve 43.
Open all hot taps to purge the DHW system.
Check for water soundness.
Check flow rate at the bath tap is set correctly (see technical data).
Central Heating
Open the flow and return valves on the boiler 40 and 44 (Fig. 15)
Open the automatic air vent 18 (Fig. 2)
Fill the system and vent radiators.
Set the system pressure and remove the filling loop.
Check for leaks.
Manually check pump is free to turn.
Switch on electrical supply.
Press on Central Heating switch 29 (Fig. 3) to switch on the heating
mode.
Press the +
key
32 (Fig. 3) to set the heating temperature to
maximum.
Allow the pump to run for several minutes.
Isolate the electrical supply.
Drain boiler and check water filter for installation debris.
Replace filter and recharge system.
Lighting the Boiler
Connect gas pressure gauge to test point 42 (Fig. 15).
Turn on the gas supply and boiler gas tap 42 (Fig. 15).
Ensure the electrical supply is on.
Ensure all the external controls are calling for heat.
Press on Central Heating switch 29 (Fig. 3) to switch on heating
mode.
Press on +
key
32 (fig 3) to set heating temperature to maximum.
The boiler will light. Allow the boiler to heat the system.
Check the inlet gas pressure (working pressure) while boiler is
operating in hot water mode. (Refer to technical data).
Check the operation of the boiler controls and safety devices. (see
separate servicing leaflet for details). Set the by-pass (refer to the
paragraph Page 11).
Re-flush the system to remove any dissolved oils and fluxes.
Recharge the system pressure and introduce any water treatment as
required.
Fig. 13
P
V
P
Electrical Connections
Commissioning and Testing