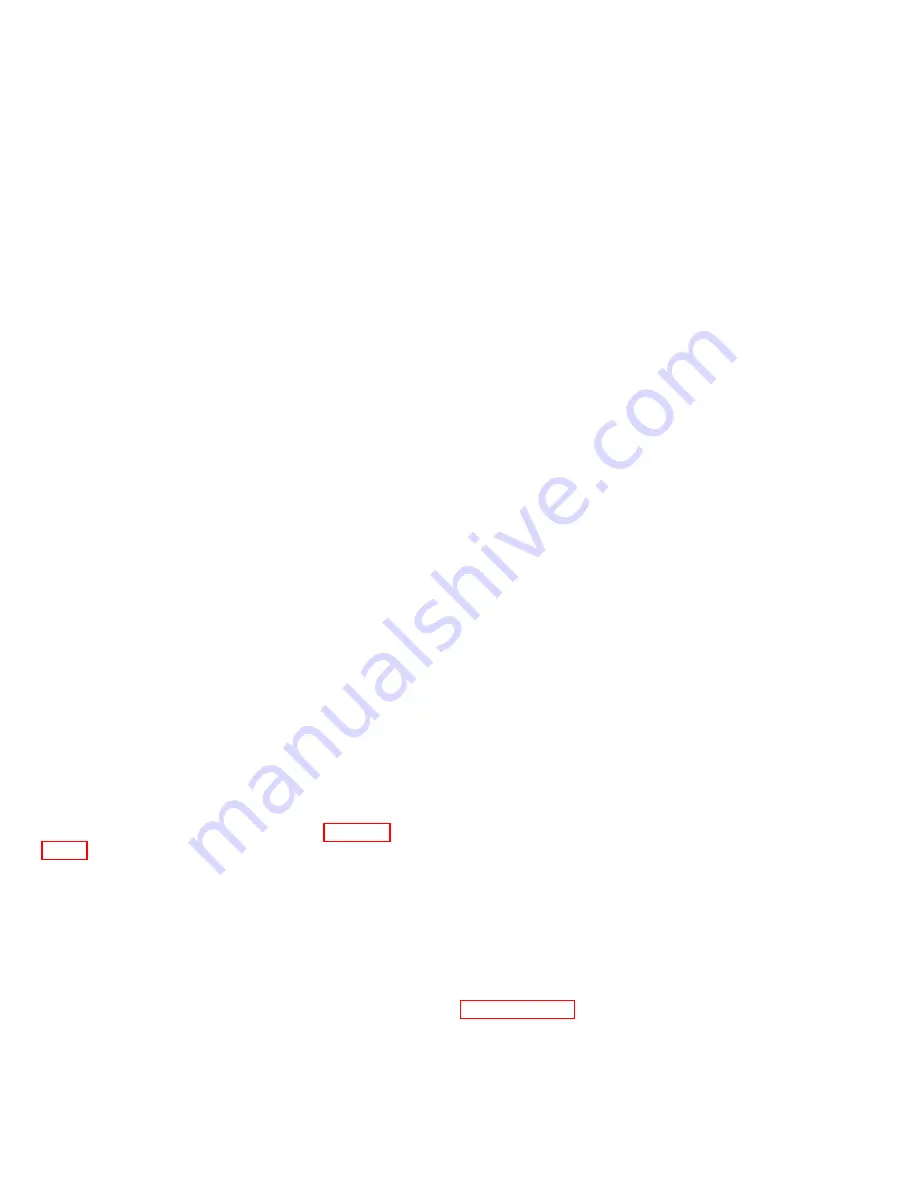
TM 55-1520-228-BD
FUEL SYSTEMS
2.
Once step 1 of this section has been
completed, locate the damage; enlarge the
wound in the tank to no more than 3
inches in diameter by using a knife or
scissors.
Remove all frayed fabric and
damaged inner lines.
3.
Abrade the inner lines or inner
surface at least 1/2 inch beyond the
enlarged hole, preferably more if con-
ditions permit.
Abrade the outer sur-
face to a minimum of 4 inches from the
enlarged area.
(NOTE:
If the fraying
fibers are too numerous, trim the fiber
with scissors.)
4.
Clean the abraded areas using towels
soaked in solvent.
5.
Cut a fabric patch 4 inches in
diameter or large enough to extend at
least 1 inch beyond the damaged area and
add a 1/2 inch hole in the center.
Soak
the patch in solvent.
6.
Mix the adhesive per option 2
instructions, step 5, and extrude into a
plastic cup. (NOTE: Adhesive can be
used between 20° through -120°, but must
be warmed to room temperature prior to
mixing and be mixed at room temperature.
Pot life of adhesive is approximately 25
minutes at 70°F.)
7.
Apply adhesive to inner liner using
finger to swab cement around the wound.
Apply adhesive to concave surface of the
rubber plug (this is the surface the
cord is attached to). Refer to Figure
12-4 for rubber plug assembly.
NOTE
Use adhesive as required, retain
some for finishing the outside of
the cell repair.
8.
Fold the rubber plug and insert it
through the hole in the cell. (NOTE:
Retain cord to prevent loss of plug in
the cell.)
9.
Pull the plug into position and
rotate it in position to smooth out the
adhesive interface.
Center the plug on
the wound.
10.
Apply a layer of adhesive 4 inches
in diameter around the wound on the out-
side and fill in the wound with adhe-
sive. (NOTE:
There must be a minimum
of a 1/2 inch bond.)
11.
Apply the solvent soaked fabric
patch to the outside surface by passing
the cord through the hole in the patch
and position the patch over the wound.
Smooth the patch into the adhesive.
12.
Pull the cord and tape to the
structure keeping a slight tension.
13.
Do not disturb the repair for a
minimum of 30 minutes, and let cure two
hours before refueling. Cut the string
and plug stem without disturbing the
repair.
14.
Tighten drain valve and install
cover plate.
15.
Refuel the aircraft.
16.
Record BDAR action taken. When
mission is complete, as soon as
practical, repair the equipment/system
using standard maintenance procedures.
OPTION 4. Two Plane Repair. Damage to
a two plane area will be repaired in the
same manner described in option 3,
except the hole should not be enlarged
to more than 1/2 X 2-1/2 inches.
OPTION 5. Three Plane Repair. Damage
to a three plane area will be repaired
in the same manner as described in
option 3, except the hole should not be
enlarged to more than 1/2 X 2-1/2 inches
and the rubber plug will be cut as shown
This will allow the
plug to assume the contour of the tank
when pulled into place.
12-8
Summary of Contents for OH-58 C
Page 8: ......
Page 10: ......
Page 20: ......
Page 32: ......
Page 36: ...TM 55 1520 228 BD ASSESSING BATTLEFIELD DAMAGE Table 2 2 General Assessment Cont 2 4...
Page 37: ...TM 55 1520 228 BD ASSESSING BATTLEFIELD DAMAGE Table 2 2 General Assessment Cont 2 5...
Page 38: ...TM 55 1520 228 BD ASSESSING BATTLEFIELD DAMAGE Table 2 2 General Assessment Cont 2 6...
Page 39: ...Table 2 2 General Assessment Cont TM 55 1520 228 BD ASSESSING BATTLEFIELD DAMAGE 2 7...
Page 40: ...I 2 8 TM 55 1520 228 BD ASSESSING BATTLEFIED DAMAGE Table 2 2 General Assessment Cont...
Page 42: ......
Page 44: ......
Page 46: ...TM 55 1520 228 BD AIRFRAME 4 2 Table 4 1 Aircraft Structure Damage Assessment Prodecures...
Page 47: ...TM 55 1520 228 BD AIRFRAME Figure 4 1 Aircraft Sections 4 3...
Page 50: ...TM 55 1520 228 BD AIRFRAME Figure 4 2 DA Form 2404 4 6...
Page 52: ...TM 55 1520 228 BD AIRFRAME Figure 4 3 Evaluating Damage to Angles Channels and Z Angles 4 8...
Page 53: ...TM 55 1520 228 BD AIRFRAME Figure 4 4 Damaged Cross Section 4 9...
Page 55: ...TM 55 1520 228 BD AIRFRAME Figure 4 6 Measuring Damage in Webs and Panels 4 11...
Page 57: ...TM 55 1520 228 BD AIRFRAME Figure 4 7 Measuring Damage in Honeycomb Sandwich Panels 4 13...
Page 61: ...TM 55 1520 228 BD AIRFRAME Figure 4 8 OH 58 Helicopter 4 17...
Page 63: ...TM 55 1520 228 BD AIRFRAME Figure 4 10 Cockpit 4 19...
Page 64: ...TM 55 1520 228 BD AIRFRAME Figure 4 11 Fuselage Pylon Support Structure Sheet 1 of 5 4 20...
Page 65: ...TM 55 1520 228 BD AIRFRAME Figure 4 11 Fuselage Pylon Support Structure Sheet 2 of 5 4 21...
Page 66: ...TM 55 1520 228 BD AIRFRAME Figure 4 11 Fuselage Pylon Support Structure Sheet 3 of 5 4 22...
Page 68: ...TM 55 1520 228 BD AIRFRAME Figure 4 11 Fuselage Pylon Support Structure Sheet 5 of 5 4 24...
Page 69: ...TM 55 1520 228 BD AIRFRAME Figure 4 12 Upper and Lower Shell Structure 4 25...
Page 70: ...TM 55 1520 228 BD AIRFRAME Figure 4 13 Aft Fuselage Structure 4 26...
Page 71: ...TM 55 1520 228 BD AIRFRAME Figure 4 14 Tail Boom 4 27...
Page 72: ...TM 55 1520 228 BD AIRFRAME Figure 4 15 Cowling and Firewalls 4 28...
Page 94: ...4 50 Table 4 8 Metal Substitution Chart TM 55 1520 228 BD AIRFRAME...
Page 96: ...TM 55 1520 228 BD AIRFRAME Figure 4 16 Typical Former Repair Sheet 1 of 2 4 52...
Page 97: ...TM 55 1520 228 BD AIRFRAME Figure 4 16 Typical Former Repair Sheet 2 of 2 4 53...
Page 100: ...TM 55 1520 228 BD AIRFRAME Figure 4 19 Typical Patch Plate Repair 4 56...
Page 102: ...TM 55 1520 228 BD AIRFRAME Figure 4 20 Expedient Cap Longeron Repair 4 58...
Page 104: ...TM 55 1520 228 BD AIRFRAME Figure 4 21 Repair of Damaged Bulkhead Flange 4 60...
Page 105: ...TM 55 1520 228 BD AIRFRAME Figure 4 22 Typical Combination Repair Sheet 1 of 2 4 61...
Page 106: ...TM 55 1520 228 BD AIRFRAME Figure 4 22 Typical Combination Repair Sheet 2 of 2 4 62...
Page 113: ...TM 55 1520 228 BD AIRFRAME Figure 4 29 Fracture Lacing With Safety Wire 4 69...
Page 117: ...TM 55 1520 228 BD ALIGHTING GEAR Table 5 1 Assessment Procedure Logic 5 3...
Page 119: ...TM 55 1520 228 BD ALIGHTING GEAR Figure 5 3 Skid Repair Figure 5 4 Clamp Repair 5 5...
Page 120: ...TM 55 1520 228 BD ALIGHTING GEAR Figure 5 5 Fabricated Clamp 5 6...
Page 122: ...TM 55 1520 228 BD POWER PLANT Figure 6 1 T63 Series Engine 6 2...
Page 123: ...POWER PLANT Table 6 1 Engine BDAR Assessment Logic 6 3...
Page 127: ...TM 55 1520 228 BD POWER PLANT Figure 6 3 Double Check Valve System Possible Alternatives 6 7...
Page 136: ...TM 55 1520 228 BD ROTORS Table 7 1 Assessment Procedures 7 4...
Page 137: ...TM 55 1520 228 BD ROTORS Figure 7 3 Rotor Blades Damage Sensitive Areas 7 5...
Page 139: ...TM 55 1520 228 BD ROTORS Figure 7 4 Rotor Blade Repair Application of Tape 7 7...
Page 143: ...TM 55 1520 228 BD DRIVE TRAIN SYSTEM 8 3 Figure 8 1 Drive Train System Sheet 2 of 4...
Page 144: ...TM 55 1520 228 BD DRIVE TRAIN SYSTEM Figure 8 1 Drive Train System Sheet 3 of 4 8 4...
Page 145: ...TM 55 1520 228 BD DRIVE TRAIN SYSTEM Figure 8 1 Drive Train System Sheet 4 of 4 8 5...
Page 149: ...TM 55 1520 228 BD DRIVE TRAIN SYSTEM Figure 8 3 Flex Duct Repair Sheet 1 of 2 8 9...
Page 150: ...TM 55 1520 228 BD DRIVE TRAIN SYSTEM Figure 8 3 Flex Duct Repair Sheet 2 of 2 8 10...
Page 156: ...TM 55 1520 228 BD HYDRAULIC Table 9 1 Assessment Logic Figure 9 3 Two Part Fitting 9 4...
Page 157: ...TM 55 1520 228 BD HYDRAULIC Figure 9 4 Four Part Fitting Figure 9 5 Using Tube Cutter 9 5...
Page 170: ......
Page 172: ......
Page 180: ...TM 55 1520 228 BD ELECTRICAL AND AVIONICS SYSTEM Figure 11 2 Crimp Splice 11 8...
Page 192: ...TM 55 1520 228 BD ELECTRICAL AND AVIONICS SYSTEM Figure 11 15 Shielded Cable Repair 11 20...
Page 208: ...TM 55 1520 228 BD ELECTRICAL AND AVIONICS SYSTEM Figure 11 35 Circuit Breakers 11 36...
Page 219: ...TM 55 1520 228 BD ELECTRICAL AND AVIONICS SYSTEM Figure 11 45 Preparation of Coax 11 47...
Page 222: ......
Page 225: ...TM 55 1520 228 BD FUEL SYSTEMS Table 12 1 Fuel System Assessment Procedures 12 3...
Page 227: ...TM 55 1520 228 BD FUEL SYSTEMS Figure 12 2 Emergency Mechanical Clamp Repair 12 5...
Page 232: ......
Page 234: ...Figure 13 1 OH 58 Flight Controls Schematic 13 2 TM 55 1520 228 BD FLIGHT CONTROLS SYSTEM...
Page 237: ...TM 55 1520 228 BD FLIGHT CONTROLS SYSTEM Figure 13 2 Collective Flight Control 13 5...
Page 238: ...TM 55 1520 228 BD FLIGHT CONTROLS SYSTEM Figure 13 3 Cyclic Flight Control 13 6...
Page 239: ...TM 55 1520 228 BD FLIGHT CONTROLS SYSTEM Figure 13 4 Flight Control Actuators 13 7...
Page 248: ...TM 55 1520 228 BD UTILITY SYSTEMS Figure 14 1 Engine De Ice System 14 2...
Page 255: ...TM 55 1520 228 BD ENVIRONMENTAL CONTROL SYSTEM Table 15 1 Assessment Procedures 15 7...
Page 258: ...TM 55 1520 228 BD ENVIRONMENTAL CONTROL SYSTEM Figure 15 6 Bleed Air Line Installation 15 10...
Page 260: ......
Page 262: ......
Page 264: ......
Page 266: ......
Page 284: ......
Page 288: ...TM 55 1520 228 BD APPENDIX F Figure F 1 Intercom System Sheet 1 of 2 F 2...
Page 298: ...TM 55 1520 228 BD APPENDIX F Figure F 6 Direction Finder Set AN ARN 89 Sheet 1 of 2 F 12...
Page 300: ...TM 55 1520 228 BD APPENDIX F Figure F 7 Radio Receiving Set AN ARN 123 V 1 Sheet 1 of 2 F 14...
Page 302: ...TM 55 1520 228 BD APPENDIX F Figure F 8 Radar Altimeter System AN APN 209 Sheet 1 of 2 F 16...
Page 314: ......
Page 324: ......
Page 326: ......
Page 332: ...P I N 0 6 6 6 3 5 0 0 0...