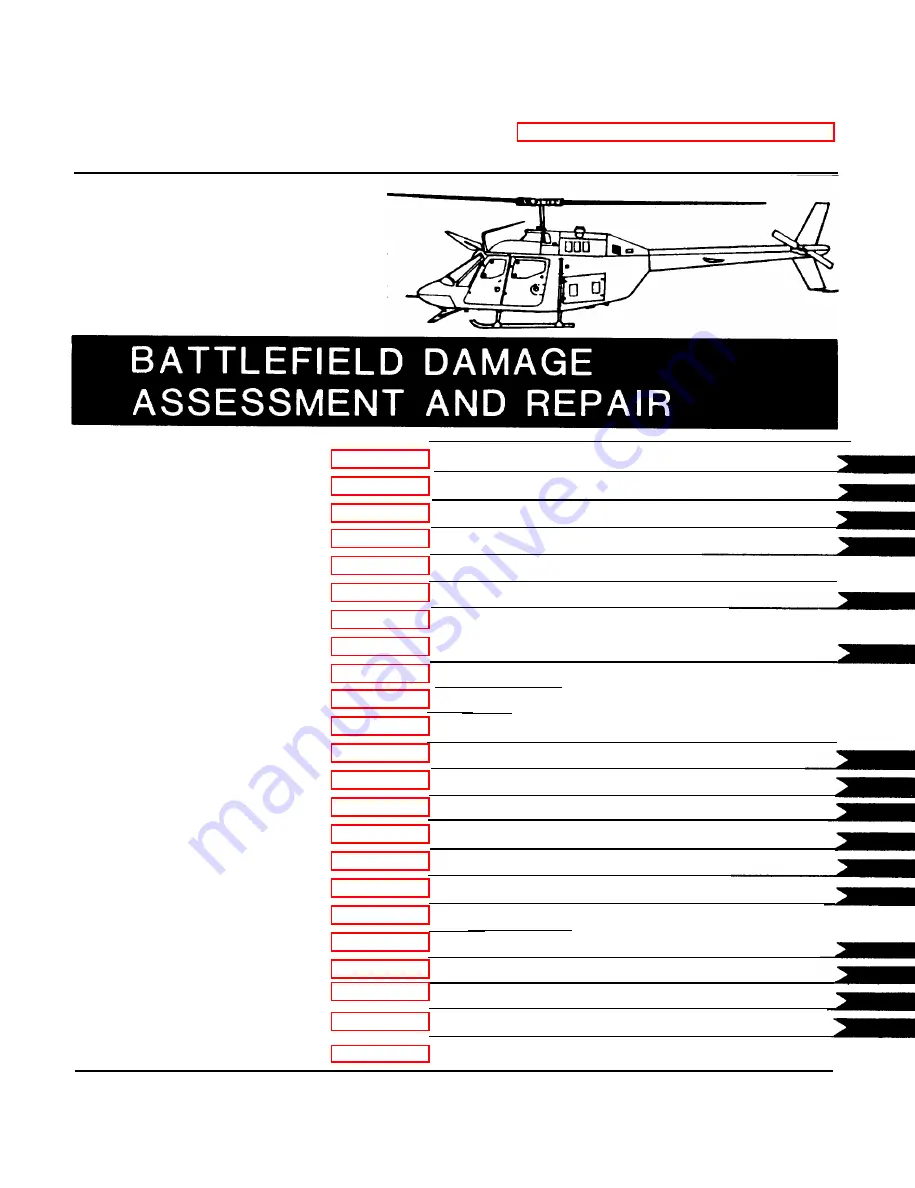
T M 5 5 - 1 5 2 0 - 2 2 8 - B D
TECHNICAL MANUAL
OPERATORS, AVIATION UNIT,
AND AVIATION
I N T E R M E D I A T E M A I N T E N A N C E
F O R
H E L l C O P T E R ,
O B S E R V A T I O N
O H - 5 8 A & O H - 5 8 C
ITEM NSN
INSIDE FRONT COVER
This publication supersedes
TM 55-1520-228-BD dated
17 August 1990.
CHAPTER 1. GENERAL INFORMATION
CHAPTER 2. ASSESSING BATTLEFIELD DAMAGE
CHAPTER 10: INSTRUMENT SYSTEMS
CHAPTER 15. ENVIRONMENTAL CONTROL SYSTEM
CHAPTER 17. EMERGENCY EQUIPMENT
APPENDIX B. SPECIAL OR FABRICATED TOOLS
APPENDIX C. EXPENDABLE/DURABLE SUPPLIES
&
MATERIALS
APPENDIX D. SUBSTITUTE MATERIALS/PARTS
APPENDIX E. BDAR TRAINING PROCEDURES
H E A D Q U A R T E R S , D E P A R T M E N T O F T H E A R M Y
4 J a n u a r y 1 9 9 1
Summary of Contents for OH-58 C
Page 8: ......
Page 10: ......
Page 20: ......
Page 32: ......
Page 36: ...TM 55 1520 228 BD ASSESSING BATTLEFIELD DAMAGE Table 2 2 General Assessment Cont 2 4...
Page 37: ...TM 55 1520 228 BD ASSESSING BATTLEFIELD DAMAGE Table 2 2 General Assessment Cont 2 5...
Page 38: ...TM 55 1520 228 BD ASSESSING BATTLEFIELD DAMAGE Table 2 2 General Assessment Cont 2 6...
Page 39: ...Table 2 2 General Assessment Cont TM 55 1520 228 BD ASSESSING BATTLEFIELD DAMAGE 2 7...
Page 40: ...I 2 8 TM 55 1520 228 BD ASSESSING BATTLEFIED DAMAGE Table 2 2 General Assessment Cont...
Page 42: ......
Page 44: ......
Page 46: ...TM 55 1520 228 BD AIRFRAME 4 2 Table 4 1 Aircraft Structure Damage Assessment Prodecures...
Page 47: ...TM 55 1520 228 BD AIRFRAME Figure 4 1 Aircraft Sections 4 3...
Page 50: ...TM 55 1520 228 BD AIRFRAME Figure 4 2 DA Form 2404 4 6...
Page 52: ...TM 55 1520 228 BD AIRFRAME Figure 4 3 Evaluating Damage to Angles Channels and Z Angles 4 8...
Page 53: ...TM 55 1520 228 BD AIRFRAME Figure 4 4 Damaged Cross Section 4 9...
Page 55: ...TM 55 1520 228 BD AIRFRAME Figure 4 6 Measuring Damage in Webs and Panels 4 11...
Page 57: ...TM 55 1520 228 BD AIRFRAME Figure 4 7 Measuring Damage in Honeycomb Sandwich Panels 4 13...
Page 61: ...TM 55 1520 228 BD AIRFRAME Figure 4 8 OH 58 Helicopter 4 17...
Page 63: ...TM 55 1520 228 BD AIRFRAME Figure 4 10 Cockpit 4 19...
Page 64: ...TM 55 1520 228 BD AIRFRAME Figure 4 11 Fuselage Pylon Support Structure Sheet 1 of 5 4 20...
Page 65: ...TM 55 1520 228 BD AIRFRAME Figure 4 11 Fuselage Pylon Support Structure Sheet 2 of 5 4 21...
Page 66: ...TM 55 1520 228 BD AIRFRAME Figure 4 11 Fuselage Pylon Support Structure Sheet 3 of 5 4 22...
Page 68: ...TM 55 1520 228 BD AIRFRAME Figure 4 11 Fuselage Pylon Support Structure Sheet 5 of 5 4 24...
Page 69: ...TM 55 1520 228 BD AIRFRAME Figure 4 12 Upper and Lower Shell Structure 4 25...
Page 70: ...TM 55 1520 228 BD AIRFRAME Figure 4 13 Aft Fuselage Structure 4 26...
Page 71: ...TM 55 1520 228 BD AIRFRAME Figure 4 14 Tail Boom 4 27...
Page 72: ...TM 55 1520 228 BD AIRFRAME Figure 4 15 Cowling and Firewalls 4 28...
Page 94: ...4 50 Table 4 8 Metal Substitution Chart TM 55 1520 228 BD AIRFRAME...
Page 96: ...TM 55 1520 228 BD AIRFRAME Figure 4 16 Typical Former Repair Sheet 1 of 2 4 52...
Page 97: ...TM 55 1520 228 BD AIRFRAME Figure 4 16 Typical Former Repair Sheet 2 of 2 4 53...
Page 100: ...TM 55 1520 228 BD AIRFRAME Figure 4 19 Typical Patch Plate Repair 4 56...
Page 102: ...TM 55 1520 228 BD AIRFRAME Figure 4 20 Expedient Cap Longeron Repair 4 58...
Page 104: ...TM 55 1520 228 BD AIRFRAME Figure 4 21 Repair of Damaged Bulkhead Flange 4 60...
Page 105: ...TM 55 1520 228 BD AIRFRAME Figure 4 22 Typical Combination Repair Sheet 1 of 2 4 61...
Page 106: ...TM 55 1520 228 BD AIRFRAME Figure 4 22 Typical Combination Repair Sheet 2 of 2 4 62...
Page 113: ...TM 55 1520 228 BD AIRFRAME Figure 4 29 Fracture Lacing With Safety Wire 4 69...
Page 117: ...TM 55 1520 228 BD ALIGHTING GEAR Table 5 1 Assessment Procedure Logic 5 3...
Page 119: ...TM 55 1520 228 BD ALIGHTING GEAR Figure 5 3 Skid Repair Figure 5 4 Clamp Repair 5 5...
Page 120: ...TM 55 1520 228 BD ALIGHTING GEAR Figure 5 5 Fabricated Clamp 5 6...
Page 122: ...TM 55 1520 228 BD POWER PLANT Figure 6 1 T63 Series Engine 6 2...
Page 123: ...POWER PLANT Table 6 1 Engine BDAR Assessment Logic 6 3...
Page 127: ...TM 55 1520 228 BD POWER PLANT Figure 6 3 Double Check Valve System Possible Alternatives 6 7...
Page 136: ...TM 55 1520 228 BD ROTORS Table 7 1 Assessment Procedures 7 4...
Page 137: ...TM 55 1520 228 BD ROTORS Figure 7 3 Rotor Blades Damage Sensitive Areas 7 5...
Page 139: ...TM 55 1520 228 BD ROTORS Figure 7 4 Rotor Blade Repair Application of Tape 7 7...
Page 143: ...TM 55 1520 228 BD DRIVE TRAIN SYSTEM 8 3 Figure 8 1 Drive Train System Sheet 2 of 4...
Page 144: ...TM 55 1520 228 BD DRIVE TRAIN SYSTEM Figure 8 1 Drive Train System Sheet 3 of 4 8 4...
Page 145: ...TM 55 1520 228 BD DRIVE TRAIN SYSTEM Figure 8 1 Drive Train System Sheet 4 of 4 8 5...
Page 149: ...TM 55 1520 228 BD DRIVE TRAIN SYSTEM Figure 8 3 Flex Duct Repair Sheet 1 of 2 8 9...
Page 150: ...TM 55 1520 228 BD DRIVE TRAIN SYSTEM Figure 8 3 Flex Duct Repair Sheet 2 of 2 8 10...
Page 156: ...TM 55 1520 228 BD HYDRAULIC Table 9 1 Assessment Logic Figure 9 3 Two Part Fitting 9 4...
Page 157: ...TM 55 1520 228 BD HYDRAULIC Figure 9 4 Four Part Fitting Figure 9 5 Using Tube Cutter 9 5...
Page 170: ......
Page 172: ......
Page 180: ...TM 55 1520 228 BD ELECTRICAL AND AVIONICS SYSTEM Figure 11 2 Crimp Splice 11 8...
Page 192: ...TM 55 1520 228 BD ELECTRICAL AND AVIONICS SYSTEM Figure 11 15 Shielded Cable Repair 11 20...
Page 208: ...TM 55 1520 228 BD ELECTRICAL AND AVIONICS SYSTEM Figure 11 35 Circuit Breakers 11 36...
Page 219: ...TM 55 1520 228 BD ELECTRICAL AND AVIONICS SYSTEM Figure 11 45 Preparation of Coax 11 47...
Page 222: ......
Page 225: ...TM 55 1520 228 BD FUEL SYSTEMS Table 12 1 Fuel System Assessment Procedures 12 3...
Page 227: ...TM 55 1520 228 BD FUEL SYSTEMS Figure 12 2 Emergency Mechanical Clamp Repair 12 5...
Page 232: ......
Page 234: ...Figure 13 1 OH 58 Flight Controls Schematic 13 2 TM 55 1520 228 BD FLIGHT CONTROLS SYSTEM...
Page 237: ...TM 55 1520 228 BD FLIGHT CONTROLS SYSTEM Figure 13 2 Collective Flight Control 13 5...
Page 238: ...TM 55 1520 228 BD FLIGHT CONTROLS SYSTEM Figure 13 3 Cyclic Flight Control 13 6...
Page 239: ...TM 55 1520 228 BD FLIGHT CONTROLS SYSTEM Figure 13 4 Flight Control Actuators 13 7...
Page 248: ...TM 55 1520 228 BD UTILITY SYSTEMS Figure 14 1 Engine De Ice System 14 2...
Page 255: ...TM 55 1520 228 BD ENVIRONMENTAL CONTROL SYSTEM Table 15 1 Assessment Procedures 15 7...
Page 258: ...TM 55 1520 228 BD ENVIRONMENTAL CONTROL SYSTEM Figure 15 6 Bleed Air Line Installation 15 10...
Page 260: ......
Page 262: ......
Page 264: ......
Page 266: ......
Page 284: ......
Page 288: ...TM 55 1520 228 BD APPENDIX F Figure F 1 Intercom System Sheet 1 of 2 F 2...
Page 298: ...TM 55 1520 228 BD APPENDIX F Figure F 6 Direction Finder Set AN ARN 89 Sheet 1 of 2 F 12...
Page 300: ...TM 55 1520 228 BD APPENDIX F Figure F 7 Radio Receiving Set AN ARN 123 V 1 Sheet 1 of 2 F 14...
Page 302: ...TM 55 1520 228 BD APPENDIX F Figure F 8 Radar Altimeter System AN APN 209 Sheet 1 of 2 F 16...
Page 314: ......
Page 324: ......
Page 326: ......
Page 332: ...P I N 0 6 6 6 3 5 0 0 0...