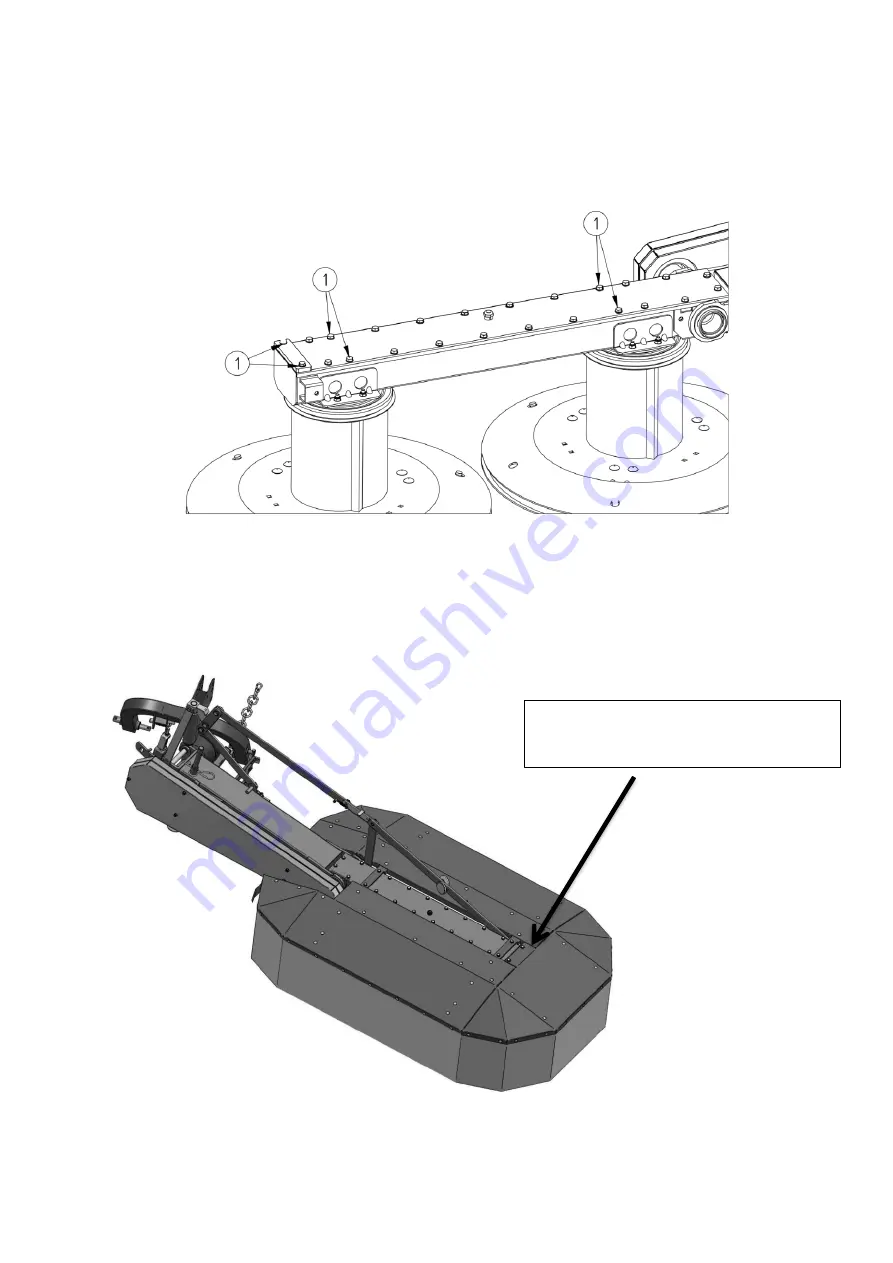
51
9) STEP X
Unscrew the bolts indicated in the following figure (Fig. 39) - cover mounting location:
10) STEP XI
Adjust the cover to the "free holes" from STEP X and fix it with the bolt elements used in STEP
X
Figure 39 Metal covers assembly
–
STEP X
Place the rear cover on the flat bar located
on the main frame cover
Summary of Contents for Tar River BDR 210
Page 33: ...33 9 2 1 Middle frame ...
Page 36: ...36 9 2 2 Hydraulic system ...
Page 39: ...39 9 2 2 Main frame ...