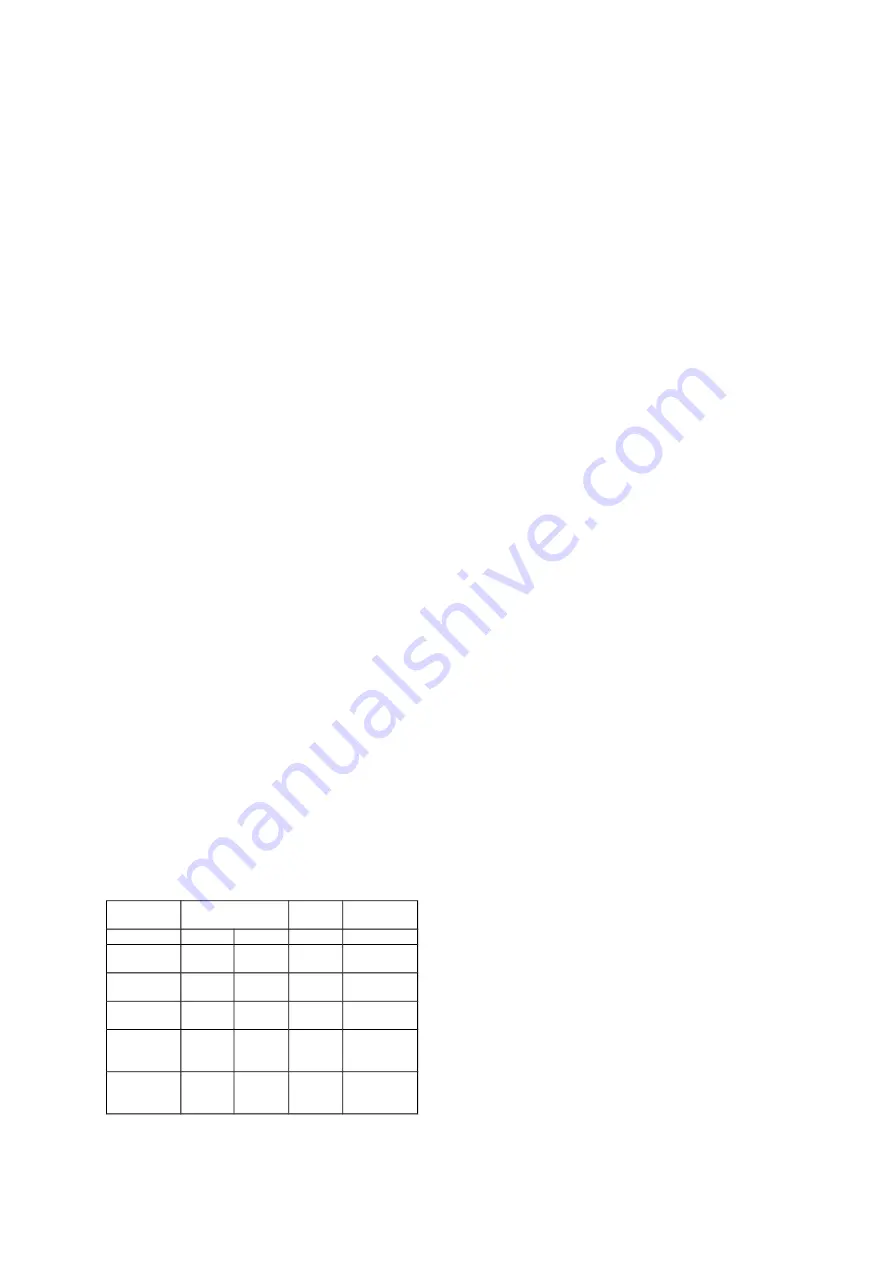
4.2.1 Power supply
Usually a BA454D batch controller is powered
from the safe area via a positive polarity 28V
300
Zener barrier which has a typical end-to-
end resistance of 340
. The BA454D
consumes a maximum current of 33mA and
requires a minimum voltage of 11V between
terminals 1 and 2. When powered from a
28V 300
Zener barrier the supply voltage in
the safe area must be between 22.2V and the
maximum working voltage of the barrier which
is usually about 26V.
CAUTION
The safety components within the batch
controller limit the voltage between terminals 1
and 2 at 15V. If the batch controller is directly
connected to a 15V or greater power supply
without a Zener barrier or equivalent series
resistor, the instrument will consume a large
current for a few seconds and then shut-down
to prevent permanent damage. To test a
BA454D batch controller in a safe area
workshop, terminals 1 & 2 should be
connected to a 24V dc power supply via a
330
resistor.
4.2.2 Pulse inputs
As shown in Figs 3 and 4 the BA454D batch
controller may be connected to a wide variety
of pulse transducers and sources in the
hazardous or safe area. Input 1 is for pulse
sources that need powering by the batch
controller such as switch contacts or a 2-wire
proximity detector. Input 2 is for voltage pulse
inputs such as the magnetic pickup in a turbine
flowmeter, or a voltage pulse output from a
flowmeter.
The following table shows the switching
thresholds for the various transducers, plus the
maximum operating frequency and the input
terminal numbers. For reliable counting the
input signal must fall below the lower switching
threshold and rise above the upper threshold.
Switching
thresholds
Freq
max
Input
terminals
Switch
100
1000
100Hz
12 & 11 +
Proximity
detector
1.2mA
2.1mA
5 kHz
12 & 11 +
Open
collector
2k
10k
5kHz
12 & 11 +
Magnetic
pickup
10mV
30mV
5kHz
16 & 15 +
Low
voltage
pulse
1V
3V
5kHz
16 & 14 +
High
voltage
pulse
3V
10V
5kHz
16 & 13 +
Note:
Only one input may be used at a time.
4.2.2.1 Switch contact input
Any mechanically activated switch contact
located in the hazardous area may be
connected directly to terminals 12 & 11
providing the switch has IP20 protection and
can withstand a 500V rms insulation test to
earth. Most magnetically activated reed relays
used in turbine flowmeters comply.
The maximum operating frequency for a switch
contact input is 100Hz.
4.2.2.2 2-wire proximity detector input
Any Ex ia certified intrinsically safe 2-wire
proximity detector complying with NAMUR
switching thresholds may be used, providing
the input safety parameters of the proximity
detector are equal to or greater than:
Ui
10.6V dc
Ii
20mA dc
Pi
50mW
If located in the same hazardous area as the
batch controller the proximity detector may be
directly connected to terminals 12 & 11
When programmed to operate with a proximity
detector, the maximum input frequency of the
BA454D batch controller is 5kHz.
4.2.2.3 Voltage pulse input
Voltage pulse sources may be connected
directly to input 2, the terminals used depend
upon the input magnitude – see the table in
section 4.2.2. All these terminals comply with
the requirements for
simple apparatus
and
they may be directly connected to any Ex ia
certified intrinsically safe voltage source within
the hazardous area. The source must be able
to withstand a 500V rms insulation test to earth
for one minute and have output parameters
equal to or less than:
Uo
28V dc
Io
100mA dc
Po
0.66W
This enables the BA454D to be connected
directly to most flowmeters incorporating a
certified intrinsically safe magnetic pickup, or a
certified intrinsically safe amplifier producing a
high level pulse output. The BA454D has
three selectable voltage switching thresholds,
for magnetic pickups, low voltage pulses and
high voltage pulses.
When programmed to operate with a voltage
pulse source, the maximum input frequency of
the BA454D batch controller is 5kHz.
9
Summary of Contents for BA454D
Page 1: ...Issue 12 29th August 2014 BA454D Intrinsically safe Field mounting Batch Controller Issue 12 ...
Page 14: ...Fig 10 Dimensions and terminal connections 14 ...
Page 17: ...17 BLANK PAGE ...
Page 18: ...18 Fig 11 System Settings Fig 11 System Settings ...
Page 23: ...23 BLANK PAGE ...
Page 24: ...24 Fig 14 Batch Settings ...
Page 29: ...29 BLANK PAGE ...
Page 30: ...30 Fig 16 Rate Settings ...
Page 38: ...38 ...
Page 39: ...39 ...
Page 40: ...Appendix 2 Information menu 40 ...
Page 43: ...43 ...
Page 44: ...44 ...
Page 45: ...45 ...
Page 46: ...46 ...
Page 47: ...47 ...
Page 48: ...48 ...
Page 49: ...49 ...