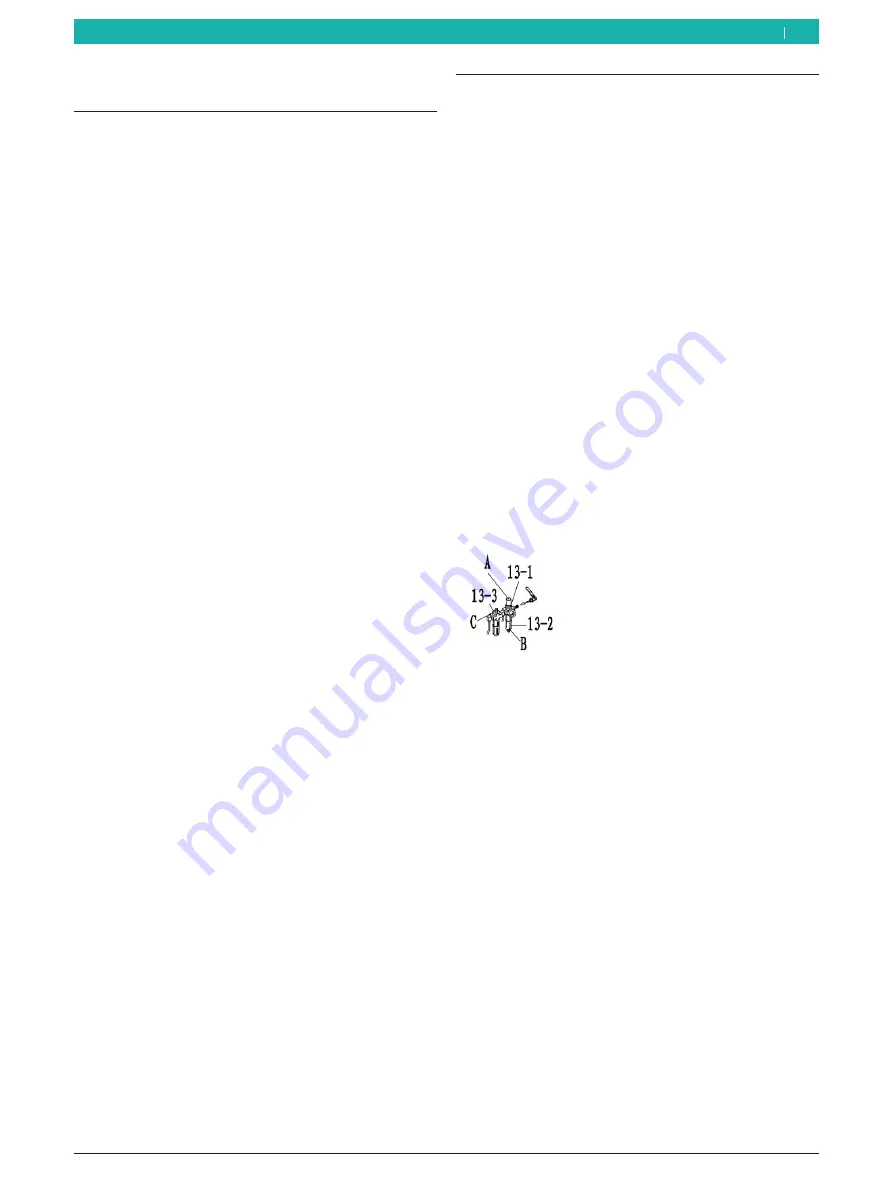
Maintenance | Start Line MS 201 | 45
en
1 695 108 073
2016-07-27
|
Bosch Automotive Service Solutions srl
9. Maintenance
9.1
Warning
!
Non-professional personnel should not perform
maintenance.
!
Before performing any maintenance, you should
switch off the air supply and power. By repeatedly
depressing the pedal, you can release the residual
air in the machine completely.
!
Perform maintenance periodically as described in
this operating manual. This is necessary to prolong
the life of the MS 201 and guarantee normal
operating conditions.
!
If maintenance is not performed periodically, the
reliability and proper operation of the MS 201
are no longer guaranteed, and the MS 201 can
be damaged. Operators and persons nearby can be
injured.
!
Defective parts must be replaced with original parts
provided by the manufacturer.
!
Removing or breaking safety devices such as the
safety valve and standard nozzles violate the safety
standards.
!
You should not modify components on the machine
without authorization.
i
Special note: The manufacture will not honor claims
arising from the use of parts provided by other
suppliers and for damage caused by removing or
breaking the safety devices.
¶
Keep the working area clean.
¶
Do not use compressed air to remove dirt from the
MS 201.
¶
Keep generation of dust in the area to a minimum.
9.2
Maintenance operations
9.2.1
Maintenance unit and bead breaking cylinder
!
Perform \the following operation at least once every
30 days.
1.
Check the oil level in the oil cup. If there is not
enough oil, remove the oil cup and replenish the
lubrication oil as shown in following figure. The oil
filled into the lubricator must be the special SAE 20
oil.
2.
Oil feeding speed regulation: Move the bead
breaking cylinder back and forward to check
whether the oil feeding speed is one drop of oil per
2 stokes of the cylinder. If not, use the bolt B to
adjust as shown in following figure.
3.
Drainage: Check the water quantity in the water cup.
Turn/press the valve at the low end of the water cup
to drain.
4.
Before operating, always run the bead breaking
cylinder back and forward while observing the
lubricator to make sure it starts feeding oil to the air
passage. After you confirm that the lubricator works
normal, you can guarantee each part of the air route
system under
perfect lubrication
.
5.
Periodically tighten the nut at the fixed equipment.
6.
Periodically fill in the lubrication oil components can
move and slide to each other.
Summary of Contents for Start Line MS 201
Page 2: ......