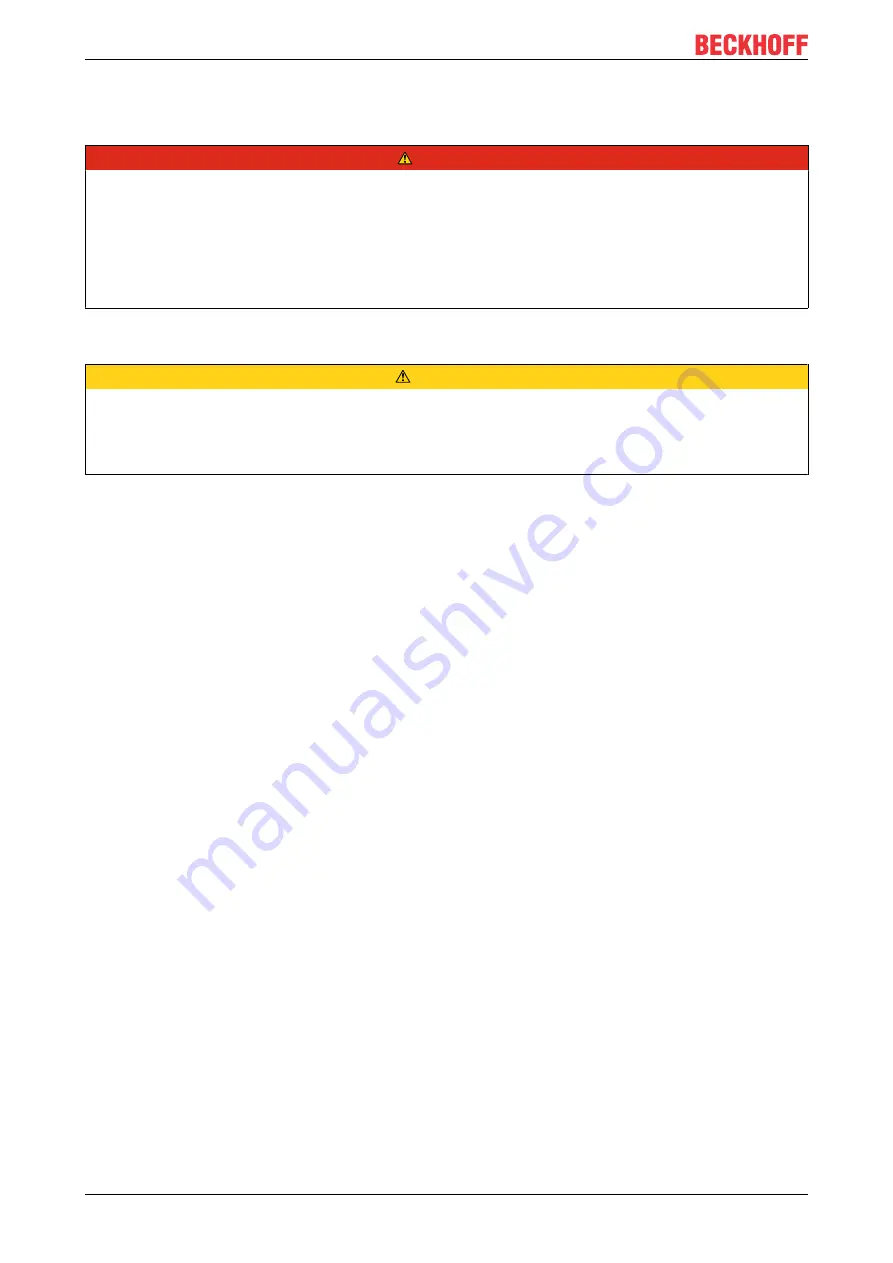
Safe Motion functions
AX8911
54
Version: 1.2.0
The safe output
SAFEOUT BRAKE Module Axis x Enable
must be set to TRUE in order to be able to vent
the built-in holding brake in the motor. If the output is set to FALSE, the internal holding brake of the motor is
applied.
DANGER
Controlling the brake
The control of the brake within the logic must always consist of the following 2 signals, which are logically
ANDed. The signal
SAFEOUT BRAKE Module Axis x Active
(input 0.3 or 0.5 respectively) and the signal
created in the safety application for controlling the brake (this is carried out automatically from the firmware
01 release).
The brake control in the current version has a switch-off delay of up to 11 ms. This will no longer be the
case in the firmware 01 release.
The brake output for the holding brake should always be switched in conjunction with the STO signal at the
standstill of the axis so that suspended or pulling loads are kept in their position in the STO state.
CAUTION
Error reaction of STO and brake
In case of error, an axis will be switched to STO. If the result of the risk and hazard analysis is that an axis
that is still in motion could lead to the endangerment of persons in the STO state, then a (safe) service
brake must be provided and activated.
If an external service brake is used, this can be controlled via safe outputs, e.g. of an EL2904.
The safety function SBC is used only for the safe control of the holding brake integrated in the motor. A
brake test must be implemented by means of the application.
7.14
Safety function SBT
The SBT (Safe Brake Test) function is for testing the function of brakes that are subject to wear. A distinction
is made here between a static and dynamic test. The static test is carried out with the brake applied and 1.3
x the maximum load moment. The dynamic test consists of the measurement of the overrun and the overrun
time when the brakes are activated after activating the STO of the axis.
If the test fails, the drive and the brake may no longer be used or activated. Following a repair and a new,
successful brake test, the drive can be put back into operation.
These functions are implemented in the AX8000 with Safe Motion function by means of an application in the
safe user program.