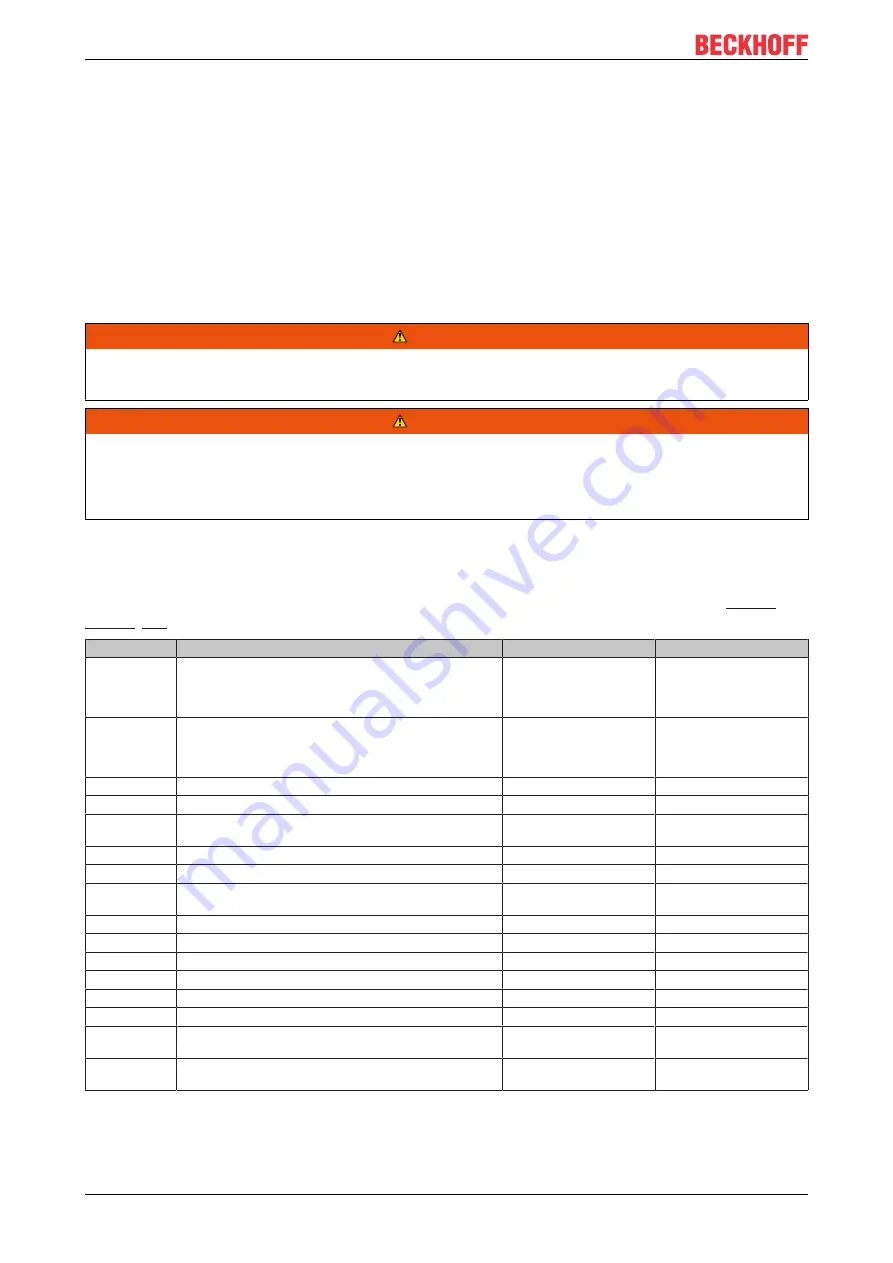
Safe Motion functions
AX8911
44
Version: 1.2.0
7.4
Basic functions
7.4.1
Signal assignment
The process data of the AX8911 supply information about the current state of the safety card and the
SafeMotion functions.
The following notes and signal assignments must be taken into account by the user and implemented
according to the user configuration.
Switch-off paths and restart lock
WARNING
STO function
For the STO function, all 4 STO signals of an axis must be switched by the safety application.
WARNING
Restart lock
After activating the STO function, the restart lock must be implemented in the safety application. If the result
of the risk and hazard analysis is that the restart must be implemented via a safe signal, then the restart
must be wired to a safe TwinSAFE signal.
Assignment of the AX8000 signals (minimum configuration)
The table below contains a list of the signals that must at least be exchanged between the AX8911 and the
AX8000. The addresses and descriptions for source and destination can be found in the chapter
.
Name
Description Axis 1
Source (SafeIn)
Destination (SafeOut)
Group-
Port_RunStop
This signal is automatically created when creating the Twin-
SAFE group and can be placed on a standard signal. If the
signals from the AX8000 are to be used, the adjacent as-
signment can be used.
22.0
GroupPort_RunStop
GroupPort_Er-
rAck
This signal is automatically created when creating the Twin-
SAFE group and can be placed on a standard signal. If the
signals from the AX8000 are to be used, the adjacent as-
signment can be used.
22.1
GroupPort_ErrAck
ErrAck_STO1
Acknowledgement of an STO module fault
22.1
0.4
ErrAck_Brake1 Acknowledgement of a brake module fault
22.1
1.5
Er-
rAck_SAFEIN1
Acknowledgement of a SafeIN module fault
22.1
2.2
ErrAck_Enc1
Acknowledgement of an encoder module fault
22.1
4.0
ErrAck_Prim1
Acknowledgement of a module fault in the primary feedback 22.1
14.0
Errack_Sec1
Acknowledgement of a module fault in the secondary feed-
back
22.1
18.0
STOerror1
Module error in the STO module for Axis 1
0.0
6.1
FSINerror1
Module error in the FSIN module for Axis 1
1.0
6.2
BrakeError1
Module error in the brake module for Axis 1
0.2
6.3
UnderRange1
Encoder Underrange Error
2.0
6.4
OverRange1
Encoder Overrange Error
2.1
6.5
EncEnable1
Encoder Enable
2.3
6.6
PrimError1
Error occurred in the primary feedback
Default OCT / Endat 2.2 (depending on active feedback)
56.0 / 56.1
6.7
SecError1
Error occurred in the secondary feedback
Default OCT / Endat 2.2 (depending on active feedback)
82.0 / 82.1
7.0