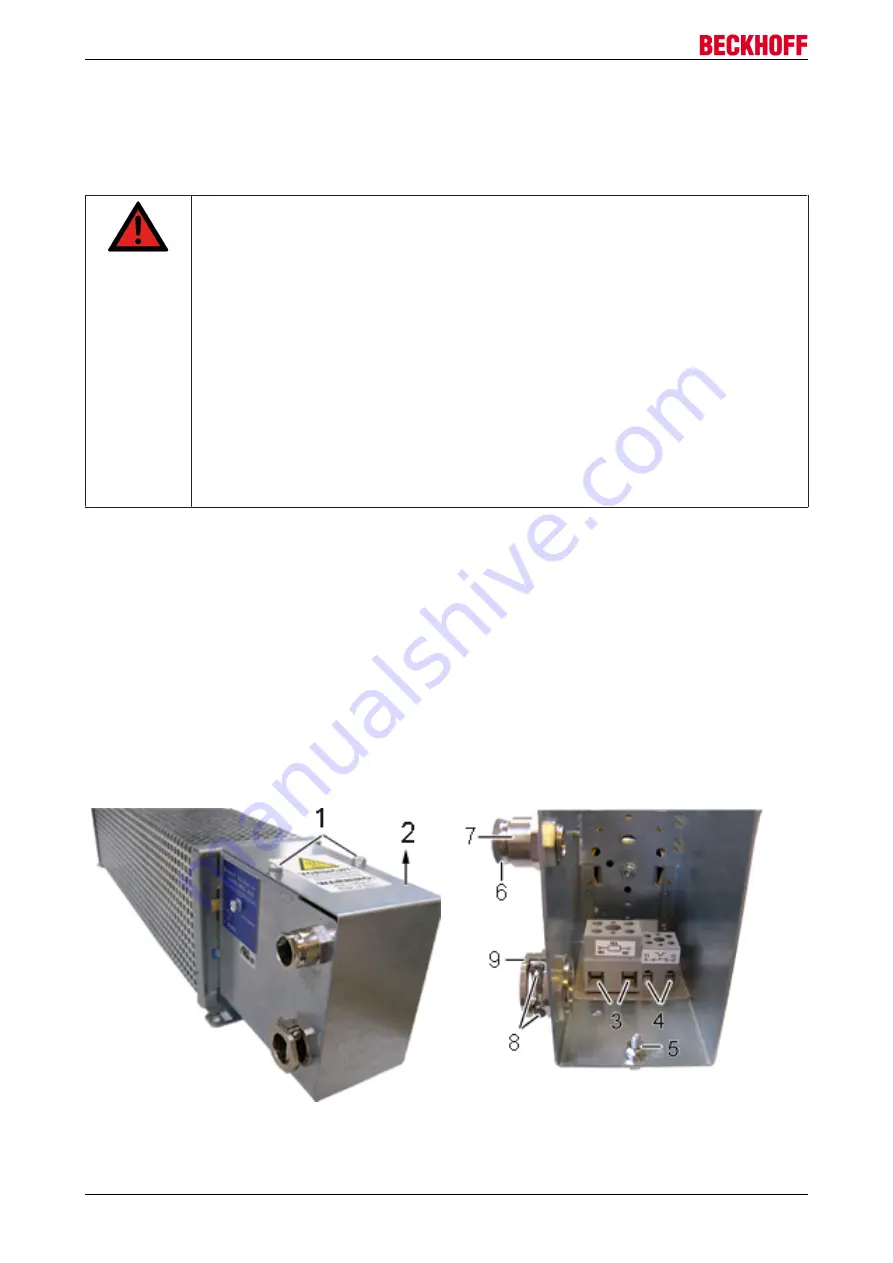
Electrical installation
External brake resistor AX2090-BW5x
12
Version: 1.3
5
Electrical installation
5.1
Important notes
DANGER
Serious risk of injury through electric shock!
Only staff qualified and trained in electrical engineering are allowed to wire up the brake re-
sistors.
• Check the assignment of the servo drive and the brake resistor. Compare the rated
voltage and the rated current of the devices.
• Always make sure that the brake resistors are de-energized during assembly and
wiring, i.e. no voltage may be switched on for any piece of equipment which is to be
connected. Ensure that the control cabinet remains turned off (barrier, warning signs
etc.). The individual voltages will only be turned on again during commissioning.
• Due to the DC link capacitors, the DC link contacts "ZK+ and ZK- (DC+ and DC-)" and
"RB+ and RB-" may be subject to dangerous voltages exceeding 890V
DC
, even after the
servo drive was disconnected from the mains supply.
Wait 5 minutes for the AX5101 - AX5125 and AX520x; 15 minutes for the AX5140/
AX5160/AX5172; 30 minutes for the AX5190/AX5191; 45 minutes for the AX5192/
AX5193 after disconnecting, and measure the voltage at the DC links "ZK+ and ZK-
(DC+ and DC-)". The device is safe once the voltage has fallen below 50 V.
5.2
Connection the brake resistor
Remove the two screws (1) and remove the cover (2) in direction of the arrow. Connect an adequately
dimensioned cable (see chapter "Cables") to the connections (3) of the resistor and the earthing stud (5) and
take it out of the terminal box through the strain-relief assembly (9). Ensure adequate strain relief with the
two screws (8). Connect the other side of the cable to the DC link contact connector "X2" of the AX5000. The
connector is supplied with the AX5000. Connect the earthing cable to the earthing conductor of the control
cabinet.
Connect an adequately dimensioned cable to the potential-free N/C contact (4) of the temperature switch
and take it out of the terminal box through the strain-relief assembly (7) (see chapter "Temperature switch").
Ensure adequate strain relief with the nut (6).
Install the cover (2) in reverse order.