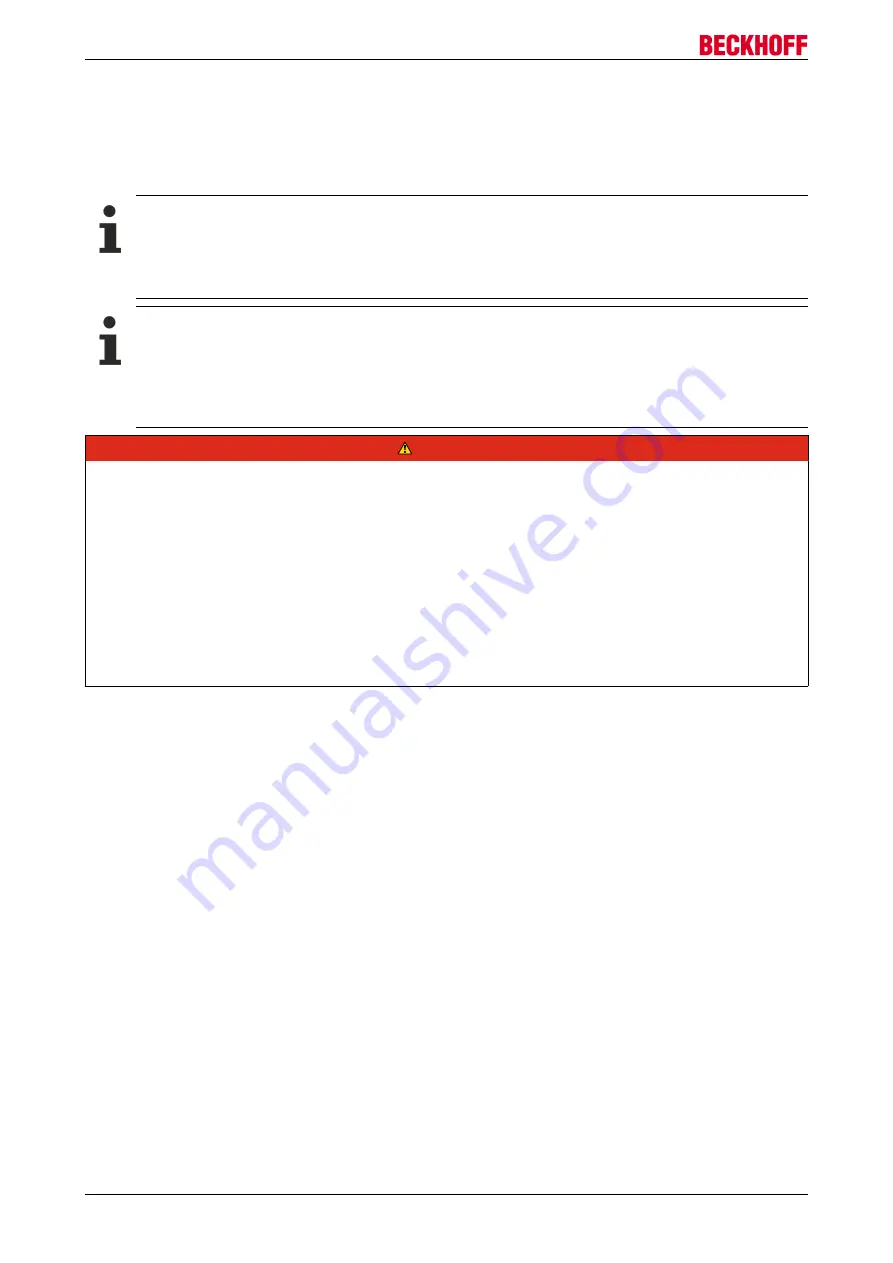
Electrical installation
AL225x Connector-Box
18
Version: 1.9
7
Electrical installation
7.1
Important notes
Assembling the motor cable (at the linear motor)
Strip the wires of the motor cable and fit wire end sleeves.
Twist the shielding of the motor cable and solder a cable with a minimum diameter of 1.5 mm² to it.
Guide the wires through socket "A" in the box and fasten the nut on the socket "A". Fit the shielded
and PE cables with a "PE" connection and the power wires on connection "X1".
Assembling the encoder cable (at the encoder)!
Strip the wires of the encoder cable and fit wire end sleeves!
Twist the shielding of the encoder cable and solder a cable with a minimum diameter of 0.75 mm² to
it. Fit wire end sleeves or a cable lug to the free end. Place the nut of socket "B" over the encoder
cable and feed the wires through the socket "B" in the box and screw the nut onto socket "B". Fit a
"PE" connection to the shielded cable. Wire the signal wires to the "X2" connection as per the table.
DANGER
Serious risk of injury through high electrical voltage!
The connector box must be opened for assembling the cables as described above.
• Make sure all system and machine components and assemblies are de-energized and secured against
unintentional restoration of electrical power.
• Check the earthing of the system or machine and all relevant components and assemblies.
• Remove the motor and feedback cables from the connector box and the servo drive. When removing the
cables from the servo drive, please note that there are residual charges at the DC link contacts of the
servo drive, even after the power has been switched off. Wait 5 minutes for the AX5101 - AX5125 and
AX520x; 15 minutes for the AX5140/AX5160/AX5172; 30 minutes for the AX5190/AX5191; 45 minutes
for the AX5192/AX5193 after disconnecting, and measure the voltage at the DC links "ZK+ and ZK- (DC
+ and DC-)". The device is safe once the voltage has fallen below 50 V.
Summary of Contents for AL-2255-0001
Page 2: ......