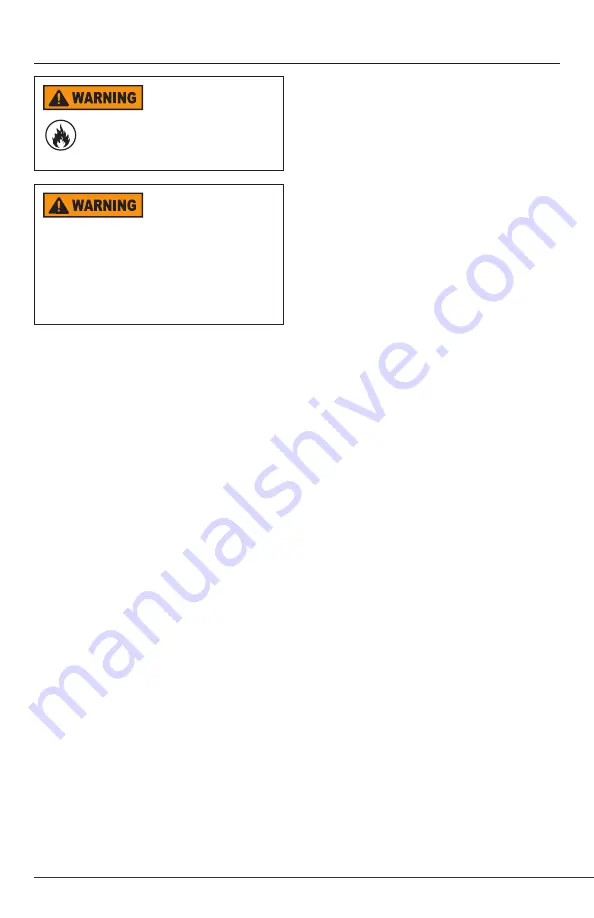
6
Startup / Checkout
If the burner or control fails any of the following
tests, recheck control wiring. If the burner or
control still fails any tests, replace the control.
Starting the System
1. Open the shut-off valves in the supply line
from the oil tank.
2. Close the disconnect switch to supply
power to the burner.
3. Adjust the thermostat or boiler control to
call for heat.
- If the pump has not been primed, refer
to “Priming the Pump” in the “Operation”
section of this manual.
4. Monitor burner operation to ensure that
the burner ignites.
5. End the call for heat. Verify that the
burner turns off before leaving the
installation site.
Check Safety Features
◦
Safe Start Check
1. Place a jumper across the cad cell terminals.
2. Refer to the steps for “Starting the System”
and have the system call for heat.
3. Burner must not start. Verify that the SYS
light is green, FLM light is yellow, and that
the control remains in Standby mode.
4. End the call for heat and remove the cad
cell jumper.
◦
Simulate Flame Failure and Ignition Failure
1. Refer to the steps for “Starting the
System” and have the system call for
heat.
2.
After flame is established and the burner
igniter turns off, close the hand valve in
the oil supply line.
3.
At flame loss, the control will enter
Recycle mode. Verify that the SYS light is
flashing yellow. The control will remain in
Recycle for 60 seconds.
4. After the 60 second recycle period, the
control will try to restart the system.
5. After the 15 second lockout time, the
control will lock out the burner and the
SYS light will flash red. Verify that the
burner motor and igniter are off and that
the burner oil solenoid valve (if used) is
not energized.
6. Open the hand valve in the oil line.
7. Click the ACTION button and verify that the
SYS light shows green and the burner lights.
8. End the call for heat.
◦
Before leaving the installation, verify that all
thermostat and boiler/furnace control wiring
is correct. Consult heating appliance manual
for directions.
Fire Hazard
Reset and Service by Qualified
Technician only.
Carbon Monoxide
Hazard
Do not block combustion air inlet. Failure
to provide adequate air supply could
seriously affect the burner performance
and result in damage to the equipement
and emission of poisnonous carbon
monoxide gas.