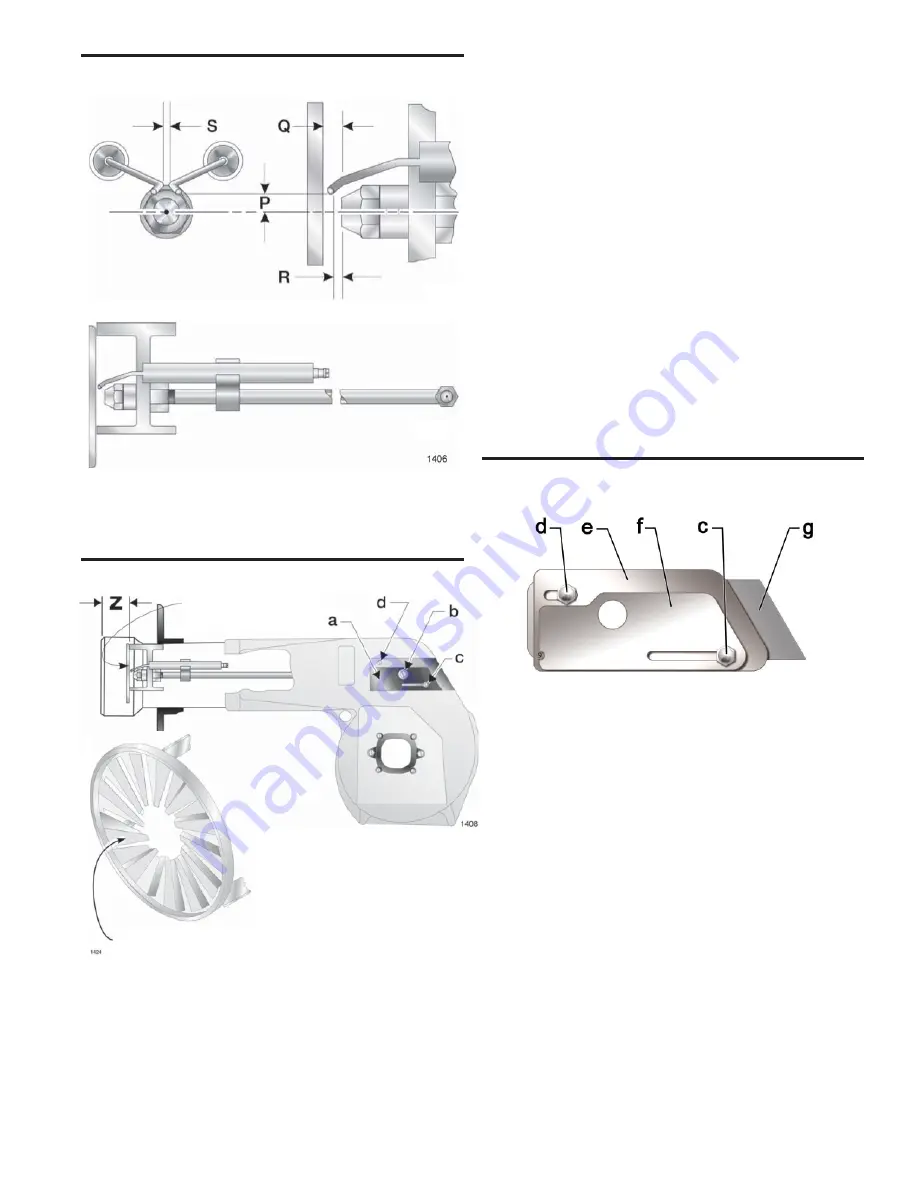
Form 6104 BCF10-R06
9
Critical dimensions -
P
(Electrode spacing) = 3/32”
R
Nozzle center line to electrode tip) = 1/4”
Q
(Nozzle to head) = 1/4”
S
Nozzle face to electrode tip = 1/8”
Figure 5 - Nozzle line assembly in burner
Set dimension Z
Replace the rear access door on the burner, making sure
that the adjusting plate assembly is now securely in the
groove.
Loosen acorn nut
d
in
Figure 5
. Slide the nozzle line and
plate assembly until dimension
Z
in
Figure 5
is
1-3/4” ±
1/16”
. When dimension
Z
(from end of air tube to fl at area
of front face of head) is correctly set, tighten acorn nut
d
.
Verify that the adjusting plate assembly is properly seated
in the adjusting groove.
Attach the oil line from the oil valve to the nozzle line end.
Tighten securely.
Before proceeding, check dimension
Z
once again. Loosen
acorn nut
d
if necessary to reposition the nozzle line. Once
dimension
Z
is set,
do not loosen acorn nut d again
. For
the setting of acorn nut
c
, refer to Page 13.
y
y
y
y
Figure 6 - Adjusting plate assy.
Legend (Figures 5 and 6)
c
Bottom acorn nut
d
Top acorn nut (for setting
dim. Z only
e
Indicator adjusting plate
f
Secondary adjusting plate
g
Primary adjusting plate
Figure 4 - Nozzle and nozzle line assembly
Measure dimension Z from
front (fl at) face of head to
end of air tube, as shown.
Measure dimension Z from the
fl at surface between (not on) the
raised fi ns.
Z
= 1-3/4” ± 1/16”
Install nozzle line assembly
Insert the nozzle line assembly into the burner air tube as
in
Figure 5
.
See
Figures 5
and
6
. Assemble the adjusting plate assem-
bly per the instructions in the assembly packet.
Slide the secondary adjusting plate (item
f
) completely to
the left on the indicator adjusting plate (item
e
). Finger
tighten acorn nut
c
to secure the two plates together. Slide
both plates completely to the left on the primary adjusting
plate (item
g
) and fi nger-tighten acorn nut
d
.
Slide the completed adjusting plate assembly over the noz-
zle line end. Move the plate assembly and the nozzle line
so the plate assembly fi ts into position as shown in
Figure
5
.
Install the spline nut (
Figure 5
, item
b
) on the end of the
nozzle line, leaving the nut loosely placed so the plates can
be moved.
Connect the high-voltage leads from the ignition trans-
former to the electrodes.
y
y
y
y
y
y
Summary of Contents for CF1000
Page 2: ...2 Form 6104 BCF10 R06...