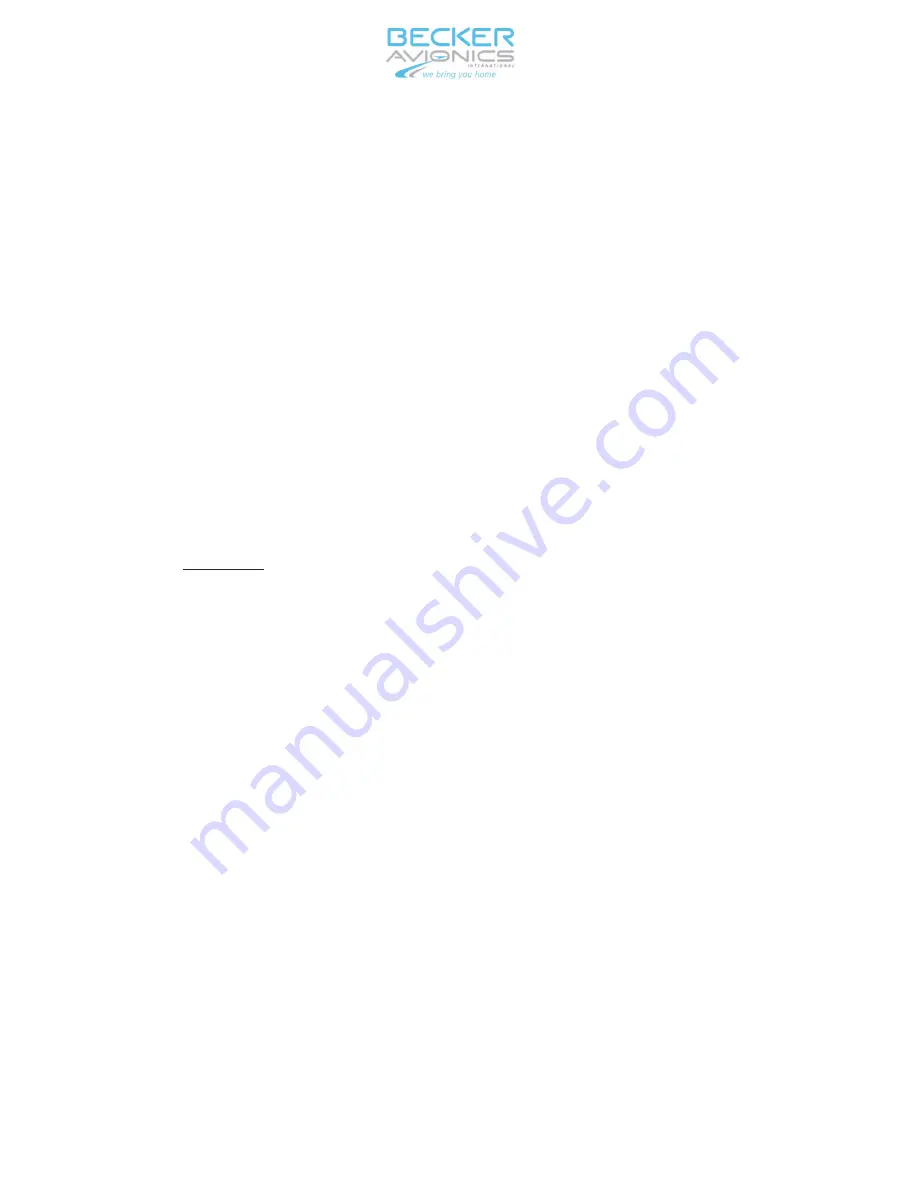
C.
Check of the address module
The installation company has to ensure that the corresponding address
module AM6400-1 is installed with the transponder and that the address
module is programmed correctly. It is recommended to connect the address
module with the aircraft tightly.
D.
Test of transmit frequency
Set code 0000 on the transponder and mode A interrogation on the ramp test
set. Check transmit frequency by means of the ramp test set. Transmit fre-
quency must be 1090
±
1 MHz.
If this is not the case send the transponder to
authorised service.
E.
Check of the transmit power
After installation of equipment and antenna the transmit power has to be che-
cked at the antenna end of the feeder line.
It should fulfill the following requi-
rements:
Requirement:
³
125 W (21 dBW) at class 1 transponder
³
70 W (18.5 dBW) at class 2 transponder
WARNING:
Radiation risk: A safe distance to the installed antenna must be ensured by
corresponding installation measures around human body damage (e.g. at the
eyes) and / or avoid the inflammation of combustible materials by radiated
energy.
Page 2-10
34-50-08
September 2011
INSTALLATION AND OPERATION BXP6401-X-(XX)
Summary of Contents for BXP6401-1 Series
Page 4: ...BLANK INSTALLATION AND OPERATION BXP 6401 X XX ROR Page 2 34 50 08 September 2011 ...
Page 6: ...BLANK INSTALLATION AND OPERATION BXP6401 X XX LEP Page 2 34 50 08 September 2011 ...
Page 10: ...BLANK INSTALLATION AND OPERATION BXP6401 X XX INTRO Page 4 34 50 08 September 2011 ...
Page 12: ...BLANK INSTALLATION AND OPERATION BXP 6401 X XX Page I II 34 50 08 September 2011 ...
Page 22: ...BLANK INSTALLATION AND OPERATION BXP6401 X XX Page II II 34 50 08 September 2011 ...
Page 38: ...Blanc INSTALLATION AND OPERATION BXP6401 X XX Page 2 16 34 50 08 September 2011 ...
Page 40: ...BLANK INSTALLATION AND OPERATION BXP6401 X XX Page III II 34 50 08 September 2011 ...