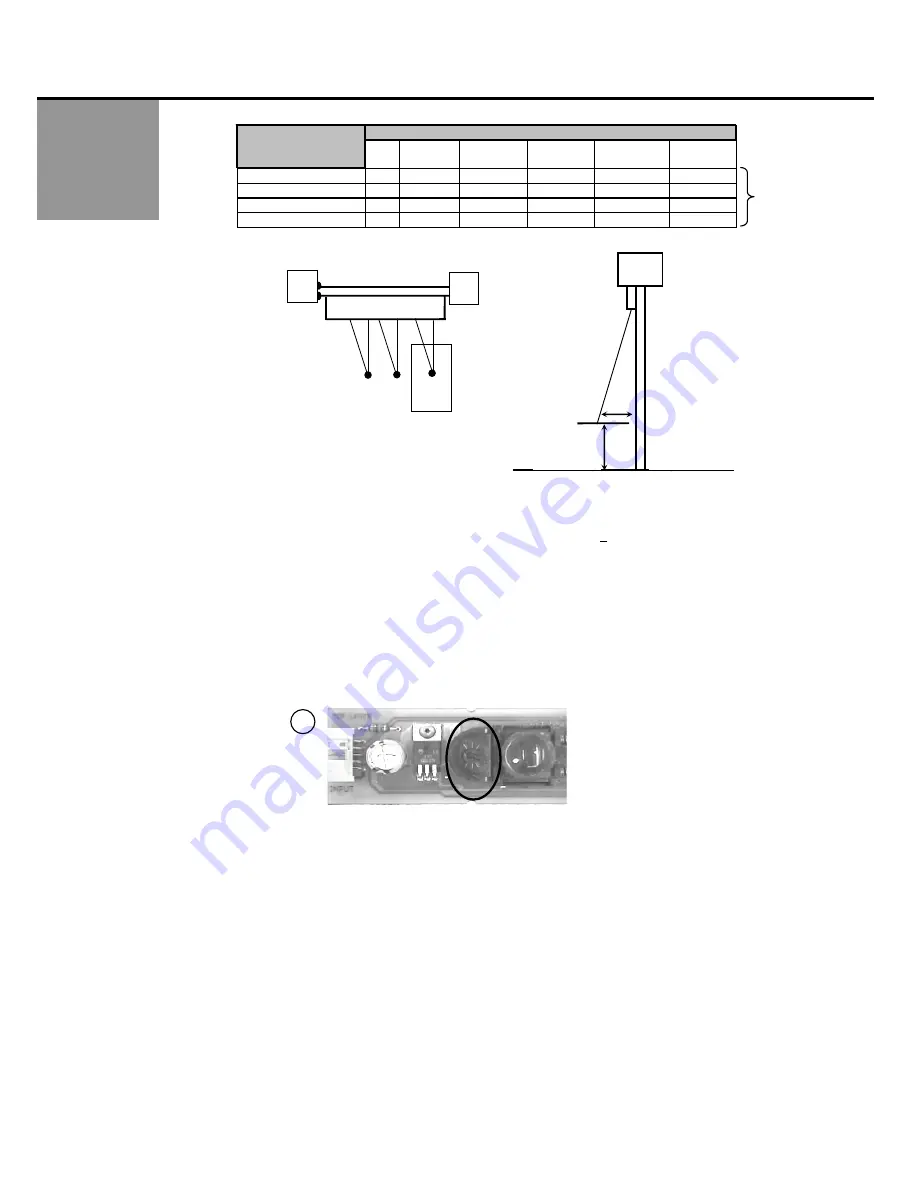
75.0084.05 20110720
Page 10 of 17
POWER-ON
POSITIONING,
ANGLING AND
ADJSUTING THE
MODULES
INACTIVE ZONE
(B) DISTANCE
FROM FLOOR
SUPERSCAN ANGLE (C)
0°
5°
10°
15°
20°
25°
8"
0
6"
12 ½"
19 ¼"
26"
33 ¼"
12"
0
6" 12" 18" 24
½"
31
½"
16"
0
5 ½"
11 ¼"
16 ¾"
23 ¼"
29 ½"
20"
0
5 ¼"
10 ½"
16"
21 ½"
27 ½"
SUPERSCAN
IR
Floor
Cardboard
SIDE VIEW
Dead Zone
Detection
Distance
DOOR
VIEW FROM ABOVE
SUPERSCAN
Cardboard
IR
A
B
A
Note:
Dimension “A” and “B”
are approximate.
3.
The following procedures will be used to adjust each module’s detection zone upon power-on, and must be made with the
Background Analysis jumper set to ‘Normal Mode’. (see page 5)
Power the sensors with 12 to 24 VAC ± 10% or 12 to 24 VDC + 10%. LED status should reflect what was
configured for the relay output. Refer to page 8.
Use a white, gray, or black piece of cardboard about 8" x 11" and hold it as shown in the diagram above.
Move the cardboard from the floor upward until it is detected. This will determine the height of the inactive
area (B distance).
Measure the height at which the cardboard was detected.
If this height does not fall between 12" & 16" above the floor or does not meet your requirements, an
adjustment must be made to the detection distance.
33
Detection Distance Adjustment
One notch of the distance adjustment corresponds to approximately 4".
If Zone B is too high: Turn the distance adjustment clockwise to increase the detection distance and to
decrease Zone B.
If Zone B is too low, turn the distance adjustment counter-clockwise to decrease the detection distance.
Per current ANSI A156.10, 156.27 the detection zone must be within 28” of the floor. Ideally, each detector
should be adjusted so that detection occurs at 12” to 16” above the floor. Less than 12” of Zone B may
result in occasional false triggering of the sensor.
Once all sensors have been adjusted, activate the door several times and allow it to go through a full cycle
each time. Insure that no false triggering is occurring, as would be indicated by the door recycling or
stopping by itself at any point of travel.
Ensure compliance of all applicable safety standards (i.e. ANSI A156.10, 156.27).
Install all remaining covers, end caps, screws, etc.