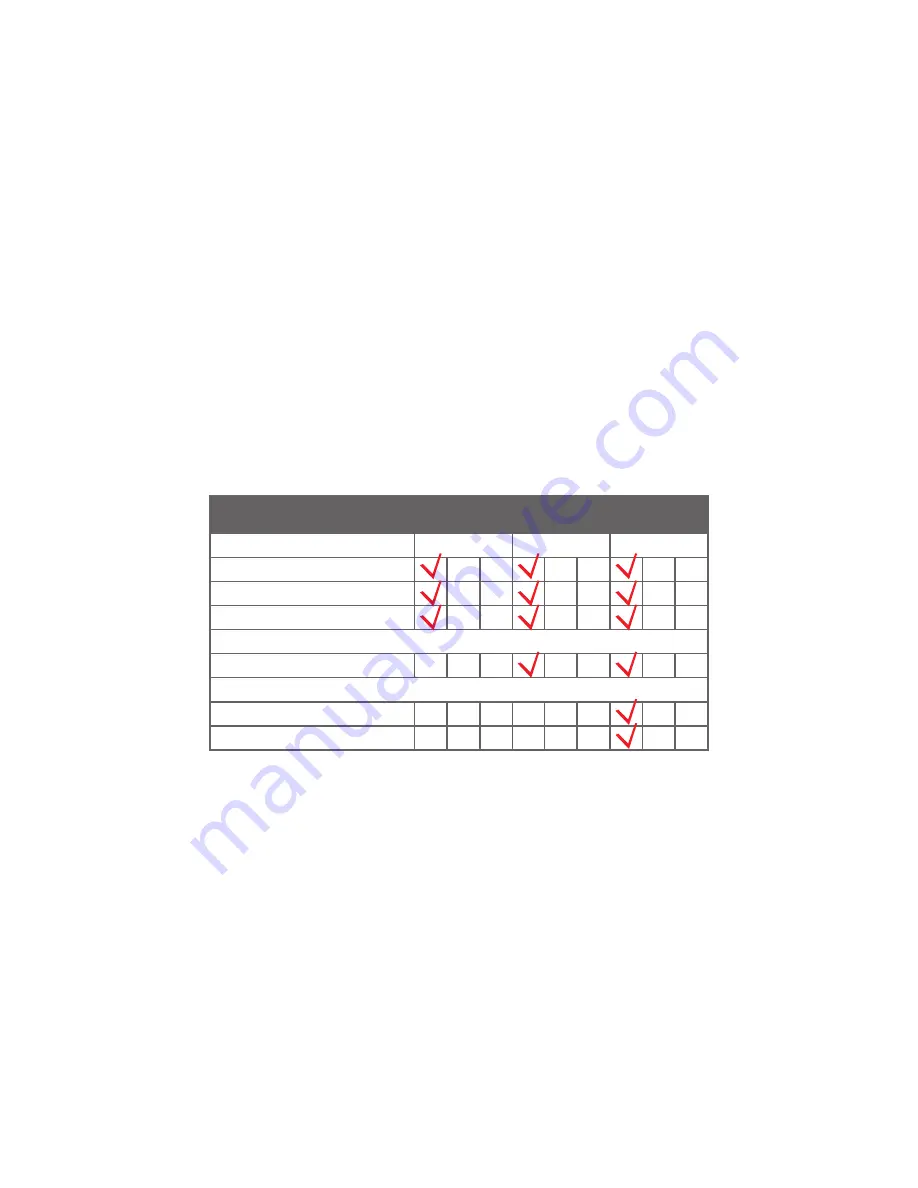
12
BE-AGMZXXX USER MANUAL
EVERY 50 HOURS OF WORK
• Check the correct tension of the driving belt.
• Check that all bolts and nuts are tightened.
• Check the cutters/hammers for wear.
• Check the over-gear unit oil level through plug A (Picture 5).
EVERY 500 HOURS OF WORK
• Check that all bolts and nuts are tightened.
• Change oil in the over-gear unit.
EVERY 1000 HOURS OF WORK
• Replace the driving belt.
GEARBOX MAINTENANCE
• The oil should be drained out and replaced after the first 50 hours of operation.
• Then the oil should be changed every 250 hours, or at least once a year.
• Drain oil form the gearbox thoroughly. Check and clean it. Fill with new gear oil up to the dedicated oil
level.
• The draining procedure is as follows: remove the draining bolt under the gearbox, so that the oil drains off.
After the oil is drained out, put the plug back and fill with gear oil up to the dedicated oil level.
Maintenance Checklis
t
8HRS/Daily
Lubricate PTO Shaft
Check Gear Box Oil Level
Lubricate Caster Wheels
Clean Machine
Lubricate & Clean PTO SHaft Cover
Lubricate Blade Spindle
50HRS/Weekly
Annually
PTO SHAFT MAINTENANCE
The PTO shaft is designed to telescope to allow for dimensional changes as the machine goes through its
operating range. A tubular guard encloses the driving components and is designed to turn relative to the
driving components. The shaft should telescope easily and the guard turn freely on the shaft at all times.
Annual disassembly, cleaning and lubrication is recommended to ensure that all components function as
intended.
To maintain the shaft, follow this procedure:
1. Remove the shaft from the machine.
2. Pull shaft apart.
3. Use a screwdriver to pry the tabs out of the sleeves on each end.
4. Pull the shaft out of the plastic tubular guard.
5. Use a solvent to clean the male and female portions of the telescoping ends.
6. Apply a light coat of grease to each end.
7. Clean the grooves on each end where the tabs are located.
8. Apply a light coat of grease to each groove.
9. Insert the shaft into its respective guard and align the slots with the groove.