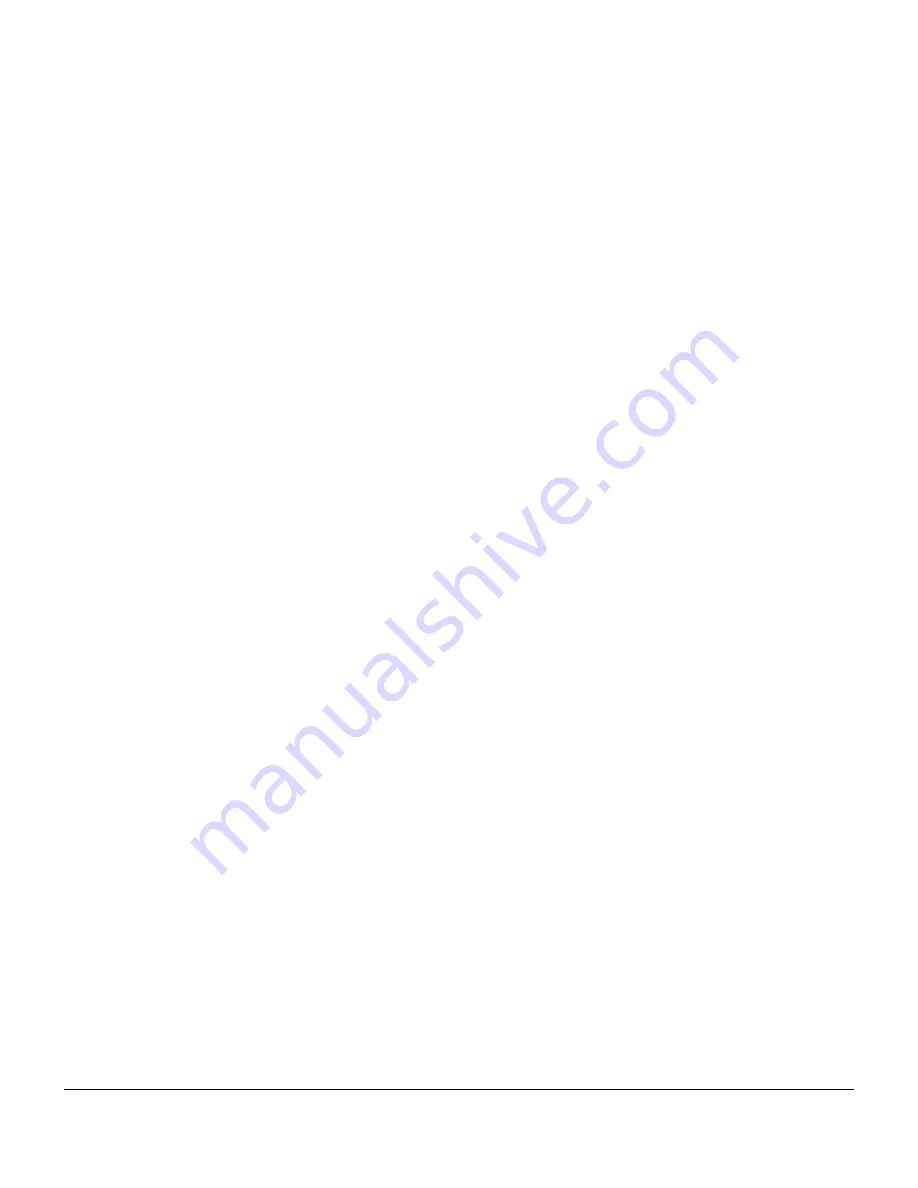
Servicing the Unit – page 10
(See ‘BOILER SERVICING GUIDE’ label on the boiler)
Before servicing the appliance please read the
Important Information section on page 3.
After servicing, complete the relevant section of the
‘Benchmark” Installation, Commissioning and Service Record
Log Book. This should be in the possession of the user.
For economy and safety reasons, it is important to service
the appliance regularly.
1)
Turn off the electrical supply to the boiler.
2)
Remove the front panel of the outer case by pulling
forwards at the top and lifting upwards.
3)
Remove the top panel of the outer case by pulling
upwards.
4)
Turn off the gas supply at the service tap and disconnect
the union (Fig. 7).
5)
Disconnect the electrical socket by pulling upwards (Fig.
7).
6)
Remove the four wing nuts and carefully withdraw the
burner and controls assembly (Fig. 7).
7)
Release the two screws securing the front insulation
assembly and remove the assembly (Fig. 9).
8)
Remove the four thumb screws securing the top inspection
panel. Lift off or slide forward under control facia to
remove. (Fig 10).
9)
60, 50, 40 RS Only - Remove retaining bracket and
casting baffles.
10) Remove any dirt that may have accumulated in the flue
outlet duct.
11) Clean the heat exchanger with a bristle brush and
brush out the bottom of the combustion box ensuring
that the air opening at the rear is clear.
12) 60, 50, 40 RS Only - Refit heat exchanger baffles and
retaining bracket.
13) Check all the insulation panels for damage, replace if
necessary. Refit the front insulation panel, the top
inspection panel.
14) Clean the burner as follows:
a)
Remove the three screws holding the burner to the
door panel.
b)
Clean the burner blades and remove any deposits
from the venturi.
c)
Remove the injector from the feed pipe, clean and
replace.
15) Clean the pilot as follows: Unscrew the pilot tubing nuts at
both ends and remove the pilot tube. Remove and clean
the pilot injector and clean the pilot shroud (Fig 15).
16) Re-assemble the pilot components and then the burner in
reverse order of dismantling.
17) Refit the burner and controls assembly checking that the
door seal is undamaged. Replace if necessary.
18) Reconnect the gas union at the service tap. Turn on the
tap and check for gas soundness.
19) Refit the electrical socket and turn the thermostat to the
OFF position.
20) Refit the outer case top panel.
21) Hold in the ON/OFF button on the gas control valve (Fig 7)
. Press in the igniter button and release. Repeat until the
pilot lights. Hold in the ON/OFF button for a further 20
seconds and then release. The pilot should then stay
alight. (IF THE PILOT FAILS TO REMAIN ALIGHT, TURN
THE ON/OFF BUTTON FULLY CLOCKWISE AND
RELEASE, WAIT 3 MINUTES AND START AGAIN FROM
THE BEGINNING OF THIS PARAGRAPH.) The flame
should be without a yellow tip and be approximately 25mm
(1 in) long. No adjustment of the pilot flame is necessary
as the pilot jet is sized to give the correct flame length at
20 mbar (8 in wg) inlet pressure.
22) Turn on the electricity supply to the boiler.
23) Remove the pressure test point screw (Fig 7). Connect a
pressure gauge and operate the burner by turning the
thermostat knob to its highest setting.
24) Check that the pressure corresponding to the range rated
output is correct for the installation (see data label). If
necessary adjust the appliance throttle (Fig 7).
25) Turn the boiler thermostat to the OFF position and refit the
pressure test point screw.
26) Turn the boiler thermostat to its original setting.
27) Replace the outer case front panel.
28) Complete the relevant section of the “Benchmark”
Installation, Commissioning and Service Record Log and
hand it back to the user.