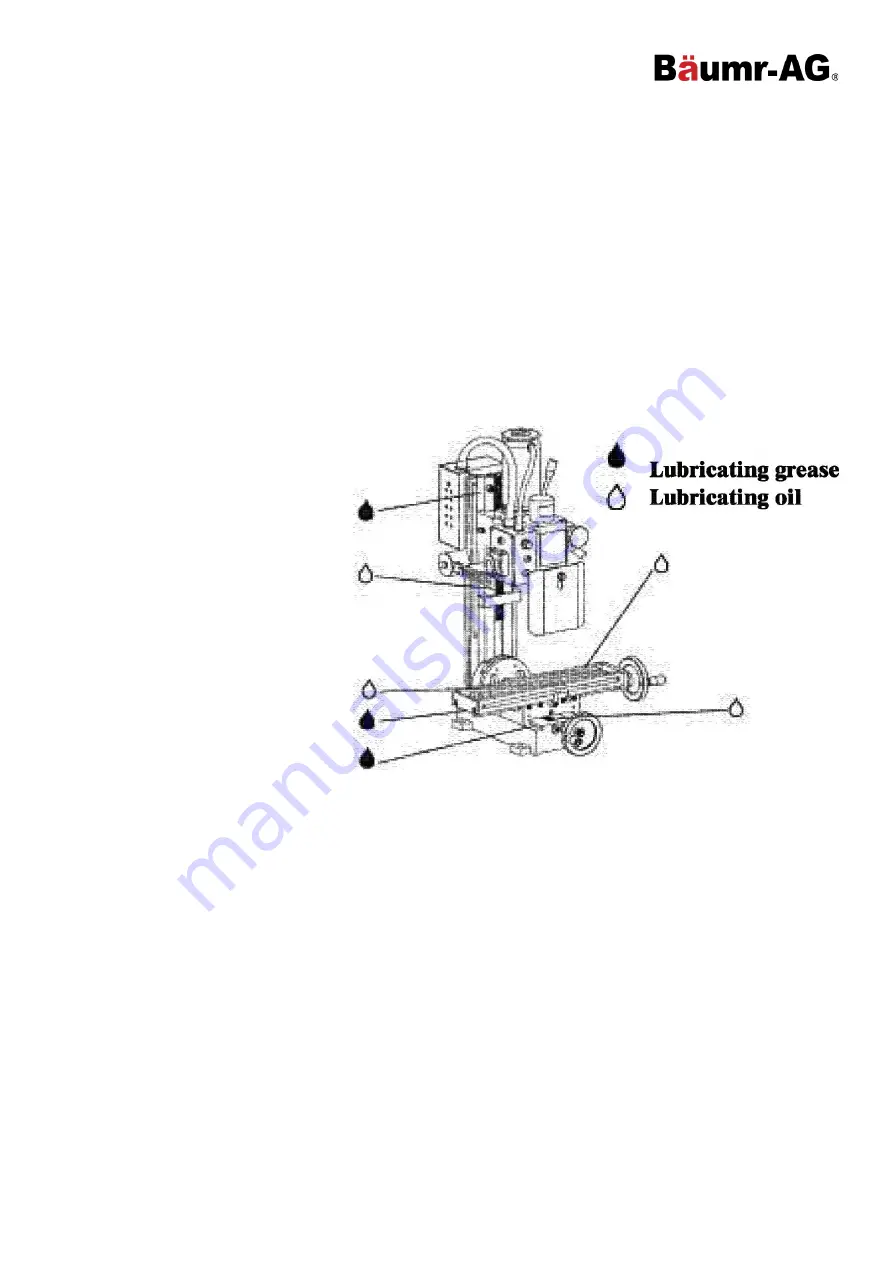
E&OE
© 2020 Baumr-AG
24
•
Sharpen the cutter as soon as it gets blunt. A blunt cutter will make your milling work not only more difficult,
but it can also damage the blade.
Accessories Maintenance
•
Please always keep the taper shank clean.
•
Keep the taper shank and cutter together so the next time you will use them, it will be more convenient for
you.
•
The draw bar and chuck will have their own wrenches. For your convenience, please keep the wrenches
near the machine and ever operate it with inappropriate tools.
•
Please use a wrench to tighten the nuts and never use any other tools, such as a steel hammer, to do so.
Lubrication Mechanics
•
In order to ensure precision, apply
lubrication only on the contact
surface.
•
Use the oil can to lubricate
accessories. Apply some lubricant to
all surfaces before operating the
machine.
The following the parts that needs
lubrication:
Lubricating Oil
•
Basement and saddle seat surface
•
Saddle seat and worktable surface
•
Fuselage sear and connecting strut
surface
Lubricating Grease
•
X-axis feeding screw (saddle seat)
•
Y-axis feeding screw (worktable)
•
Z-axis feeding gear rack (fuselage)
After each work, clean the worktable and lubricate it with a little lubricant for protection.