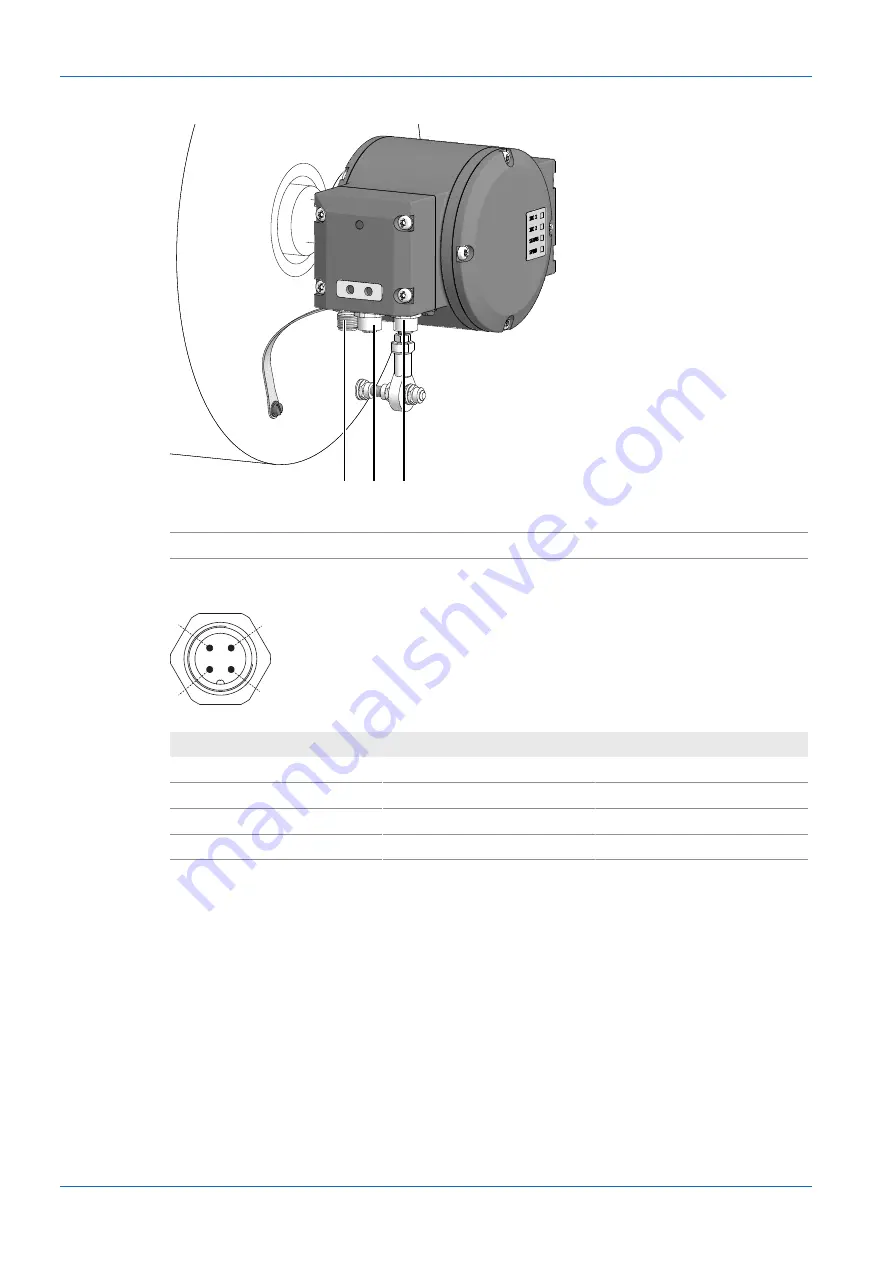
6
|
Electrical installation
Baumer Hübner
26
Operating Manual
HMG10 & HMG10P EtherNet/IP | V1, T1
6.1.2
Pin assignment EtherNet/IP
1
2
2
Ill. 4:
Connections HMG10 EtherNet/IP
1
Mating connector (4-pin, A-coded)
2
Mating connector (4-contact, D-coded)
6.1.2.1
Mating connector (4-pin, A-coded)
1
2
3
4
Ill. 5:
Mating connector (4-pin, A-coded)
Pin
Connection
Description
1
UB
Operating voltage 10-30 V DC
2
-
Do not use
3
GND
Ground connection for UB
4
-
Do not use